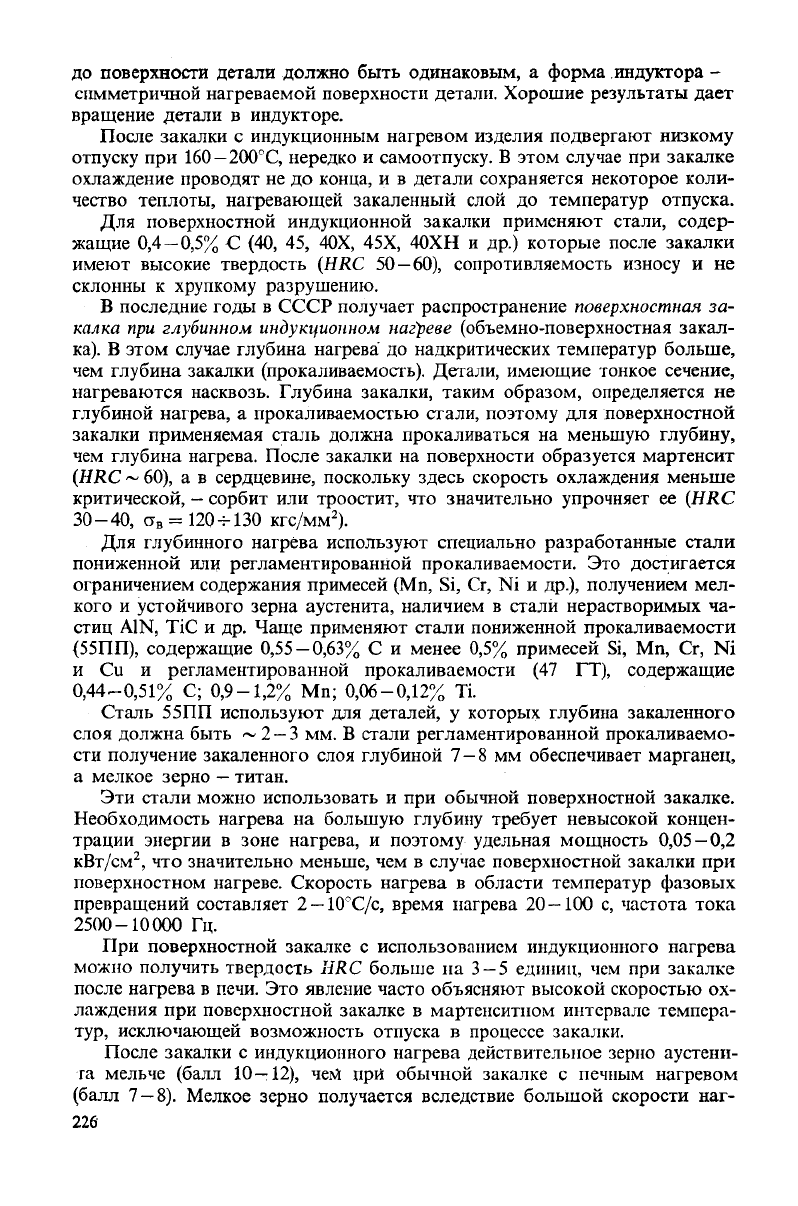
до поверхности детали должно быть одинаковым, а форма индуктора -
симметричной
нагреваемой поверхности детали. Хорошие результаты
дает
вращение детали в индукторе.
После
закалки с индукционным нагревом изделия подвергают низкому
отпуску при
160—200°С,
нередко и самоотпуску. В этом
случае
при закалке
охлаждение проводят не до конца, и в детали сохраняется некоторое коли-
чество теплоты, нагревающей закаленный слой до температур отпуска.
Для поверхностной индукционной закалки применяют стали, содер-
жащие
0,4—0,5%
С (40, 45, 40Х, 45Х, 40ХН и др.) которые после закалки
имеют высокие твердость (HRC 50
—
60), сопротивляемость износу и не
склонны
к хрупкому разрушению.
В последние годы в
СССР
получает распространение
поверхностная
за-
калка при
глубинном
индукционном
нагреве
(объемно-поверхностная закал-
ка).
В этом
случае
глубина нагрева до надкритических температур больше,
чем глубина закалки (прокаливаемость). Детали, имеющие тонкое сечение,
нагреваются насквозь. Глубина закалки, таким образом, определяется не
глубиной нагрева, а прокаливаемостью стали, поэтому для поверхностной
закалки
применяемая сталь должна прокаливаться на меньшую глубину,
чем глубина нагрева. После закалки на поверхности образуется мартенсит
(HRC ~ 60), а в сердцевине, поскольку здесь скорость охлаждения меньше
критической,
— сорбит или троостит, что значительно упрочняет ее (HRC
30-40,
ст
в
=
120н-130
кгс/мм
2
).
Для глубинного нагрева используют специально разработанные стали
пониженной
или регламентированной прокаливаемое™. Это достигается
ограничением содержания примесей (Mn, Si, Cr, Ni и др.), получением мел-
кого и устойчивого зерна аустенита, наличием в стали нерастворимых ча-
стиц
A1N, TiC и др. Чаще применяют стали пониженной прокаливаемости
(55ПП),
содержащие 0,55
—
0,63% С и менее 0,5% примесей Si, Mn, Cr, Ni
и
Си и регламентированной прокаливаемости (47 ГТ), содержащие
0,44-0,51% С;
0,9-1,2%
Мп;
0,06-0,12%
Ti.
Сталь 55ПП используют для деталей, у которых глубина закаленного
слоя
должна быть ~ 2
—
3 мм. В стали регламентированной прокаливаемо-
сти получение закаленного слоя глубиной 7
—
8 мм обеспечивает марганец,
а мелкое зерно — титан.
Эти
стали можно использовать и при обычной поверхностной закалке.
Необходимость нагрева на большую глубину
требует
невысокой
концен-
трации
энергии в зоне нагрева, и поэтому удельная мощность
0,05-0,2
кВт/см
2
, что значительно меньше, чем в
случае
поверхностной закалки при
поверхностном нагреве. Скорость нагрева в области температур фазовых
превращений
составляет 2
—10°С/с,
время нагрева 20
—
100 с, частота тока
2500-10000
Гц.
При
поверхностной закалке с использованием индукционного нагрева
можно
получить твердость HRC больше на 3
—
5 единиц, чем при закалке
после нагрева в печи. Это явление часто объясняют высокой скоростью ох-
лаждения при поверхностной закалке в мартенситном интервале темпера-
тур, исключающей возможность отпуска в процессе закалки.
После
закалки с индукционного нагрева действительное зерно аустени-
та мельче (балл 10—12), чем при обычной закалке с печным нагревом
(балл 7
—
8). Мелкое зерно получается вследствие большой скорости наг-
226