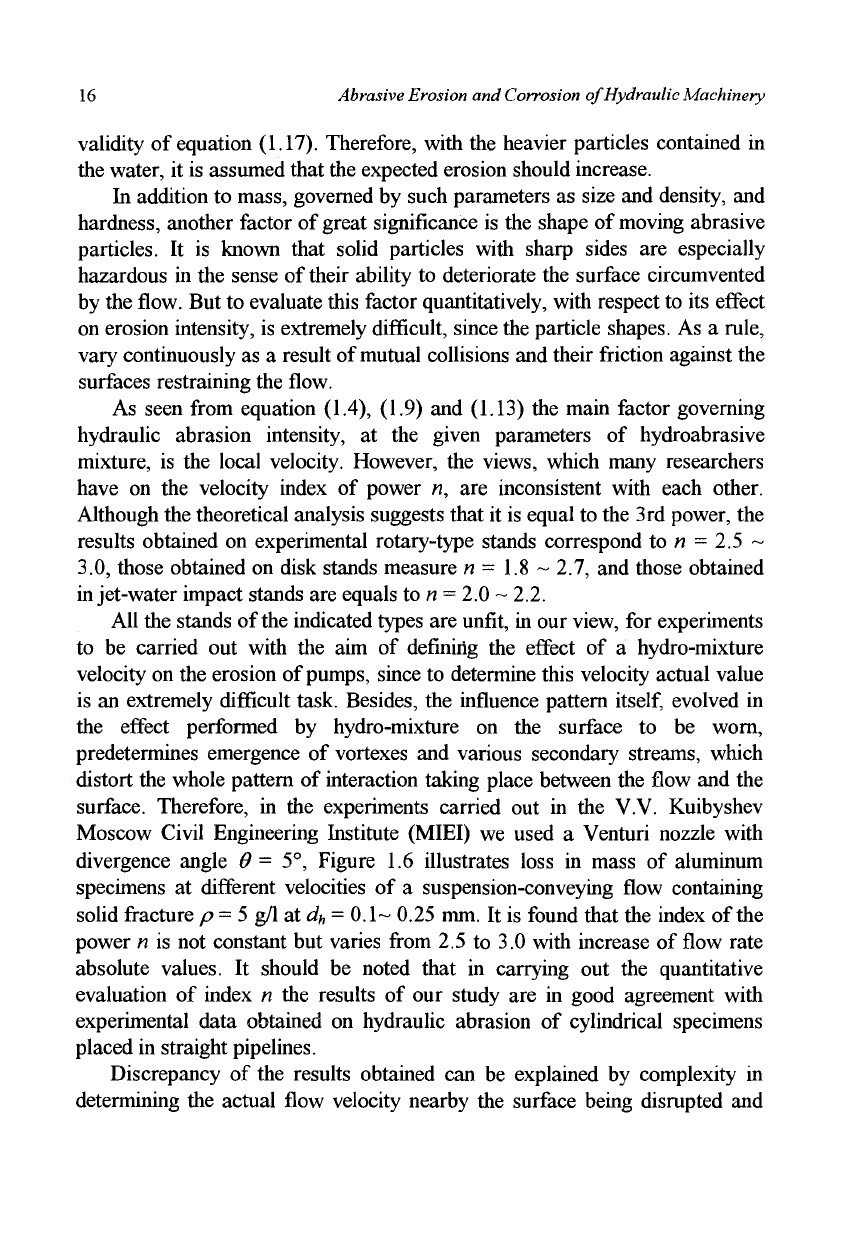
16
Abrasive Erosion and Corrosion of Hydraulic Machinery
validity of equation (1.17). Therefore, with the heavier particles contained in
the water, it is assumed that the expected erosion should increase.
In addition to mass, governed by such parameters as size and density, and
hardness, another factor of great significance is the shape of moving abrasive
particles. It is known that solid particles with sharp sides are especially
hazardous in the sense of their ability to deteriorate the surface circumvented
by the flow. But to evaluate this factor quantitatively, with respect to its effect
on erosion intensity, is extremely difficult, since the particle shapes. As a rule,
vary continuously as a result of mutual collisions and their friction against the
surfaces restraining the flow.
As seen from equation (1.4), (1.9) and (1.13) the main factor governing
hydraulic abrasion intensity, at the given parameters of hydroabrasive
mixture, is the local velocity. However, the views, which many researchers
have on the velocity index of power n, are inconsistent with each other.
Although the theoretical analysis suggests that it is equal to the 3rd power, the
results obtained on experimental rotary-type stands correspond to n = 2.5 ~
3.0, those obtained on disk stands measure n = 1.8 ~ 2.7, and those obtained
in
jet-water impact stands are equals to n
=
2.0 ~ 2.2.
All the stands of the indicated types are unfit, in our view, for experiments
to be carried out with the aim of defining the effect of a hydro-mixture
velocity on the erosion of
pumps,
since to determine this velocity actual value
is an extremely difficult task. Besides, the influence pattern
itself,
evolved in
the effect performed by hydro-mixture on the surface to be worn,
predetermines emergence of vortexes and various secondary streams, which
distort the whole pattern of interaction taking place between the flow and the
surface. Therefore, in the experiments carried out in the V.V. Kuibyshev
Moscow Civil Engineering Institute (MIEI) we used a Venturi nozzle with
divergence angle 6 = 5°, Figure 1.6 illustrates loss in mass of aluminum
specimens at different velocities of a suspension-conveying flow containing
solid fracture p = 5 g/1 at d
h
= 0.1~ 0.25 mm. It is found that the index of the
power n is not constant but varies from 2.5 to 3.0 with increase of flow rate
absolute values. It should be noted that in carrying out the quantitative
evaluation of index n the results of our study are in good agreement with
experimental data obtained on hydraulic abrasion of cylindrical specimens
placed in straight pipelines.
Discrepancy of the results obtained can be explained by complexity in
determining the actual flow velocity nearby the surface being disrupted and