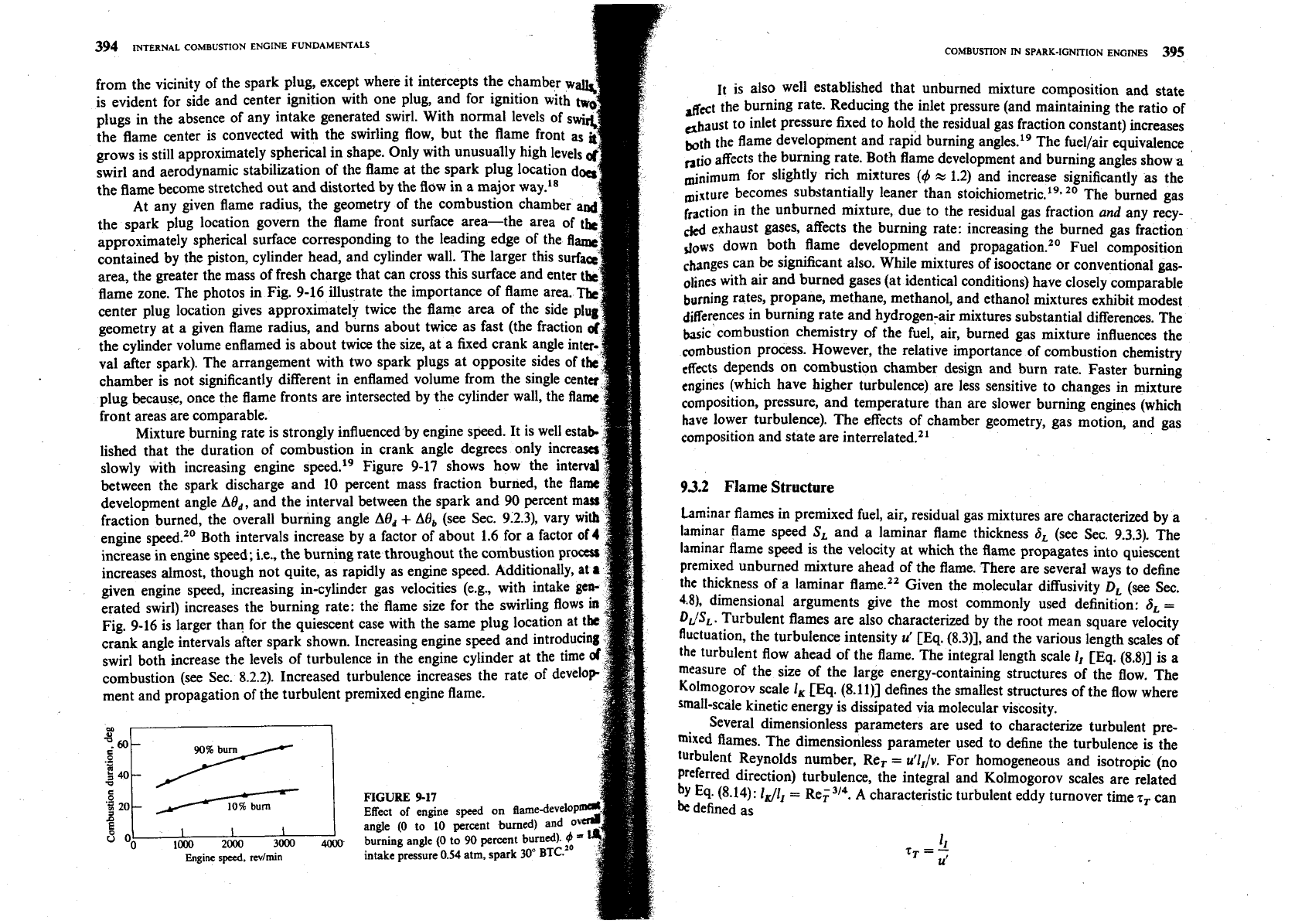
394
INTERNAL COMBUSTION ENGINE FUNDAMENTALS
from the vicinity of the spark plug, except where it intercepts the chamber
w
is evident for side and center ignition with one plug, and for ignition with
plugs in the absence of any intake generated swirl. With normal levels of s
the flame center is convected with the swirling flow, but the flame front
grows is still approximately spherical in shape. Only with unusually hi
swirl and aerodynamic stabilization of the flame at the spark plug location
d
the flame become stretched out and distorted by the flow in a major way.18
At any given flame radius, the geometry of the combustion chamber
ad
the spark plug location govern the flame front surface area-the area of
tk
approximately spherical surface corresponding to the leading edge of the
flw
contained by the piston, cylinder head, and cylinder wall. The larger this surf==
area, the greater the mass of fresh charge that can cross this surface and enter
flame zone. The photos in Fig. 9-16 illustrate the importance of flame area.
