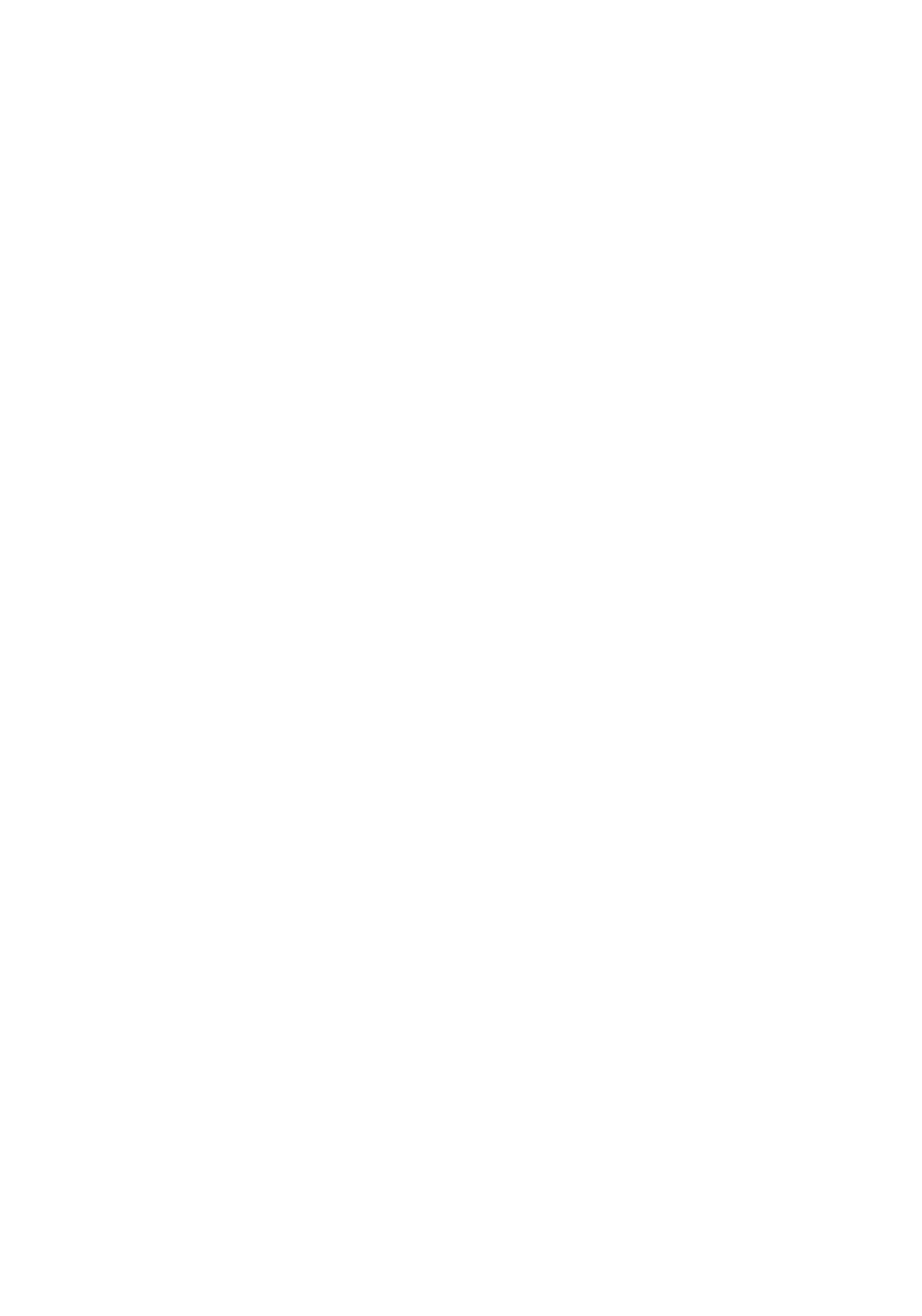
EN 13480-4:2002(E)
Issue 1 (2002-05)
10.2.2 Adjustments by means of heat
Heat straightening by local heating shall be performed under strict supervision.
For materials other than group 1 materials, the use of this method shall be allowed only in so far as it can be
demonstrated that the procedure does not adversely modify the characteristics of the metal.
NOTE A test can be conducted to check the absence of notable alteration in the heated area (e.g. dye penetrant, hardness
test).
10.2.3 Adjustment by welding
Adjustment by welding, with or without filler metal may be used on welded joints. Details such as parameters of the
welding procedure (capping pass) shall be specified.
10.2.4 Adjustment by local forging
Local forging shall only be performed by uniform circumferential heating of the part to be adjusted. During the local
forging operation, the temperature and the rate of heating and cooling shall be carried out in accordance with a
written procedure.
The requirements of 7.3 shall apply to local forging.
NOTE The material characteristics should be taken into account before forging.
10.3 Weld repair
Welding defects which require repair shall be removed by grinding, chipping, gouging, flame, plasma or machining
part or all of the weld. When using thermal processes, the pipe and weld material shall not be adversely affected.
Weld repairs shall be made using approved procedures and approved welding personal. Prior to repair welding, the
surface of all joints shall be examined by NDT to ensure freedom from cracks and other defects.
A weld defect shall not be repaired more than twice with the same procedure. Any further repair shall be done in
accordance with an approved, modified and documented procedure.
If a weld is repaired as a result of radiographic examination, the films showing the defects shall be made available.
The original assessment that led to the repair shall appear in the documentation. All weld repairs shall be
documented
All repaired welds shall be non-destructively tested in accordance with EN 13480-5.
11 Marking and documentation
11.1 Marking of spools and components for installation
All spools and components shall be marked for identification. The markings shall be by means of paint, stamping,
or tags. For materials working in the creep range or under cyclic load, only low-stress stamps shall be used.
This marking shall remain visible throughout the installation process.
Licensed Copy: London South Bank University, London South Bank University, Wed Jul 12 21:19:14 BST 2006, Uncontrolled Copy, (c) BSI