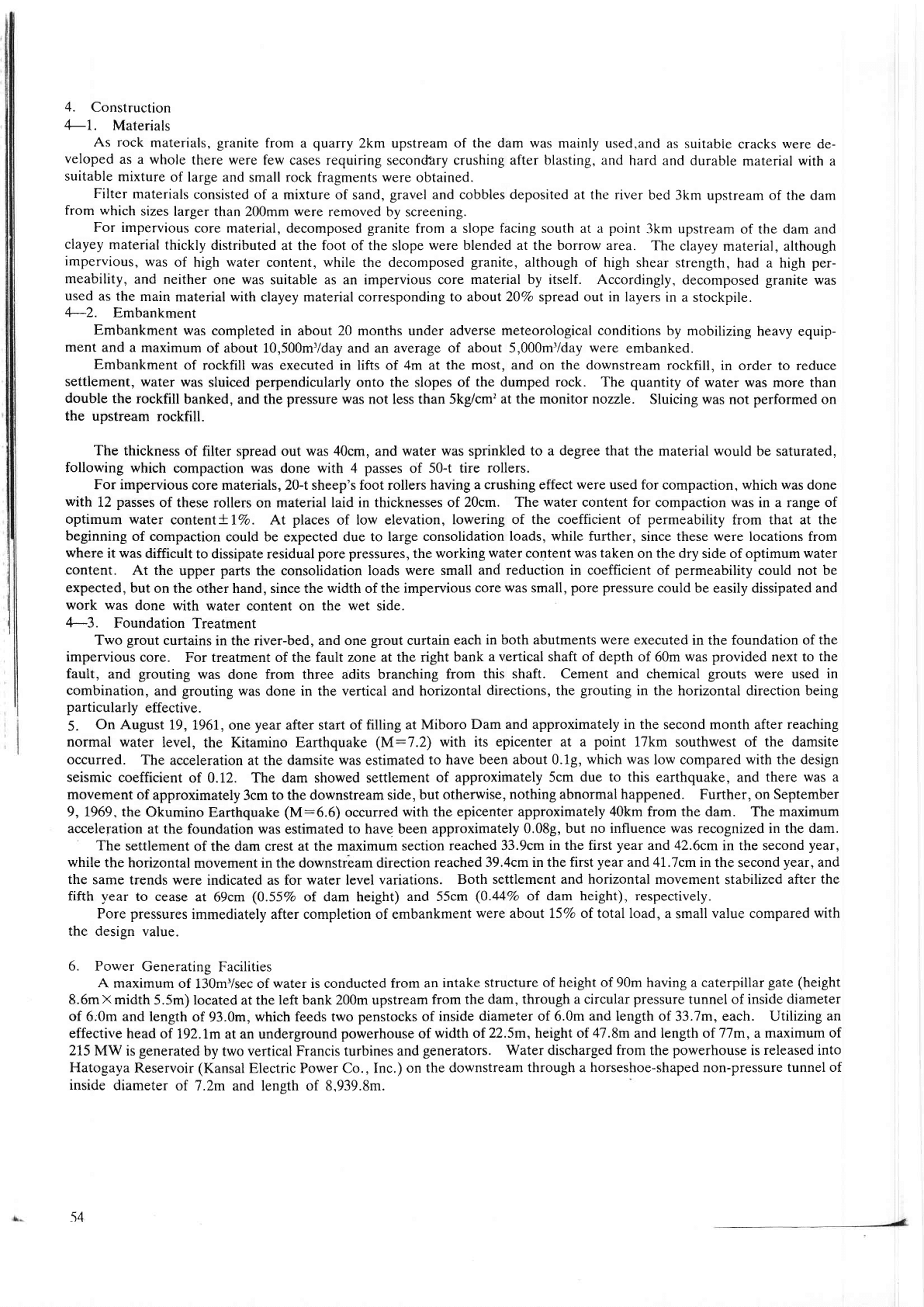
4. Construction
4-1.
Materials
As rock
materials, granite
from a
quarry
2km upstream of the dam was mainly used,and
as suitable
cracks
were
de-
veloped
as a whole
there were
few cases requiring secondary crushing after blasting, and hard
and durable material with
a
suitable
mixture
of large and
small rock fragments w€re obtained.
Filter materials
consisted of a mixture of
sand,
gravel and cobbles deposited at the river
bed 3km
upstream of the darn
from which
sizes larger
than 200mm
were
removed by screening.
For impervious
core material, decomposed
granite
from a slope
facing
south at a
point
3km upstream
of the dam and
clayey
material
thickly distributed
at the foot of the slope
were blended at the borrow area.
