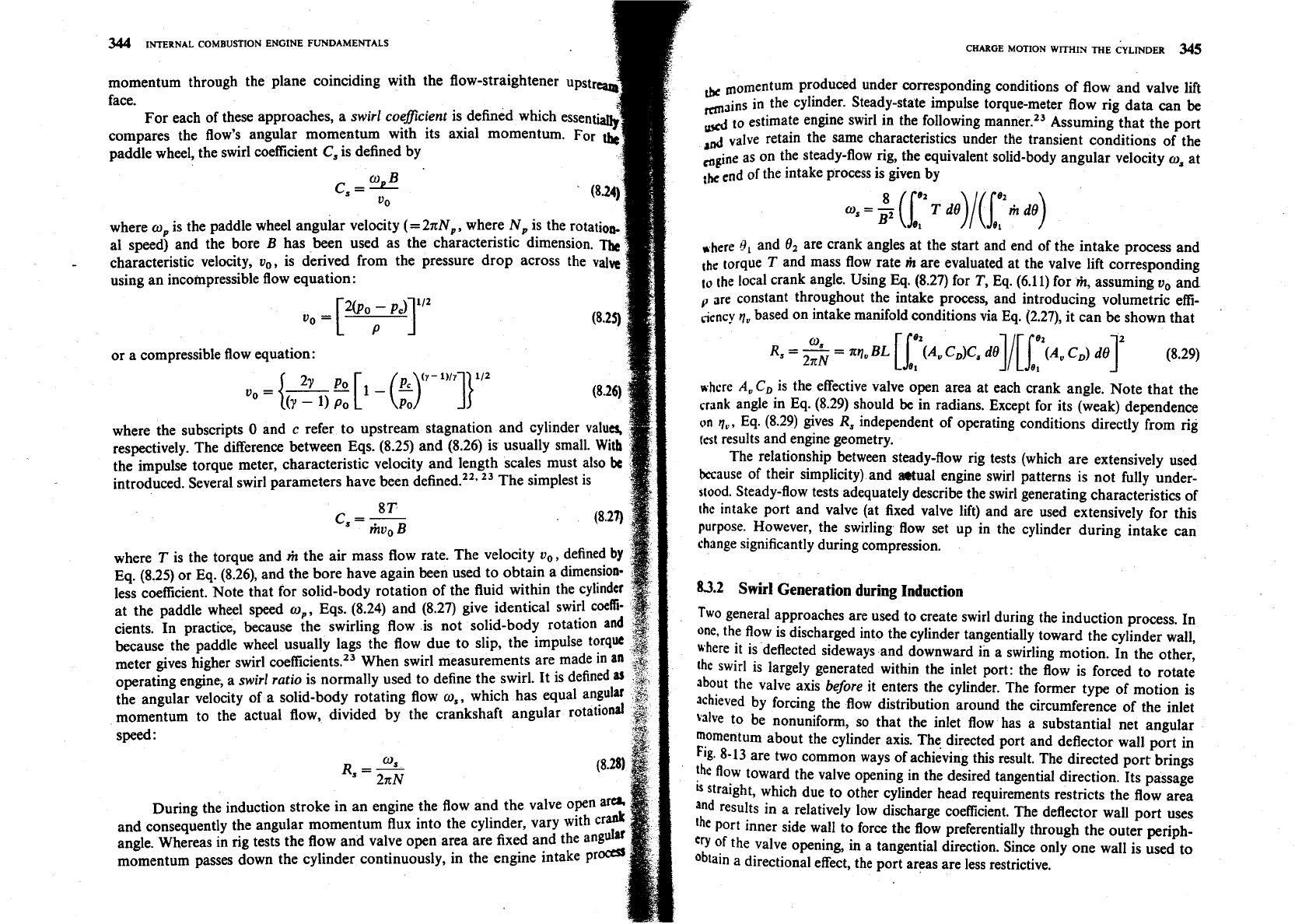
344
INTERNAL
COMBUSTION ENGINE FUNDAMENTALS
momentum through the plane coinciding with the flow-straightener upstr
face.
For each of these approaches, a
swirl coeflcient
is defined which essent
compares the flow's angular momentum with its axial momentum. For
paddle wheel, the swirl coefficient
C,
is defined by
o
B
C,
=
-
00
where w, is the paddle wheel angular velocity (=2nNp, where N, is the rotatio
a1 speed) and the bore
B
has been used as the characteristic dimension.
