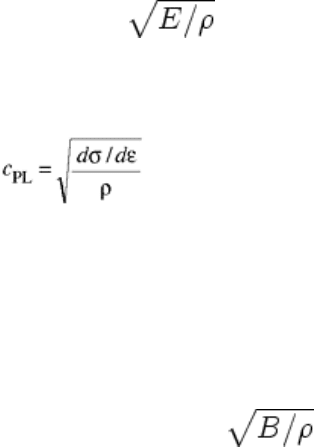
the ram is attempting to apply, and the no-load speed may be much higher than the full-load speed. The
distance traveled may also affect the speed capability. A long-stroke machine may attain a given speed only
after a significant amount of travel. Depending on the specimen length, considerable specimen strain could
occur before final maximum velocity is obtained in a tension test. Finally, the ability to control speed is a
function of the response capability of a servo-controlled machine working in a closed-loop mode. Open-loop
machines provide speeds that can be influenced by specimen strength and cannot easily reproduce
predetermined velocities or strain rates on materials with different yield strengths or strain hardening behaviors.
Load cell ringing at intermediate or medium strain rates may be negligible. However, even if wave propagation
effects in the test piece can be neglected, the characteristic response time of load cells must still be checked. At
intermediate strain rates, “ringing” of a load cell can mask the desired measurement. Load cell ringing is
frequently encountered in high-rate tensile testing. Generally, the load-cell response time (which is the
reciprocal of its natural frequency in hertz) must be small compared to the total duration of the test. For
example, if a load cell has a natural frequency of 1 kHz, its period of vibration is 10
-3
s. This load cell could
then be used only for experiments that lasted over ten times that amount, or over 10 μs.
Another condition that must be satisfied is the distance of the load cell from the end of the specimen. If a
sufficient distance exists between the specimen and load cell, the finite elastic wave transit time may result in
load data that are not time-coincident with strain data. To prevent phase lags from obscuring the experimental
data, the wave transit time from the specimen to load cell should be negligibly small compared to the test
duration. Otherwise, the load data must be corrected for the delay, and such corrections seldom are precise.
Wave Propagation Effects. At high strain rates, uniform deformation within the test piece becomes a factor.
Inertia initially opposes uniform deformation, and a stress wave is transmitted and reflected within the test
piece at the speed of sound. If the deformation is purely elastic, then the longitudinal sound velocity, c
EL
, is
simply c
EL
= , where E is the elastic modulus and ρ is density. If the material has deformed into the
plastic region, the plastic-wave velocity is more appropriate and generally can be an order of magnitude smaller
than the elastic wave velocity. One-dimensional strain-rate-independent theory predicts that the plastic wave
propagates at a velocity, c
PL
, determined by:
(Eq 4)
where dσ/dε is the slope of the true stress/true strain curve. For many materials, the initial work-hardening rate
dσ/dε is approximately 1% of E; thus for these materials, the plastic wave velocity is approximately 10% of the
elastic-wave velocity.
However, experimental evidence in a variety of metals suggests that the above estimate is too conservative. The
stress waves generated by impacts at stress levels far in excess of the yield stress appear to travel, at least
initially, closer to the elastic wave velocity rather than at the plastic wave velocity (Eq 4). This implies that the
wave propagation behavior can be more complicated than described by Eq 4. The velocity of the plastic wave is
sometimes estimated as where B is the bulk modulus.
The velocity of waves and the size of the test piece determine the upper limit of strain rate for accurate
measurement of stress-strain curves. If many wave transits occur during a test, the use of average stresses and
strains can be justified. However, if only a few wave reflections occur before the specimen fails, then individual
wave propagation must be considered. In this case, average values alone cannot be considered, and the use of
this test to determine dynamic stress-strain response is precluded. As a first approximation, Davies and Hunter
(Ref 3): have estimated that three reverberations are required for stress equilibration in compression testing.
To illustrate the importance of stress wave propagation, consider compression testing of a 10 mm (0.4 in.)
specimen, in which the elastic wave velocity is 5.0 × 10
3
m/s (16.4 × 10
3
ft/s) and the initial plastic wave
velocity may be approximated as 5.0 × 10
2
m/s (16.4 × 10
2
ft/s). Assuming that three reverberations of the
slower moving plastic wave are required for uniform stress within the deforming specimen, the time for these
reverberations is computed to equal 60 μs. At a strain rate of 10
3
s
-1
, the specimen will have compressed to a
strain of 6% during this interval. Thus, data at strains less than this may be invalid, because it cannot be
assumed that the specimen was deforming uniformly. Even if the elastic wave velocity is used in the above
example, the critical strain at which uniform stress within the specimen is achieved is computed to be equal to
0.6%. At a strain rate of 10
4
s
-1
, this critical strain becomes 6%.