~h~
center plug location gives approximately twice the flame area of the side plu
geometry at a given flame radius, and burns about twice as fast (the fraction
the cylinder volume enflamed is about twice the size, at a fixed crank angle int
val after spark). The arrangement with two spark plugs at opposite sides oft
chamber is not significantly different in enflamed volume from the single ce
plug because, once the flame fronts are intersected by the cylinder wall, the
fl
front areas are comparable.
Mixture burning rate is strongly influenced by engine speed. It is well esta
lished that the duration of combustion in crank angle degrees only incre
slowly with increasing engine speed.19 Figure 9-17 shows how the in
between the spark discharge and 10 percent mass fraction burned, the
development angle
Ad,,
and the interval between the spark and 90 percent
mass
fraction burned, the overall burning angle
Ad,
+
Ad,
(see Sec. 9.2.3
engine speed." Both intervals increase by a factor of about 1.6 for a
increase in engine speed; i.e., the burning rate throughout the combustion pr
increases almost, though not quite, as rapidly as engine speed. Additionally,
at
given engine speed, increasing in-cylinder gas velocities (e.g., with intake ge
erated swirl) increases the burning rate: the flame size for the swirling flows
Fig. 9-16 is larger than for the quiescent case with the same plug location at t
crank angle intervals after spark shown. Increasing engine speed and introducing
swirl both increase the levels of turbulence in the engine cylinder at the time
combustion (see Sec. 8.2.2). Increased turbulence increases the rate of develo
ment and propagation of the turbulent premixed engine flame.
FIGURE
9-17
n
Effect of engine speed on flame-deve
angle
(0
to
10
percent burned) and
2&3
3&
4000
burning angle
(0
to
90
percent burn&
Engine
speed,
revlmn
intake pressure
0.54
atm, spark
30"
BTC.
COMBUSTION lN SPARK-IGNITION ENGlNES
395
11
is also well established that unburned mixture composition and state
the burning rate. Reducing the inlet pressure (and maintaining the ratio of
daust
to inlet pressure fixed to hold the residual gas fraction constant) increases
both the flame development and rapid burning angles.'' The fuellair equivalence
,,tio the burning rate. Both flame development and burning angles show
a
minimum for slightly rich mixtures
(4
x
1.2) and increase significantly as the
becomes substantially leaner than stoi~hiometric.'~~
20
The burned gas
friction
in the unburned mixture, due to the residual gas fraction
and
any recy-
gases, affects the burning rate: increasing the burned gas fraction
dews
down both flame development and pr~pagation.'~ Fuel composition
~bnges can be significant also. While mixtures of isooctane or conventional gas-
oline~ with air and burned gases (at identical conditions) have closely comparable
burning rates, propane, methane, methanol, and ethanol mixtures exhibit modest
diKerences in burning rate and hydrogen-air mixtures substantial differences. The
bjsic combustion chemistry of the fuel, air, burned gas mixture influences the
combustion process. However, the relative importance of combustion chemistry
effects depends on combustion chamber design and burn rate. Faster burning
engines (which have higher turbulence) are less sensitive to changes in mixture
composition, pressure, and temperature than are slower burning engines (which
have lower turbulence). The effects of chamber geometry, gas motion, and gas
composition and state are
interrelated.21
93.2
Flame Structure
Laminar flames in premixed fuel, air, residual gas mixtures are characterized by a
laminar flame speed
SL
and a laminar flame thickness
6,
(see
Sec.
9.3.3). The
laminar flame speed is the velocity at which the flame propagates into quiescent
premixed unburned mixture ahead of the flame. There are several ways to define
the thickness of a laminar flame." Given the molecular diffusivity
DL
(see Sec.
4.8),
dimensional arguments give the most commonly used definition:
6,
=
D
JSL.
Turbulent flames are also characterized by the root mean square velocity
fluctuation, the turbulence intensity
u'
[Eq. (8.3)], and the various length scales of
the
turbulent flow ahead of the flame. The integral length scale 1, [Eq. (841 is a
measure of the size of the large energy-containing structures of the flow. The
Kolmogorov scale 1, [Eq. (8.11)] defines the smallest structures of the flow where
small-scale kinetic energy is dissipated via molecular viscosity.
Several dimensionless parameters are used to characterize turbulent pre-
mixed flames. The dimensionless parameter used to define the turbulence is the
turbulent Reynolds number, Re,
=
ullI/v.
For homogeneous and isotropic (no
Preferred direction) turbulence, the integral and Kolmogorov scales are related
by
Eq. (8.14):
I&
=
Re;". A characteristic turbulent eddy turnover time
7,
can
be
defined as