-
characteristic velocity,
vO,
is derived from the pressure drop across the
v
using an incompressible flow equation:
uO
=
poi
pPljI2
or a compressible flow equation:
{
27 Po
-
(PC$-
1)ty]}112
vo=
--
(Y
-
1) Po
where the subscripts
0
and
c
refer to upstream stagnation and cylinder values,
respectively. The difference between Eqs. (8.25) and (8.26) is usually small.
With
the impulse torque meter, characteristic velocity and length scales must also
k
introduced. Several swirl parameters have been defined.22.
23
The simplest is
8
T
C,
=
-
rhvo
B
where
T
is the torque and
m
the air mass flow rate. The velocity oO, defined
by
Eq. (8.25) or Eq. (8.26), and the bore have again been used to obtain a dimension-
less coefficient. Note that for solid-body rotation of the fluid within the cylinder
at the paddle wheel speed
o,,
Eqs. (8.24) and (8.27) give identical swirl coeffi-
cients. In practice, because the swirling flow is not solid-body rotation and
because the paddle wheel usually lags the flow due to slip, the impulse torqw
meter gives higher swirl
coefficient^.^^
When swirl measurements are made
in
an
operating engine, a
swirl ratio
is normally used to define the swirl. It is defined
the angular velocity of a solid-body rotating flow os, which has equal angular
momentum to the actual flow, divided by the crankshaft angular rotational
speed
:
W,
R,
=
-
2nN
During the induction stroke in an engine the flow and the valve open am
and consequently the angular momentum flux into the cylinder, vary with
angle. Whereas in rig tests the flow and valve open area are
fixed and the andu
momentum passes down the cylinder continuously, in the engine intake pre
Ibe
produced under corresponding conditions of flow and valve lift
mains in the cylinder. Steady-state impulse torque-meter flow rig data can
be
to
estimate engine swirl in the following manner.23 Assuming that the port
valve retain the same characteristics under the transient conditions of the
mgine as on the steady-flow rig, the equivalent solid-body angular velocity
o,
at
:he
end of the intake process is given by
*here
Q1
and
6,
are crank angles at the start and end of the intake process and
,hc
torque
T
and mass flow rate
m
are evaluated at the valve lift corresponding
,,
[he local crank angle. Using Eq. (8.27) for
T,
Eq. (6.1 1) for
m,
assuming
vo
and
,,
are constant throughout the intake process, and introducing volumetric effi-
,jfncy
q,
based on intake manifold conditions via Eq. (2.27), it can be shown that
where
A,CD
is the effective valve open area at each crank angle. Note that the
crank angle in Eq. (8.29) should
be
in radians. Except for its (weak) dependence
on
q,,
Eq. (8.29) gives
R,
independent of operating conditions directly from rig
(61
results and engine geometry.
The relationship between steady-flow rig tests (which are extensively used
because of their simplicity) and Wual engine swirl patterns is not fully under-
stood. Steady-flow tests adequately describe the swirl generating characteristics of
thc intake port and valve (at fixed valve lift) and are used extensively for this
purpose. However, the swirling flow set up in the cylinder during intake can
change significantly during compression.
83.2
Swirl Generation during Induction
Two general approaches are used to create swirl during the induction process. In
one, the flow is discharged into the cylinder tangentially toward the cylinder wall,
ahere it is deflected sideways and downward in a swirling motion. In the other,
the
swirl is largely generated within the inlet port: the flow is forced to rotate
about the valve axis
before
it enters the cylinder. The former type of motion is
achieved by forcing the flow distribution around the circumference of the inlet
valve to be nonuniform, so that the inlet flow has a substantial net angular
momentum about the cylinder axis. The directed port and deflector wall port in
Fig. 8-13 are two common ways of achieving this result. The directed port brings
the flow toward the valve opening in the desired tangential direction. Its passage
"
straight, which due to other cylinder head requirements restricts the flow area
and results in a relatively low discharge coefficient. The deflector wall port uses
'he pon inner side wall to fom the flow preferentially through the outer periph-
t'Y
of the valve opening, in a tangential direction. Since only one wall is used to
Obtain a directional effect, the port areas are less restrictive.