The clayey
material, although
impervious,
was of high water
content,
while
the decomposed
granite,
although of high shear strength,
had a high
per-
meability,
and neither
one
was
suitable as an impervious core
material by itself. Accordingly,
decomposed
granite
was
used as the
main material with
clayey
material
colresponding
to abolut2oEo spread out in layers
in a stockpile.
4--2.
Embankment
Embankment
was completed in about 20 months under adverse meteorological conditions by mobilizing
heavy equip-
ment
and a maximum
of about 10,500m'/day and ar average of about 5,000mr/day were embanked.
Embankment
of rockfill was executed in lifts of 4m at th€
most, and
on
the downstream
rockfill,
in order
to reduce
settlement, water
was
sluiced
perpendicularly
onto the
slopes of the dumped rock. The
quantity
of water was more than
double
the rockfill banked,
and the
pressure was
not less than
skg/cm'! at the monitor nozzle.
Sluicing was not
performed
on
the upstream
rockfill.
The thickness
of lilter spread out
was
40cm, and
water was sprinkled to a degree that the mate
al
would
be saturated,
following which
compaction was done with 4
passes
of 50-t tire
rollers.
For impervious
core materials, 20-t sheep's foot rollers having
a crushing effect were used
for compaction, which
was
done
with
1.2
passes
of these
rollers on material
laid in thicknesses of 20cm. The
wat€r
content for compaction was in a range of
optimum
water conlentllVo. At
places
of
low elevation, lowering of the coefficient of
permeability
ftom that at the
beginning
of compaction
could be expected due to large
consolidation loads, while further, since these were locations from
where
it was
difficult to dissipate residual
pore pressures,
the
working water content was taken on the dry
side of optimum
water
content.
At the
upper
parts
the consolidation
loads were small and reduction in coefficient of
permeability
could not be
expected,
but on the other hand, since the width of the impervious
cote was small,
pore pressure
could
be easily dissipated and
work was
done with
water content on the
wet
side.
4-3. Foundation
Treatment
Two
grout
curtains
in the dver-bed,
and
one
grout
ortain each
in both abutments were executed
in the foundation of
the
impervious core.
For treatnent of the fault
zone at the right bank
a vertical
shaft
of depth
of 60m
was provided
next to
the
fault, and
grouting
was done ftom three adits branching
from this shaft. Cement and chemical
grouts
were used
in
combination,
and
grouting
was done in the vertical and horizontal
directions, the
grouting
in tlle horizontal direction being
pa
icularly
effective.
5.
On August 19,
1961, one
year
after start of
filling at Miboro
Dam and approximately in the
second month after
reaching
normal water
level,
the
Kitamino Earthquake
(M:7.2) vrith its epicenter at a
point
1.7km southwest of the damsite
occurred. The
acceleration at the damsite was estimated
to have beeD about 0.1g,
which was
lolv compared with the design
seismic
coefficient of
0.12. The
dam showed settlement of
approximately 5cm due to this earthquake, and there was a
movement
of approximately
3cm to the
downstream side, but otherwise,
nothing abnormal happened. Further, on September
9, 1969. the
Okumino Earthquake
(M:6.6)
occuned
with the epicenter approximately
40km
from the dam. The maximum
acceleration
at the foundation was estimated to have been
approximately 0.089, but
no influence
was recognized in th€
dam.
The settlement
of the
dam crest at the maximum section
reached 33.9cm in the first
year
and 42.6cm in the s€cond
year,
while
the horizontal
movement in the
downstream direction reached
39.4cm in the first
year
and 41.7cm in
the second
year,
and
the same
trends were indicated as for lvater level
variations. Both settlement and horizontal movement stabilized after
the
fifth
year
to cease
at 69cm
(O.55Va
of dam height)
and 55cm
(0-44Vo
of
dam height), respectively.
Pore pressures
immediately
after
completion of embankment
were
about 1570 of total load, a small value compared
with
the design value.
6. Power
Generating Facilities
A maximum
of 130m3/sec of
water
is conducted
from an intake
structure of height of 90m having a caterpillar
gate (height
8.6m
x
midth
5.5m) located at the left bank 200m upstream
ftom the
dam, through a circular
pressure
tulnel of
inside diameter
of 6;0m and length
of 93.0m, which feeds two
penstocks
of inside
diameter of
6.0m
and length
of 33.7m, each. Utilizing
an
effective
head of 192.1m
at an underground
powerhouse
of
width of 22.5m, height of
47.8m
and length of 77m, a maximum
of
215
MW is
generated
by two
vertical Francis turbines and
generators. Water
discharged from the
powerhouse
is
released into
Hatogaya
Reservoir
(Kansal
Electric Power Co., Inc.)
on the downstream
through a horseshoe-shaped non-pressure tunnel of
inside
diameter of
7.2m and leneth of 8.939.8m.
54