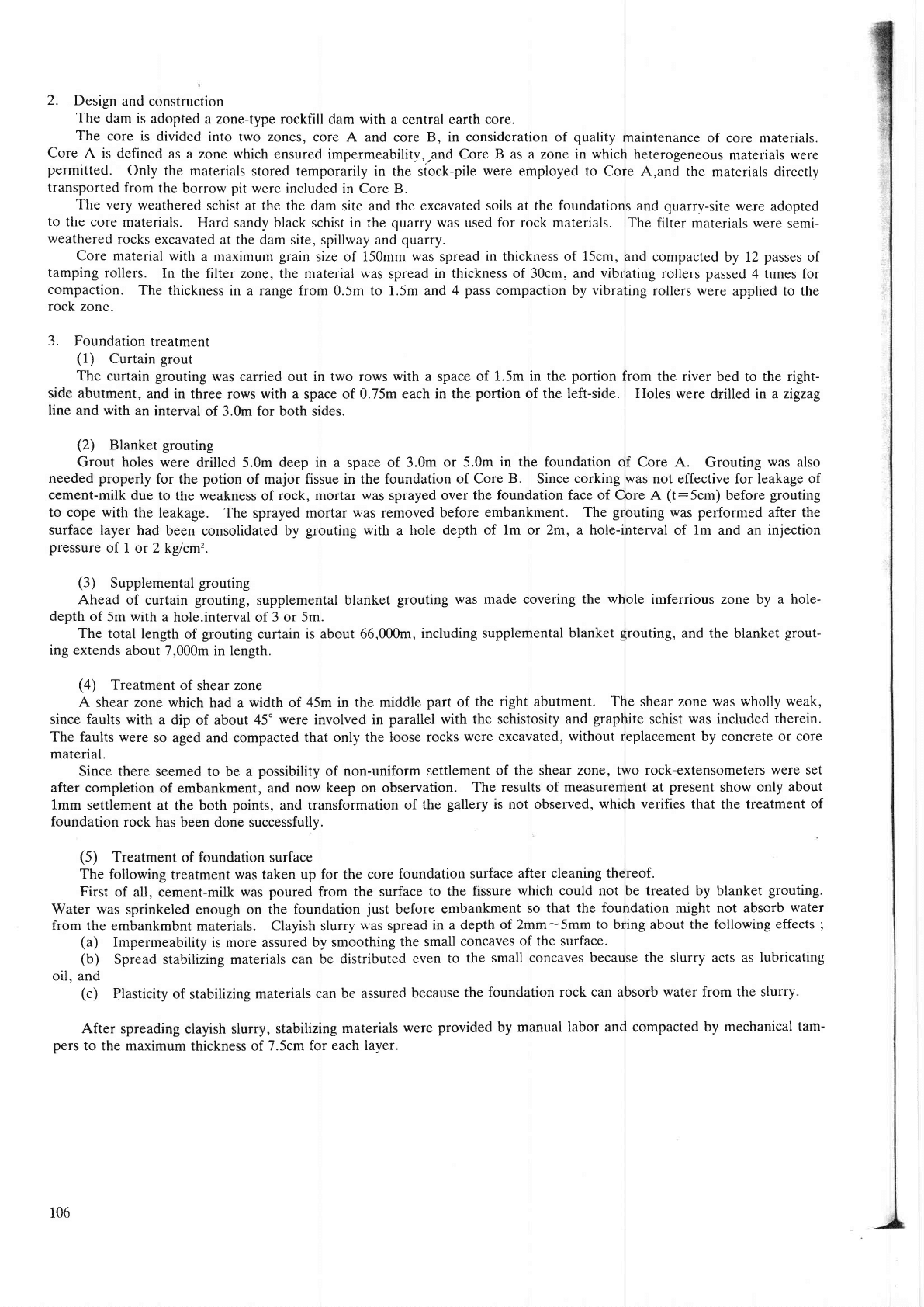
2.
Design and
construction
The dam
is adopted
a zone-type rockfill dam with
a central earth
core.
The core
is divided into
two
zones,
cor€ A and core B, in consideration of
quality
maintenance
of core materials.
