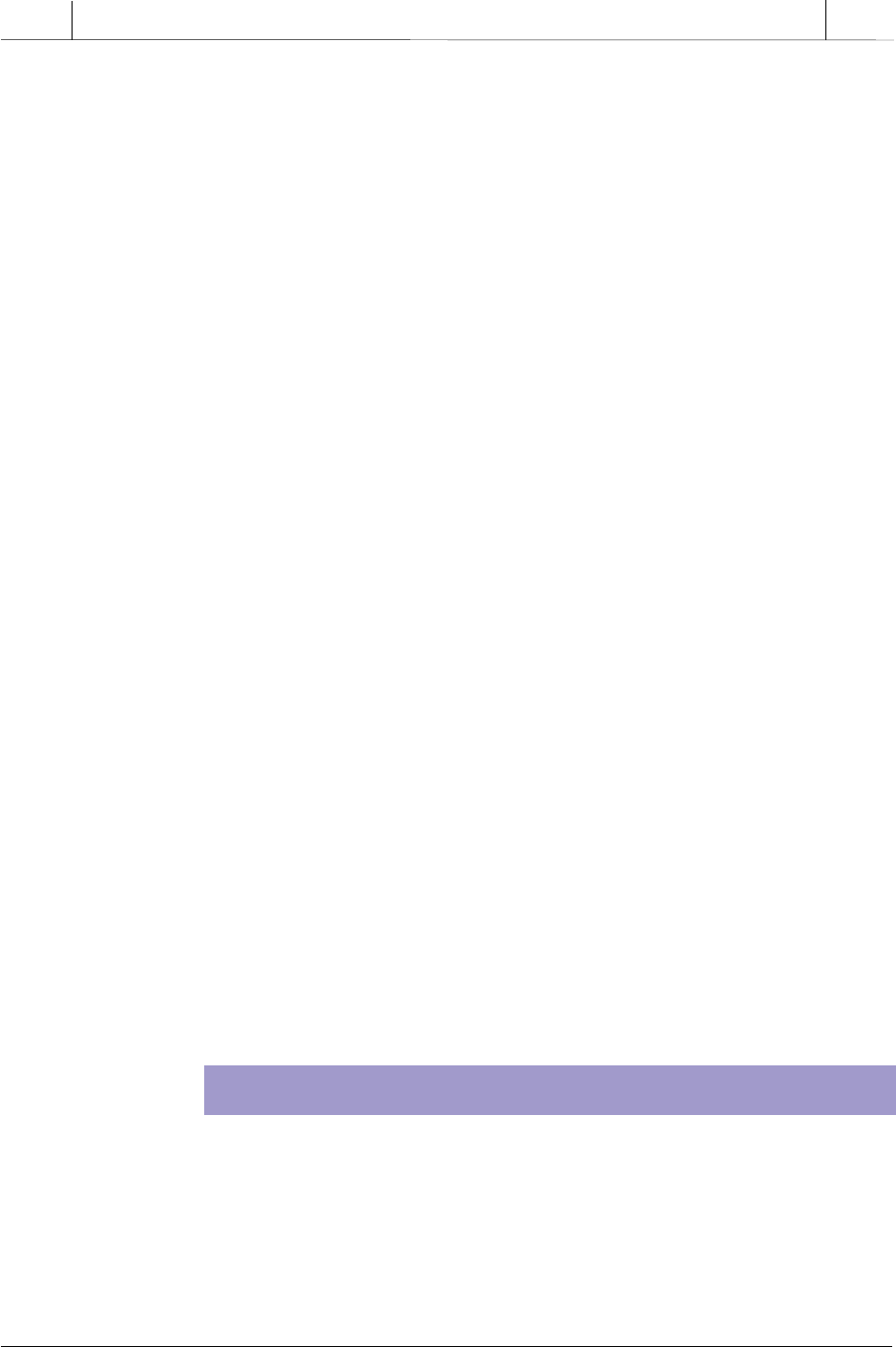
235
CHAPTER
8
Special Function I/O and
Serial Communication Interfacing
Industrial Text & Video Company 1-800-752-8398
www.industrialtext.com
SECTION
2
Components
and Systems
rotation over distance by outputting a fixed number of pulses per shaft
rotation. The module provides two pulse signals that have a 90° phase
difference (quadrature); it then determines the direction of rotation by sensing
which of the two pulse channels is the leading waveform. Incremental
encoders provide a marker, or index, channel that sends a pulse for every
shaft revolution. This marker, which is an input to the module, can be used in
conjunction with the module’s limit switch channel input to establish a
home position along the encoder’s measurements. When the encoder inter-
face is used in a counter configuration, however, only one input channel can
be connected to a device that provides a pulse count.
During operation, an encoder/counter module (in incremental encoder mode)
receives two pulse channel inputs that are counted and compared with a user-
specified preset value. The interface may have one or two output lines
available, which are energized once the incoming pulses are equal to, greater
than, or less than the preset values. The input channels and output lines
available are generally rated for TTL or for 12–48 VDC. The maximum input
pulse frequency that an encoder/counter interface can properly count ranges
between 50 and 60 kHz.
The communication between an encoder/counter interface and the processor
is bidirectional. The module accepts the preset value and other control data
from the processor and transmits values and status data to the PLC memory.
The interface also lets the PLC know when the marker and limit switch are
both energized, indicating a home position. On the other hand, the processor’s
control program, which tells the module to operate the outputs according to
the count value received, enables the output controls. The control program
also enables and resets the counter operation.
Typically, the length between the module and the encoder should not exceed
50 feet, and shielded cables should be used. Since encoder/counter modules
have both inputs and outputs, they have isolation between the input and
output circuits, as well as between the control logic and both I/O circuits. The
use of separate power supplies, which must be provided by the user, enhances
this isolation. Figure 8-19 shows the typical connections for an incremental
encoder configuration.
STEPPER MOTOR INTERFACES
Stepper motor interfaces, as their name implies, are used in applications
requiring control of stepper motors. Stepper motors are permanent-type
magnet motors that translate incoming pulses, through a stepper translator,
into mechanical motion. Stepper is a generic term that describes this type of
brushless motor capable of making fixed angular motions in response to a
step input.