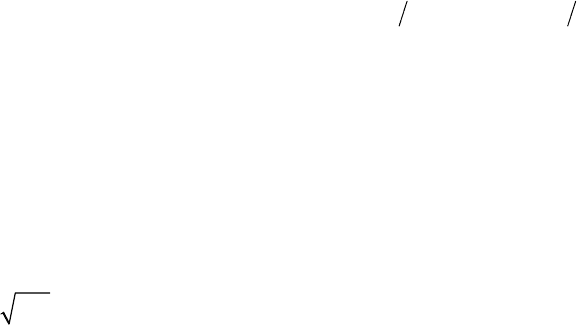
2010 SECTION VIII, DIVISION 2
4-81
4.4 Design of Shells Under External Pressure and Allowable Compressive Stresses
4.4.1 Scope
4.4.1.1 Paragraph 4.4 provides rules for determining the required wall thickness of cylindrical, conical,
spherical, torispherical, and ellipsoidal shells and heads subject to external pressure. In this context, external
pressure is defined as pressure acting on the convex side of the shell.
4.4.1.2 The effects of supplemental loads are not included in the design equations for shells and heads
included in paragraphs 4.4.5 to 4.4.9. The effects of supplemental loads that result in combined loadings
shall be evaluated in a separate analysis performed in accordance with the methods in paragraph 4.4.12.
4.4.1.3 Rules are also provided for the design of cylindrical-to-conical shell transition junctions in
paragraphs 4.4.13 and 4.4.14. To facilitate the use of these rules, it is recommended that the shell wall
thickness and stiffener configuration, as applicable, first be designed using the rules in paragraphs 4.4.5
through 4.4.9. After an initial design is determined, this design should then be checked and modified as
required using the rules of paragraphs 4.4.13 and 4.4.14.
4.4.1.4 The equations in this paragraph are applicable for
2000
o
Dt
. If 2000
o
Dt> , then the
design shall be in accordance with Part 5. In developing the equations in the paragraph, the shell section is
assumed to be axisymmetric with uniform thickness for unstiffened cylinders and formed heads. Stiffened
cylinders and cones are also assumed to be of uniform thickness between stiffeners. Where nozzles with
reinforcing plates or locally thickened shell sections exist, the thinnest uniform thickness in the applicable
unstiffened or stiffened shell section shall be used for the calculation of the allowable compressive stress.
4.4.1.5 Special consideration shall be given to ends of components (shell sections) or areas of load
application where stress distribution may be in the inelastic range and localized stresses may exceed those
predicted by linear theory.
4.4.1.6 When the localized stresses extend over a distance equal to one-half the length of the buckling
mode (approximately
1.2
o
Dt), the localized stresses shall be considered as a uniform stress for the design
of the shell section.
4.4.1.7 The buckling strength formulations presented in this paragraph are based upon linear structural
stability theory which is modified by reduction factors which account for the effects of imperfections, boundary
conditions, non-linearity of material properties and residual stresses. The reduction factors are determined
from approximate lower bound values of test data of shells with initial imperfections representative of the
tolerance limits specified in this paragraph.
4.4.2 Design Factors
The allowable stresses are determined by applying a design factor,
FS , to the predicted buckling stresses.
The required values of
S
are 2.0 when the buckling stress is elastic and 1.667 when the predicted buckling
stress equals the minimum specified yield strength at the design temperature. A linear variation shall be used
between these limits. The equations for
FS are given below where
ic
F is the predicted buckling stress that
is determined by setting
1.0FS =
in the allowable stress equations. For combinations of design loads and
earthquake loading or wind loading (see paragraph 4.1.5.3), the allowable stress for
bha
F or
ba
F in Equations
(4.4.106), (4.4.107), (4.4.108), (4.4.111), (4.4.112) and (4.4.113) may be increased by a factor of 1.2.
2.0 0.55
ic y
FS for F S=≤ (4.4.1)