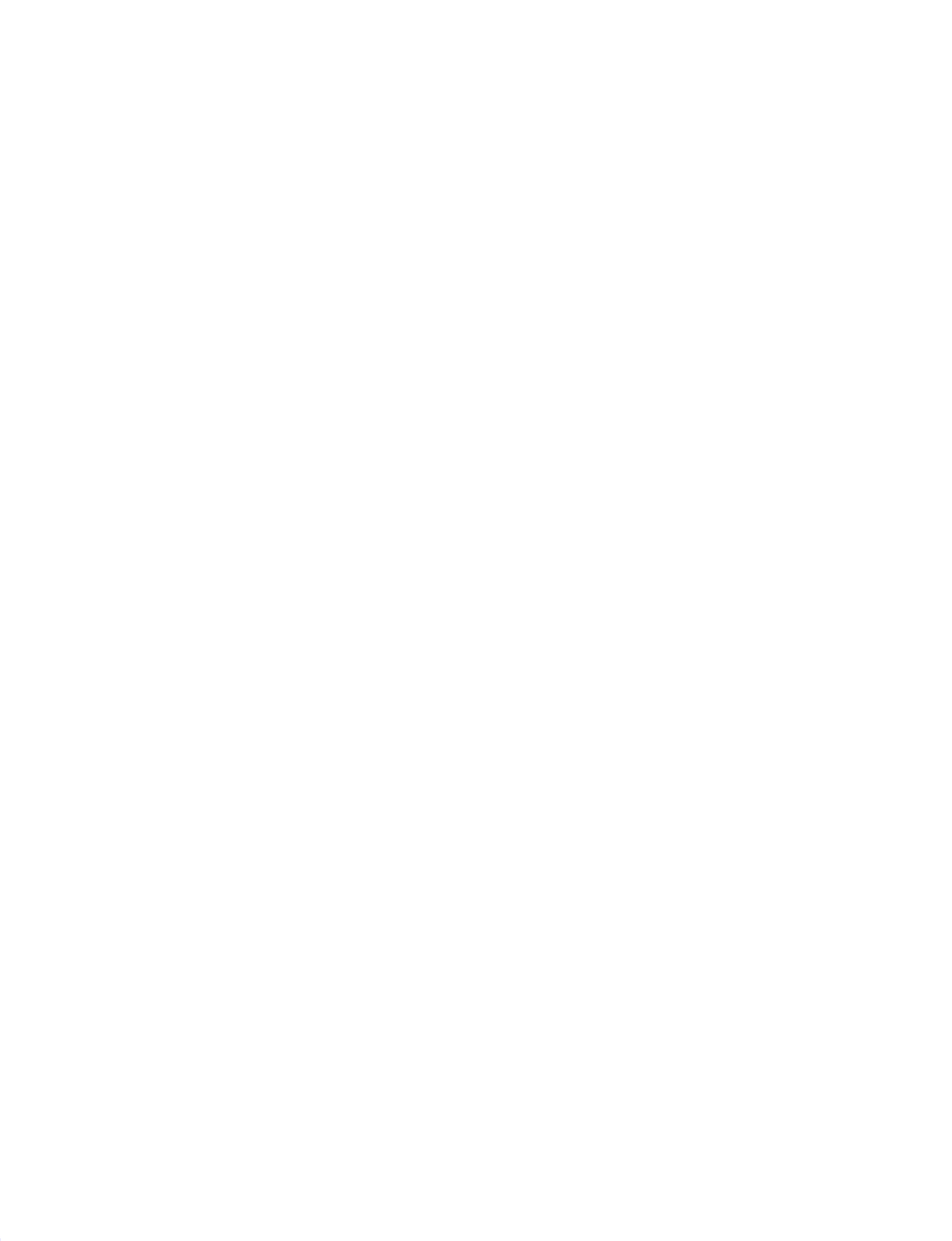
Таким образом, магнитотвердые материалы должны иметь высокие
значения B
r
, Н
с
, магнитной энергии В · Н и сохранять их во времени.
Наиболее высокие значения коэрцитивной силы характерны для сталей
или сплавов с наивысшей физической твердостью. Высокая твердость
достигается закалкой на мартенсит или дисперсионным твердением.
Углеродистые стали, закаливающиеся на мартенсит (легированные) и
безуглеродистые сплавы (дисперсно-твердеющие) применяют в
промышленности для постоянных магнитов.
Размагничивание связано с наличием примесей, при этом идет
смещение стенок доменов и вращение векторов намагничивания.
Необратимость этих эффектов приводит при перемагничивании к
образованию петли гистерезиса. При различном химическом составе и
структуре доля участия каждого фактора различна, но основным считают
вращение векторов. Значения коэрцитивной силы зависят от
кристаллографической анизотропии К и намагниченности насыщения М
s
.
Максимальное значение имеет кобальт, минимальное – никель, поэтому
кобальт используют для постоянных магнитов.
Высокие значения В
r
, Н
с
, В∙Н отмечаются у следующих материалов:
сталей в мартенситном состоянии, сплавов системы Fe–Ni–Al–Co (АЛНИКО),
интерметаллидов, РЗМ, сплавов кобальта, соединений Nd–Fe–B, ферритов.
Легирование такими элементами, как W, Cr, Co, Mo, повышает
устойчивость мартенситной структуры.
Для изготовления магнитов применяют высокоуглеродистые стали
(чаще с 1,0 % С), легированные хромом (3,0 %) – ЕХЗ, вольфрамом (6,0 %) –
ЕВ6; одновременно хромом и кобальтом – ЕХ5К5, ЕХ9К15М2 (ГОСТ 6862-
71). Легирующие элементы повышают коэрцитивную силу, остаточную
индукцию и улучшают температурную стабильность и стойкость
постоянного магнита к механическим ударам. Хромистые, вольфрамовые и
кобальтовые стали легко обрабатываются давлением и резанием, но
обладают относительно малой магнитной энергией, поэтому их применяют
для неответственных магнитов массового производства. Коэрцитивная сила
легированных сталей составляет 60–180 Э, остаточная индукция – 8 000–10
000 Гс. Наиболее высокие магнитные свойства у сталей ЕХ5К5 и ЕХ9К15М2
после нормализации, высокого отпуска, закалки и низкого отпуска (при
100
о
С).
Наибольшее промышленное значение имеют сплавы типа АЛНИКО. Они
тверды, хрупки и не поддаются деформации, поэтому магниты
изготавливают литьем, а затем проводят только шлифование.
Высокие магнитные свойства сплавы получают после нагрева до
1250–1280
о
С и дальнейшей закалки с определенной (критической) для
каждого сплава скоростью охлаждения; после закалки следует отпуск при