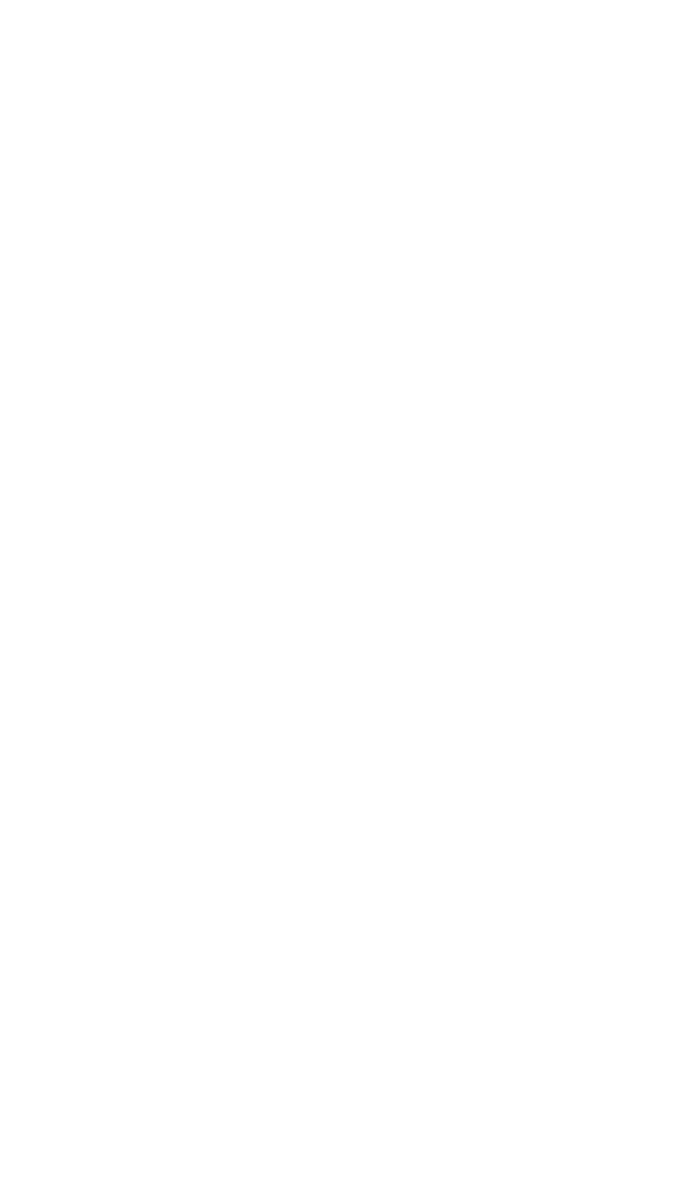
150 COPPER AND COPPER ALLOYS
6.2 Electrical and Electronic Alloys
Electrical and electronic connectors, contacts, leadframes and components of
switches, relays, and similar products form another important use of copper
metals. The principal property of concern here is electrical conductivity, followed
by formability, corrosion resistance, and spring properties, i.e., the ability to
maintain required contact forces. (Thermal conductivity roughly parallels elec-
trical conductivity, and like electrical conductivity, it decreases with increasing
concentrations of alloying elements.) The ability to retain mechanical properties
at moderately elevated temperatures is also important. This property, known as
stress-relaxation resistance, is important in high-current-carrying components,
components that require constant contact forces over time and products that are
subjected to high ‘‘burn-in’’ currents during testing. Mechanical properties of
sheet, strip, and plate alloys, including those used in electrical and electronic
applications, are listed in Table 4.
The copper alloy most commonly used in electrical connectors is cartridge
brass, UNS C26000. The alloy’s electrical conductivity is only 28% that of pure
copper, but that is sufficient for many applications. C26000 is also the most
formable of the brasses, and its ductility enables complex connectors to be pro-
duced at high speed. Brasses containing less than the 30% zinc found in C26000
have higher conductivity, but they are somewhat weaker and less formable. No
practical benefit is gained by adding more than 30% zinc to brass for electrical
connectors.
Phosphor bronzes comprise the next-most popular group of connector alloys.
The phosphor bronzes trade-off conductivity for higher strength and are used to
provide high contact forces when electrical conductivity is not a prime concern.
Conversely, they can provide equivalent contact force with less metal. With
innovative design, reducing the weight of material required for each contact can
often offset the cost penalty for alloys carrying a higher price per pound.
Unlike the brasses, which offer a wide range of electrical conductivity (28–
56% IACS), conductivities of phosphor bronzes range from only 11 up to 20%
IACS, although there are exceptions. Conductivity of phosphor bronze A (5%
tin, UNS C51000), the leading alloy, is 15% IACS, only about one-half that of
C26000, but it is twice as strong.
Phosphor bronze C (C52100) is another popular alloy in this family. With
8% tin and a small amount of phosphorus, it is stronger but not so highly
conducting as C51000. Alloy UNS C51100 offers somewhat higher conductivity
than C51000 and C52100 and is also frequently used. These alloys are available
in strip form in a variety of tempers. See the data tables for conductivity and
mechanical properties.
Coppers containing small quantities of tellurium, zirconium, magnesium, cad-
mium (now in disfavor due to its adverse effects on the environment), chromium,
and iron, in some cases in combination with phosphorus, can provide conduc-
tivity of around 80–90% IACS with yield strengths between about 35 and 70
ksi (240 and 480 MPa).
High-copper alloys offer combinations of high conductivity and high me-
chanical properties. Typical alloys in this class include chromium–coppers such
as C18200 and C18400; copper–iron–phosphorus alloys (C19210, C19400, and