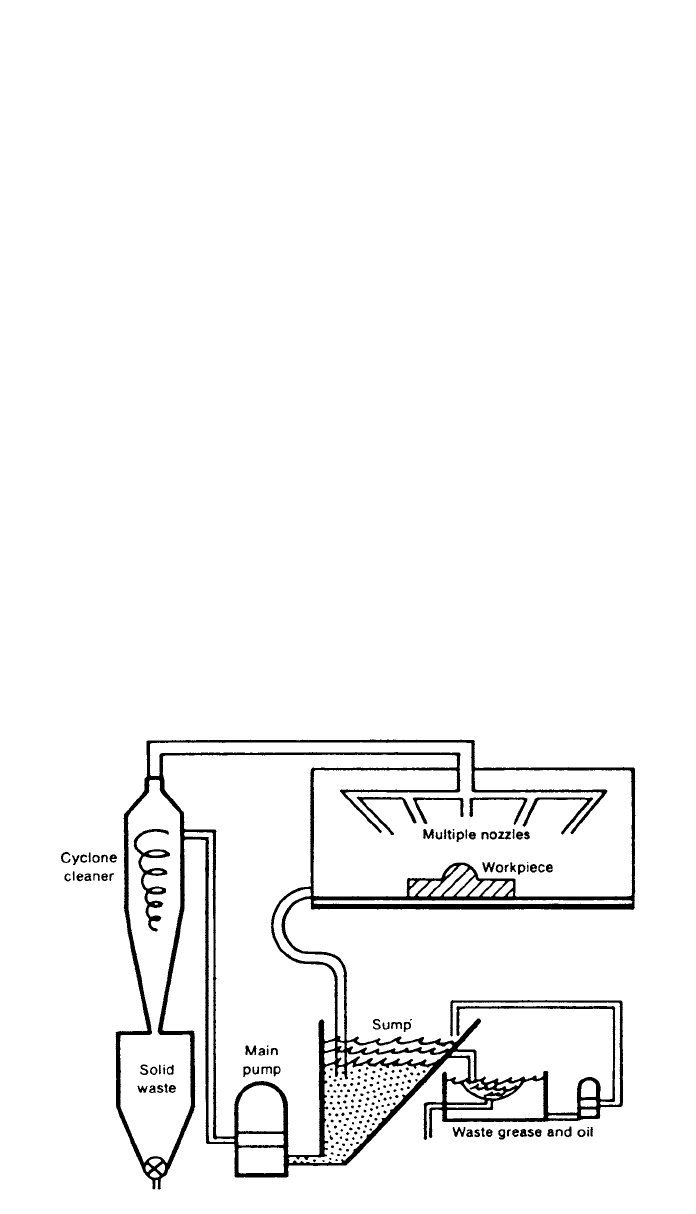
908 PRODUCTION PROCESSES AND EQUIPMENT FOR METALS
Fig. 38 Water-jet machining.
that operates in the region from 250–1000 psi (1.7–6.9 Mpa); and one for
smaller parts and production shop situations that uses pressures below 250 psi
(1.7 Mpa).
The first version, or high-pressure range, is characterized by use of a pumped
water supply with hoses and nozzles that generally are hand-directed. In the
second version, more production-oriented and controlled equipment, such as that
shown in Fig. 38, is involved. In some instances, abrasives are added to the fluid
flow to promote rapid cutting. Single or multiple-nozzle approaches to the work-
piece depend on the size and number of parts per load. The principle is that
WJM is high-volume, not high-pressure.
16.10 Electrochemical Deburring
Electrochemical deburring (ECD) is a special version of ECM (Fig. 39). ECD
was developed to remove burrs and fins or to round sharp corners. Anodic dis-
solution occurs on the workpiece burrs in the presence of a closely placed ca-
thodic tool whose configuration matches the burred edge. Normally, only a small
portion of the cathode is electrically exposed, so a maximum concentration of
the electrolytic action is attained. The electrolyte flow usually is arranged to
carry away any burrs that may break loose from the workpiece during the cycle.
Voltages are low, current densities are high, electrolyte flow rate is modest, and
electrolyte types are similar to those used for ECM. The electrode (tool) is
stationary, so equipment is simpler than that used for ECM. Cycle time is short
for deburring. Longer cycle time produces a natural radiusing action.
16.11 Electrochemical Discharge Grinding
Electrochemical discharge grinding (ECDG) combines the features of both elec-
trochemical and electrical discharge methods of material removal (Fig. 40).