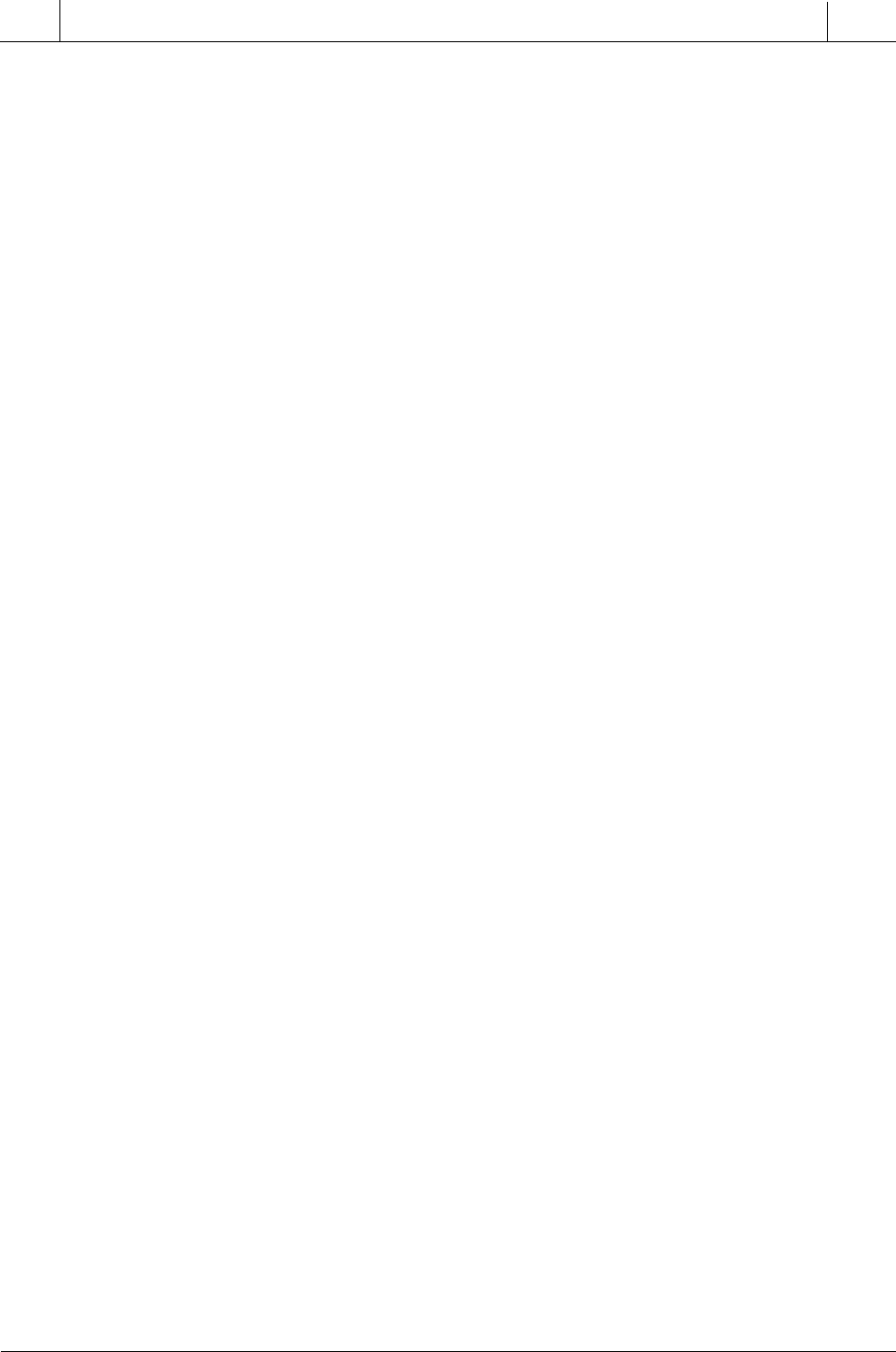
767
CHAPTER
15
Process Controllers
and Loop Tuning
SECTION
4
PLC Process
Applications
Industrial Text & Video Company 1-800-752-8398
www.industrialtext.com
Integral action tends to ignore high-frequency changes, such as noise or
rapid transients, in the process. Although this control mode eliminates the
inherent offset error present in a proportional controller, it adversely affects
stability. If the integration time is reduced, the response during the slow
period of the process will become faster, inducing cycling.
Derivative control provides corrective action as a function of either the rate
of change of the error or the process variable. A derivative controller provides
its highest gain, or corrective action, at high frequencies. Hence, it provides
an anticipatory response to the process variable change. The derivative mode
cannot be used alone and does not eliminate residual error.
A proportional-integral, or PI, controller combines the fast response of
proportional action with the offset error elimination of integral action. A PI
controller with an integral time that is too long will exhibit a response that
will take a long time to return to the set point. Conversely, a shorter integral
time will cause the process variable to cross the set point faster, resulting in
damped oscillations. An integral time that is too short, however, will produce
continuous oscillations.
A proportional-derivative, or PD, controller provides better response stabil-
ity than a PI controller, but it does not provide offset error elimination. A
PD controller is useful in applications where the process has a long lag time
delay in its recovery from a disturbance. The derivative action in this
controller provides a lead function, which cancels some of the process lag
and allows the proportional band to become narrower. This improves re-
sponse and stability. A PD controller does not eliminate offset error, but a
narrower proportional band can reduce the amount of residual error in the
system. A derivative time constant (K
D
or T
D
) that is too long will cause the
process variable to change too rapidly and overshoot the set point with
damped oscillation. Conversely, if the derivative constant is too short, the
process variable will take too long to reach the set point.
A proportional-integral-derivative, PID, controller combines the increased
stability of a PD controller with the eliminated offset feature of a PI
controller. A PID controller can be used to control almost any type of process,
including those with long lag times. The gains for each of the control actions
in a PID controller can be derived experimentally utilizing several tuning
methods.
An integral, or reset, windup situation occurs when an integral action
saturates a controller’s output at 100%. Integral windup usually happens
during the start-up of a process. This condition occurs when the error in a
slow-responding process system is large. The proportional action tries to bring
the process variable closer to the set point, but the slow speed of the process
response and the presence of error induces the integral action to continue,
keeping the controller at 100% output. This condition can be prevented by
disabling the integral action once the controller’s output reaches 100%.