Core
A is defined
as a zone which ensured imperrneability,-and Core B as a zone in which
heterogeneous
materials
were
permitted.
Only the materials
stored tempomrily in the stock-pile
were
employed to Core A,and
the mate als directly
transported
from the
borrow
pit
wer€ included in Core B.
The very weathered
schist at the the dam site and tbe excavated soils
at
the
foundations
and
quarry-site
were
adopted
to the core
materials.
Hard sandy black schist in the quarry was used for rock materials. The
filter materials were semi-
weathered
rocks
excavated
at the dam site, spillway and
quarry.
Core material
with a maximurn
grain
size of 150mm
was
spread
in thickness of 15cm, and
compacted by 12
passes
of
tamping
rollers. In
the filter zone, the mate al
was
spread in thickness
of
30cm,
and vibrating
rollers
passed
4 times for
compaction,
The thickness
in a range from 0,5m to 1.5m and
4
pass
compaction by vibrating
rollers were applied to the
rock zone.
3.
Foundationtreatment
(1)
Curtain grout
The curtain grouting
was caried out in two rows with a space of 1.5m in the
portion
from the dver bed
to
the fight-
side
abutment,
and in three
rou,s
with a
space of 0.75m
each io the
portion
of the left-side. Holes were drilled
i\
a zigz
g
line and with
an interval of 3.0m for both sides.
(2)
Blanket
grouting
Grout holes
were ddlled 5.0m deep in a space of 3.0m
or 5.0m in the foundation of Core A.
Grouting
was also
needed
properly
for
the
potion
of major
fissue in the foundation of Core
B.
Since
corking was
not effective for leakage of
cement-milk
due to the weakness of rock, mortar
was
sprayed over
the foundation face of Core A
(t:scm)
before
grouting
to cope with
the leakage.
The sprayed
mortar was removed before
embankment. The
grouting
was
pedormed
after the
surface layer had
been consolidated by
gouting with
a
hole depth of lm or 2m, a hole-interval of lm and an injection
pressure
of 1 or 2 kg/cmr.
(3)
Supplemental grouting
Ahead
of curtain
grouting,
supplemental blanket
grouting
was made covedng
the whole
imferrious zone by
a hole-
depth of
5m
with
a hole.int€rval
of
3 or 5m.
The total length
of
gouting
curtain
is about
66,000m,
including
supplemental blanket
gouting,
and the
blanket
grout-
ing extends about
7,000m in length.
(4)
Treatment
of shear zone
A shear zone which
had a
width of 45m in the middle
part
of th€ right abutment.
The
shear zone was wholly
weak,
since
faults with
a dip of about 45'were
involved in
parallel with the schistosity and
graphite
schist
was
included
therein.
The faults were
so aged and compacted that only the
loose rocks were
excavated, without replacement by conqete or core
matedal.
Since there seemed
to be a
possibility
of non-uniforrn
settlement
of the
shear
zone, two rock-extensometers were set
after completion of embankment, and now keep on observation.
The results of
measurement
at
present
show
only about
lmm settlement
at the both
points,
and transformation
of the
gallery
is not observed, which
verifies
that the treatment
of
foundation
rock has been done successfully.
(5)
Treatment
of foundation
surface
The following
treatment
was
taken
up for the core
{oundation
surface after cleaning thereof.
First of
all, cement-milk was
poured
from the sudace
to the
fissure which could not be treated by blanket
grouting.
Water was
sprinkeled
enough on
the foundation
just
before embankment
so that the
foundation
might not absorb
water
from the embankmbnt
materials. Clayisb
slurry
rvas
spread
in a depth
of 2mm-5mm to bring about the following
effects
;
(a)
Impermeability is more assured by smoothing
the small
concaves of the suface.
(b)
Spread
stabilizing mate als
can be distributed
even to
the small concaves because
the
slurry
acts as lubricating
oil, and
(c)
Plasticity
of stabilizing
materials can be assured
because
the
foundation rock can absorb
water
from the
slurry.
After spreading clayish slurry, stabilizing
materials
were
provided by manual labor and compacted by
mechanical
tam-
pers
to the maximum
thickness of
7.5cm for each layer.
106