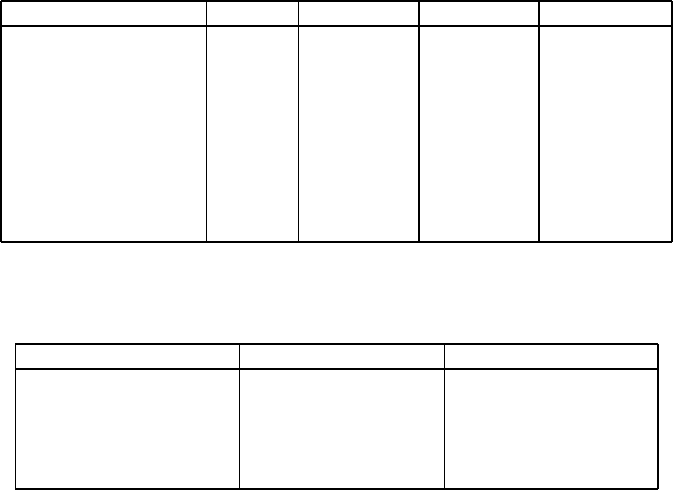
330 CHAPTER 5. PRACTICAL ASPECTS OF MAGNETIC METHODS
Table 5.2: Comparison of dierent types of dry magnetic separators, as applied
to phosphate recovery (after Roux et al. [R19]).
Parameter IMR RE Roll HGMS OGMS
Capacity Low, 4
t/h/m
Low, 8
t/h/m
High, 400
t/h
High, 60 t/h
Power input 2kW/t 0.6 kWh/t 5.6 kWh/t 0.5 kWh/t
Ore distribution Complex Complex Simple Simple
Mass [kg] per t/h of
feed
2200 440 4100 41
Sensitivity to ore
variation
High Low Low Very high
Recovery of the fines Poor Very poor Good Very poor
Table 5.3: Comparison of IMR and RE roll in ilmenite-rutile separation (after
Arvidson [A26]).
Product IMR @ 2.5 t/m/h RE roll @ 4 t/h/m
Magnetics (mass %) 25 30.5
Non-mags in mags (%) 2.5 0.46
Middlings (%) 10 0.8
Non-magnetics (%) 65 68.7
Mags in non-mags (%) 0.5 0.28
velocity to the particles, thereby counteracting, to a considerable extent, the
sweeping across of non-magnetic particles by the magnetic ones. This approach
made it possible to obtain metallurgical results comparable with those of IMR
separators, at feed rates of up to 6 t/h per meter width, or 3.5 times the optimum
feed rate of an IMR.
Comparison of dry separators for beneficiation of beach sands and
other industrial minerals.
High-intensity magnetic separation has been a standard beneficiation method
for heavy mineral sands and various industrial minerals, and a variety of dry
magnetic separators has been used. With the advent of aordable rare-earth
permanent magnets, and as a result of design improvements, the conventional
dry separators, such as induced magnetic roll and cross-belt separators are be-
ing replaced by reliable and economical rare-earth roll and drum separators
[A24, A25, A26]. Although the plant data are usually confidential, comparative
studies indicate superior performance of the rare-earth-based separators. An
example is shown in Table 5.3, which compares the separation e!ciency of IMR
and RE roll separators as applied to ilmenite and rutile separation.
A similar improvement in the e!ciency of separation after replacing the in-
duced magnetic roll with a permanent magnetic roll, was obtained with feldspar.