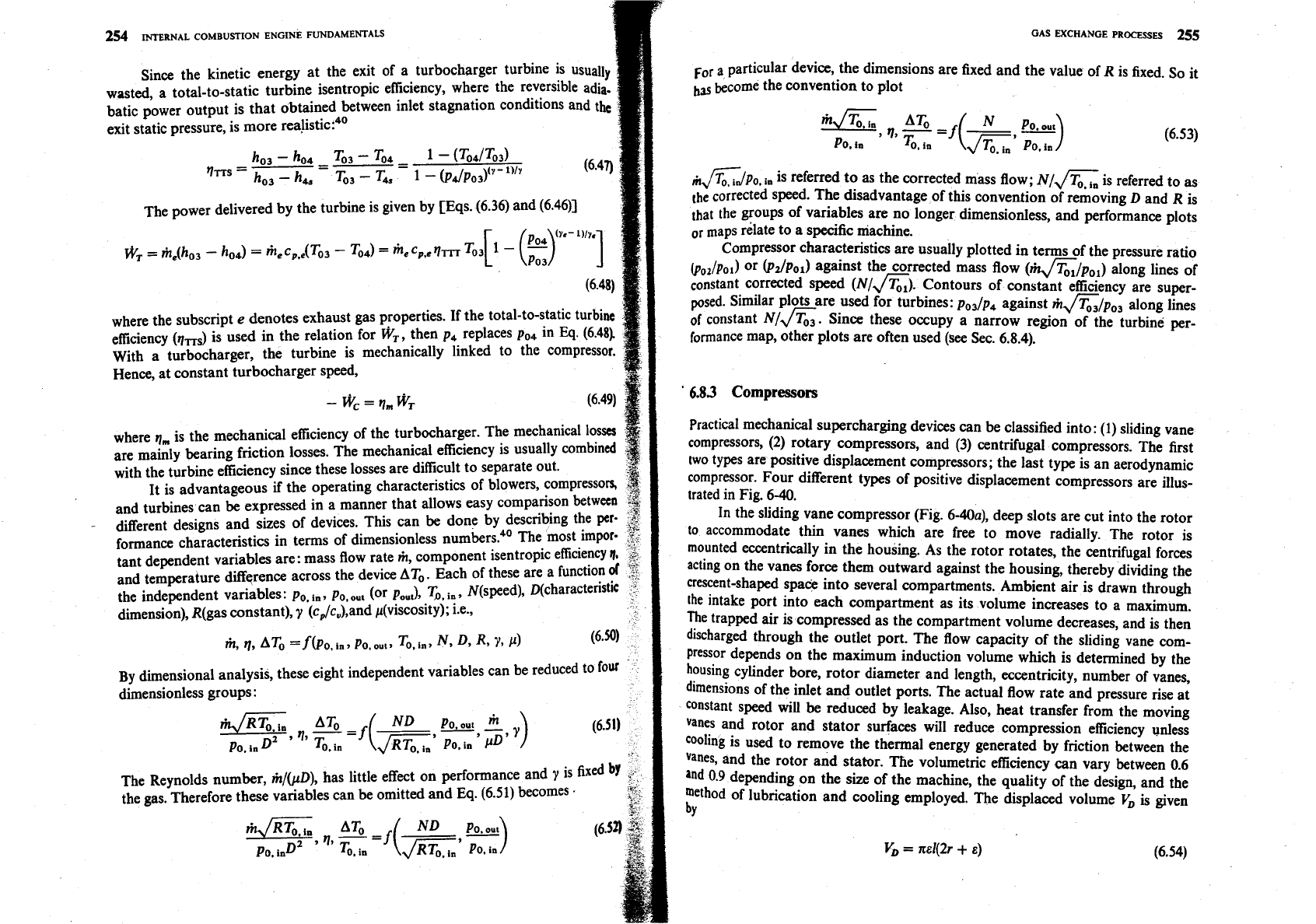
The power delivered by the turbine is given by [Eqs. (6.36) and (6.4611
I
where the subscript
e
denotes exhaust gas properties. If the total-to-static turbine
efficiency (qns) is used in the relation for wT, then p4 replaces po4 in
Eq.
