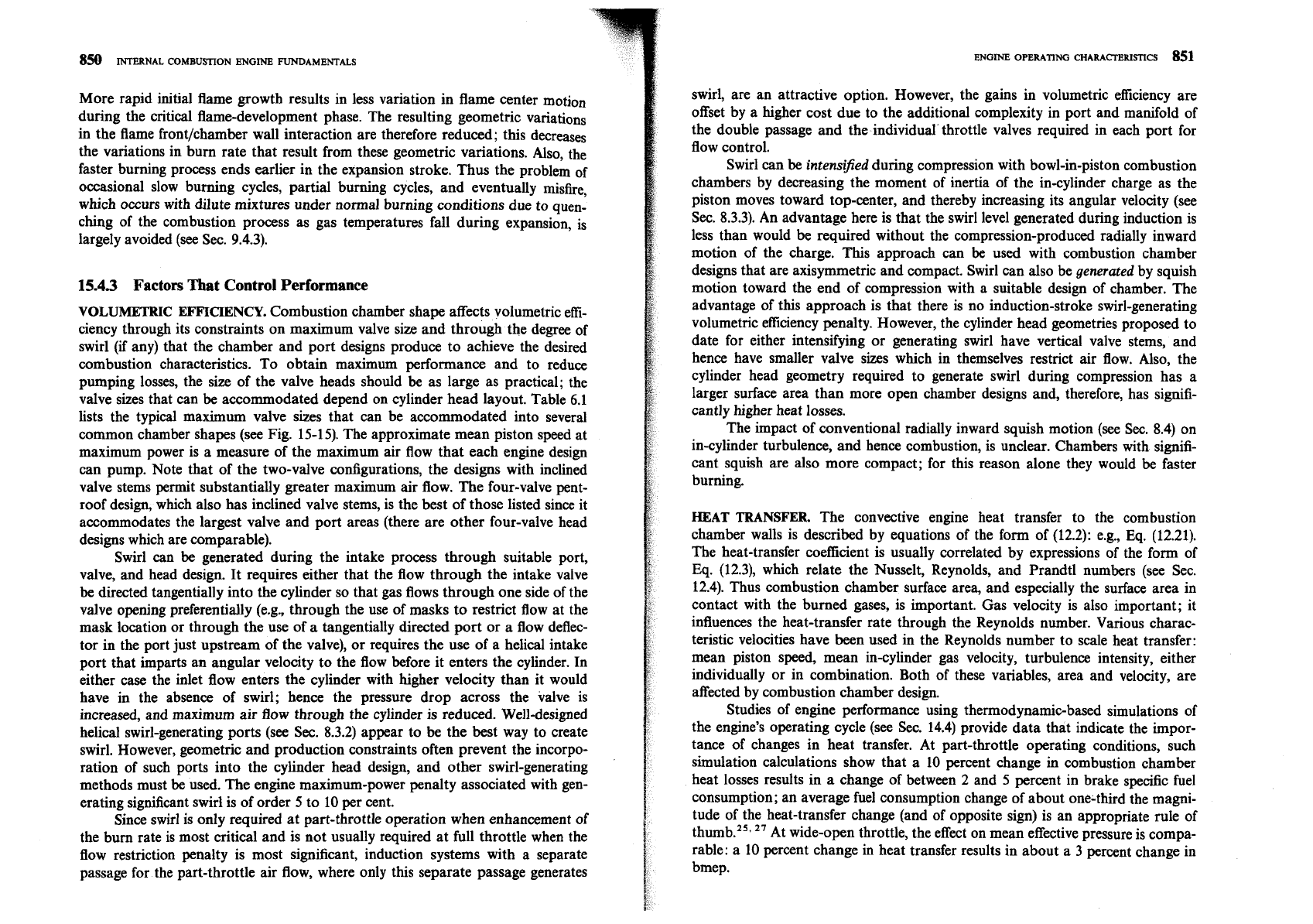
850
INTERNAL COMBUSTION
ENGINE
FUNDAMENTALS
More rapid initial flame growth results in less variation in flame center motion
during the critical flame-development phase. The resulting geometric variations
in the flame frontlchamber wall interaction are therefore reduced; this decreases
the variations in burn rate that result from these geometric variations. Also, the
faster burning process ends earlier in the expansion stroke. Thus the problem of
occasional slow burning cycles, partial burning cycles, and eventually misfire,
which occurs with dilute mixtures under normal burning conditions due to quen-
ching of the combustion process
as
gas temperatures fall during expansion, is
largely avoided (see Sec. 9.4.3).
15.43
Factors That Control Performance
VOLUMETRIC
EFFICIENCY.
