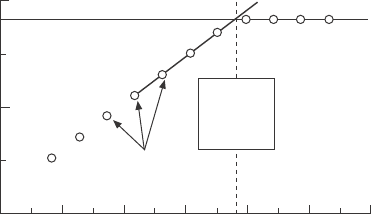
115In situ spectroscopic ellipsometry (SE)
© Woodhead Publishing Limited, 2011
to the aluminum source for composition control. Though the composition
prole was controlled, well-width was established assuming growth rates
from previous calibration.
Multi-wavelength ellipsometry expanded the ability to control processes
in real-time. Growth-rate control of CdTe from metal-organic vapor phase
epitaxy (MOVPE) was demonstrated using a 12-wavelength ellipsometer
(Johs et al., 1993). The feedback of voltage to the Cd mass ow controller
was limited to every 3 seconds due to data acquisition and computer speed at
the time. kildemo, et al. (1996) used a three-wavelength in situ ellipsometry
measurement to control PECVD deposition of optical coating multilayers
with 1% accuracy. Because the coatings were transparent, a standard VI
approach was not successful. Instead, they predicted data trajectories in
advance of deposition for the measured structure. During the process, the
layer deposition was stopped when real-time experimental data approached
the calculated end-points.
Herzinger et al. (1996) demonstrated multilayer growth control of an
8-period Bragg reector structure with a VI approach that considers multiple
measurement times to adjust the model interface. Although analysis on a
90 MHz Pentium computer required 3 to 8 seconds per measurement time-
point, precise shutter control was achieved through stop-point predictions
based on the most recent measured thicknesses, as shown in Fig. 5.16.
Successful control to 1.3% thickness accuracy was achieved using a 44-
wavelength ellipsometer under non-ideal conditions (beam wobble, window
birefringence, and non-optimum angle) with an intentionally drifting process.
Today, modern computers and advanced SE systems with hundreds or even
thousands of wavelengths make in situ SE control signicantly better and
easier.
SE data
points
Target thickness
Shutter
close
time
9.9 10.2 10.5 10.8 11.1 11.4 11.7
Time (min)
Layer thickness (Å)
600
500
400
5.16 Demonstration of MBE growth control for a 583 Å GaAs layer
(adapted from Herzinger et al., 1996, with permission from the
Materials Research Society).