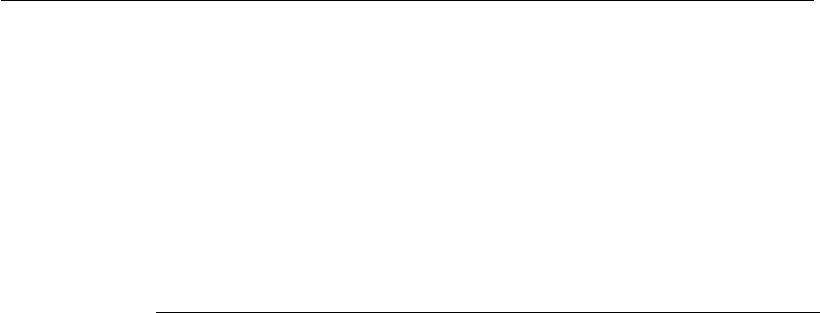
be dispensed with for release of the bulk product (WHO, 1998). Other
potential contaminants that should be monitored are endotoxins, animal
sera-derived proteins or protein fragments, and degradation products or
other contaminants derived from the purification process, such as resin
ligands, detergents, or salts. The purification steps should be designed to
effectively remove those contaminants and the assays for their quantifica-
tion should be validated (ICH, 1996a).
14.8 Stability
Stability is defined as the period of time during which the product
maintains, within the specified limits, the same characteristics and proper-
ties displayed when it was manufactured. Environmental factors like tem-
perature, air, light, ionic content, and humidity can affect the drug’s
quality (Ugwu and Apte, 2004). Proteins are susceptible to proteolysis,
denaturation, aggregation, fragmentation, and chemical modifications such
as oxidation and changes in the disulfide bonds. The degradation process
directly affects the biological activity of the product and might cause
immunogenicity, among other adverse effects. The shelf-life is determined
by stability tests that guarantee that the product is active, pure, and safe
during a specified period, if stored under the prescribed conditions. The
stability tests should establish identity, purity, potency, and modifications
of the product. Tests to demonstrate stability include: (i) potency of
biological activity in vivo or in vitro, compared to reference material; (ii)
purity and molecular characterization of the active component and degra-
dation products, by SDS-PAGE, capillary electrophoresis, immunoelec-
trophoresis, western blotting, isoelectric focusing, chromatography
(reverse phase, ion exchange, hydrophobic interaction, or affinity), peptide
mapping, circular dichroism, or mass spectrometry; (iii) physical charac-
teristics and appearance (color, opacity, pH, visible particulates in the
solution or after reconstitution of the lyophilized material); (iv) sterility
testing or alternatively package integrity testing; (v) assays to quantify
additives, stabilizers, preservatives, or excipients.
For registration, the stability tests supporting the proposed shelf-life
must be performed in three consecutive product batches in their final
package. The data obtained on a pilot scale are accepted for registration
with a commitment by the manufacturer, after approval, to submit the first
three batches of the commercial-scale production for stability testing. The
shelf-life of biological products determines the frequency at which the
tests should be repeated. For a product with a shelf-life longer than 1 year,
the tests should be repeated every 3 months for the first year, every 6
months for the second year, and annually after that. The stability should
be monitored after the beginning of commercialization with enough
batches and a frequency to allow a tendency analysis (ICH, 1996b; EC,
2004). Accelerated tests (Tydeman and Kirkwood, 1984), with samples
stored at temperatures above the specifications, can help in the identifica-
tion of degradation products and evaluate the capacity of analytical tools
used in the stability testing.
362 Animal Cell Technology