(6.48).
With a turbocharger, the turbine is mechanically linked to the compressor.
Hence, at constant turbocharger speed,
where q, is the mechanical efficiency of the turbocharger. The mechanical losses
are mainly bearing friction losses. The mechanical effciency is usually combined
with the turbine efficiency since these losses are difficult to separate out.
It is advantageous
if
the operating characteristics of blowers, compressors,
and turbines can be expressed in a manner that allows easy comparison between
-
different designs and sizes of devices. This can be done by describing the per-
formance characteristics in terms of dimensionless numbers?' The most impor-
tant dependent variables are: mass flow rate m, component isentropic efficiency
q.
and temperature diffqrence across the device ATo. Each of these are a function
d
the independent variables
:
po.
in
,
po,
out
(or pout),
T,,
in
,
N(speed), ~(characteisf~
dimension), R(gas constant),
y
(cJc,),and p(viscosity); i.e.,
254
MTERNAL
COMBUSTION
ENGINE
FUNDAMENTALS
Since the kinetic energy at the exit of a turbocharger turbine is usually
wasted, a total-to-static turbine isentropic effciency, where the reversible
batic power output is that obtained between inlet stagnation conditions and the
exit static pressure, is more realistic:40
h03
-
h04
-
T03
-
T04
-
-
(To~/To~)
Vns
=
-
-
ho3
-
h,
To,
-
Tk
1
-
@4/pO3)"
-
''IY
By dimensional analysis, these eight independent variables can be reduced to four
dimensionless groups
:
ND Po.out (6.51)
PO.
in
RT,,
,
PO,
in
'
PD
'
The Reynolds number, rh/(pD), has little effect on performance and
y
is fixed
by
$1
the gas. Therefore these variables can be omitted and Eq. (6.51) becomes.
P'
t
ND
PO.
inDZ
TO,
in
RTo,
in
PO.
in
For
a particular device, the dimensions are fixed and the value of R is fixed.
SO
it
bas
become the convention to plot
h&~po,
in
is referred to as the corrected mass flow;
N/&
is referred to as
the corrected speed. The disadvantage of this convention of removing D and R is
that the groups of variables are no longer dimensionless, and performance plots
or
maps relate to a specific machine.
Compressor characteristics are usually plotted in terms of the pressure ratio
@02/p01) or (PJPOI) against the corrected mass flow (lit&/po,) along lines of
~~nstant corrected sped
(N/&).
Contours of constant effciency are super-
posed. Similar plots are used for turbines: po3/p4 against lit&/po3 along lines
of constant
N/&.
Since these occupy a narrow region of the turbine per-
formance map, other plots are often used
(see
Sec. 6.8.4).
*
6.83
Compressors
practical mechanical supercharging devices can be classified into:
(1)
sliding vane
compressors, (2) rotary compressors, and (3) centrifugal compressors. The first
two types are positive displacement compressors; the last type is an aerodynamic
compressor. Four different types of positive displacement compressors are illus-
trated in Fig. 6-40.
In the sliding vane compressor (Fig. 6-40a), deep slots are cut into the rotor
to accommodate thin vanes which are free to move radially. The rotor is
mounted eccentrically in the housing. As the rotor rotates, the centrifugal forces
acting on the vanes force them outward against the housing, thereby dividing the
crescent-shaped space into several compartments. Ambient air is drawn through
the intake port into each compartment as its volume increases to a maximum.
The trapped air is compressed as the compartment volume decreases, and
is
then
discharged through the outlet port. The flow capacity of the sliding vane com-
pressor depends on the maximum induction volume which is determined by the
housing cylinder bore, rotor diameter and length, eccentricity, number of vanes,
dimensions of the inlet and outlet ports. The actual flow rate and pressure rise at
constant speed
will
be reduced by leakage. Also, heat transfer from the moving
vanes and rotor and stator surfaces will reduce compression efficiency unless
cooling is used to remove the thermal energy generated by friction between the
vanes, and the rotor and stator. l3e volumetric efficiency can vary between 0.6
and
0.9
depending on the size of the machine, the quality of the design, and the
method of lubrication and cooling employed. The displaced volume
V,
is given
by