Combustion chamber shape affects volumetric efi-
ciency through its constraints on maximum valve size and through the degree of
swirl
(if
any) that the chamber and port designs produce to achieve the desired
combustion characteristics. To obtain maximum performance and to reduce
pumping losses, the size of the valve heads should be as large as practical; the
valve sizes that can be accommodated depend on cylinder head layout. Table 6.1
lists the typical maximum valve sizes that can be accommodated into several
common chamber shapes (see Fig. 15-15). The approximate mean piston speed at
maximum power is a measure of the maximum air flow that each engine design
can pump. Note that of the two-valve configurations, the designs with inclined
valve stems permit substantially greater maximum air flow. The four-valve pent-
roof design, which also has inclined valve stems, is the best of those listed since it
accommodates the largest valve and port areas (there are other four-valve head
designs which are comparable).
Swirl can be generated during the intake process through suitable port,
valve, and head design. It requires either that the flow through the intake valve
be directed tangentially into the cylinder so that gas flows through one side of the
valve opening preferentially
(e.g., through the use of masks to restrict flow at the
mask location or through the use of a tangentially directed port or a flow deflec-
tor in the port just upstream of the valve), or requires the use of a helical intake
port that imparts an angular velocity to the flow before it enters the cylinder. In
either case the inlet flow enters the cylinder with higher velocity than it would
have in the absence of swirl; hence the pressure drop across the valve is
increased, and maximum air flow through the cyiinder is reduced. Well-designed
helical swirl-generating ports (see
Sec. 8.3.2) appear to be the best way to create
swirl. However, geometric and production constraints often prevent the incorpo-
ration of such ports into the cylinder head design, and other swirl-generating
methods must be used. The engine maximum-power penalty associated with gen-
erating significant swirl is of order 5 to 10 per cent.
Since swirl is only required at part-throttle operation when enhancement of
the burn rate is most critical and is not usually required at full throttle when the
flow restriction penalty is most significant, induction systems with a separate
passage for the part-throttle air flow, where only this separate passage generates
swirl, are an attractive option. However, the gains in volumetric efficiency are
offset by a higher cost due to the additional complexity in port and manifold of
the double passage and the individual throttle valves required in each port for
flow control.
Swirl can be
intensijed
during compression with bowl-in-piston combustion
chambers by decreasing the moment of inertia of the in-cylinder charge as the
piston moves toward top-center, and thereby increasing its angular velocity (see
Sec. 8.3.3). An advantage here is that the swirl level generated during induction is
less than would be required without the compression-produced radially inward
motion of the charge. This approach can be used with combustion chamber
designs that are axisymrnetric and compact. Swirl can also
be
generated
by squish
motion toward the end of compression with a suitable design of chamber. The
advantage of this approach is that there is no induction-stroke swirl-generating
volumetric efficiency penalty. However, the cylinder head geometries proposed to
date for either intensifying or generating swirl have vertical valve stems, and
hence have smaller valve sizes which in themselves restrict air flow. Also, the
cylinder head geometry required to generate swirl during compression has a
larger surface area than more open chamber designs and, therefore, has signifi-
cantly higher heat losses.
The impact of conventional radially inward squish motion (see
Sec. 8.4) on
in-cylinder turbulence, and hence combustion, is unclear. Chambers with signifi-
cant squish are also more compact; for this reason alone they would
be
faster
burning.
HEAT
TRANSFER.
The convective engine heat transfer to the combustion
chamber walls is described by equations of the form of (12.2): e.g., Eq. (12.21).
The heat-transfer coefficient is usually correlated by expressions of the form of
Eq.
(12.3), which relate the Nusselt, Reynolds, and Prandtl numbers (see Sec.
12.4). Thus combustion chamber surface area, and especially the surface area in
contact with the burned gases, is important. Gas velocity is also important; it
influences the heat-transfer rate through the Reynolds number. Various charac-
teristic velocities have been used in the Reynolds number to scale heat transfer:
mean piston speed, mean in-cylinder gas velocity, turbulence intensity, either
individually or in combination. Both of these variables, area and velocity, are
affected by combustion chamber design.
Studies of engine performance using thermodynamic-based simulations of
the engine's operating cycle (see Sec. 14.4) provide data that indicate the impor-
tance of changes in heat transfer. At part-throttle operating conditions, such
simulation calculations show that a 10 percent change in combustion chamber
heat losses results in a change of between 2 and
5
percent in brake specific fuel
consumption; an average fuel consumption change of about one-third the magni-
tude of the heat-transfer change (and of opposite sign) is an appropriate rule of
thumb.25*
"
At wide-open throttle, the effect on mean effective pressure is compa-
rable: a 10 percent change in heat transfer results in about a 3 percent change in
bmep.