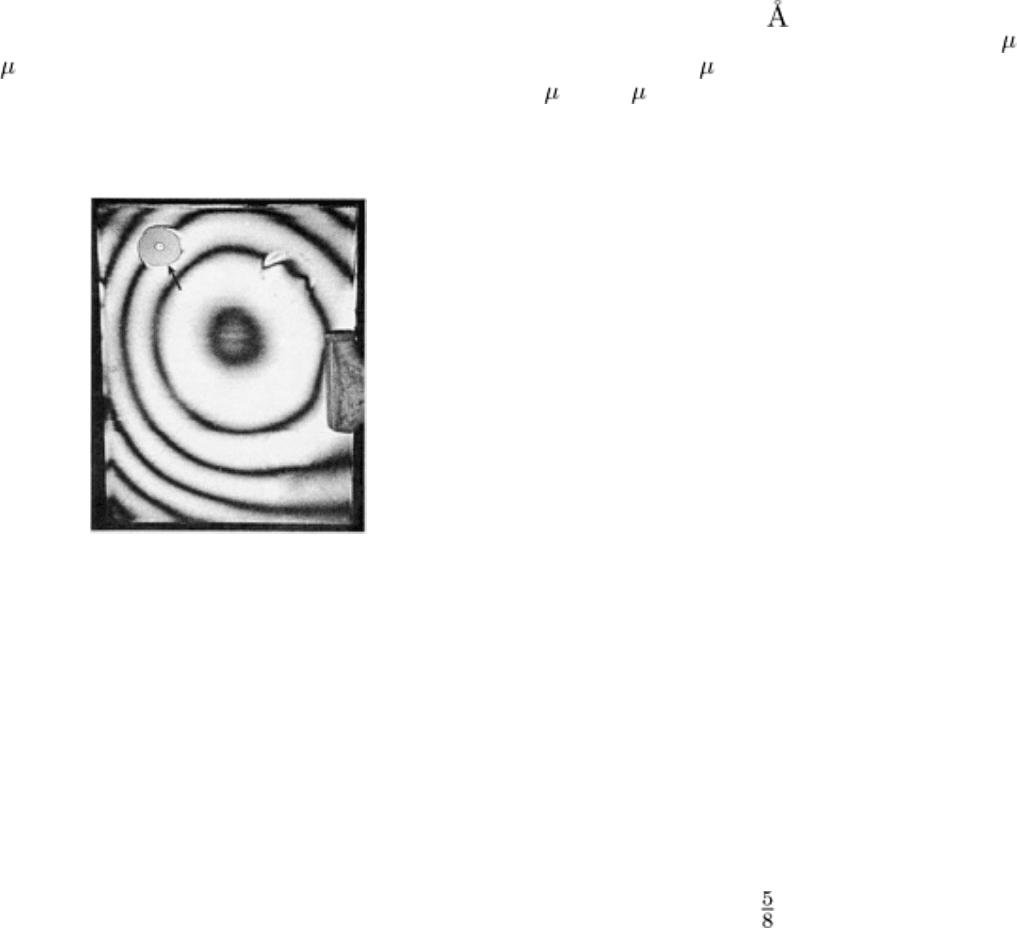
A typical set of fringes caused by a debond in a honeycomb-core sandwich panel is illustrated by the interferogram in Fig.
12, which demonstrates the sensitivity of inspection by thermal stressing. This interferogram was obtained using the
double-exposure technique and a pulsed ruby laser, which has a wavelength of 694 nm (6940 ) (Table 1). Using Eq 3, it
can be seen that each fringe, except the first, represents an out-of-plane displacement of 0.694/(2 sin 90°), or about 0.33
m (13 in.). The region above the debond in the panel, which had a face sheet 500 m (0.02 in.) thick and was heated
only about 2.8 °C (5 °F), has a maximum displacement of about 3 m (120 in.), or only about 0.6% of the face sheet
thickness.
Example 2: Holographic Detection
of a Debond in a Sandwich
Structure Using the Vacuum-
Stressing Method.
Inspection by vacuum stressing has also been found to
be effective for detecting debonds in sandwich
structures. Figure 10 shows the essential components
of a portable holographic analyzer for the inspection
of sandwich panels. This analyzer consists of two
separate sets of equipment: one set for vacuum
stressing and holographic recording (Fig. 10a) and
one set for holographic reconstruction (Fig. 10b). The
holographic recording system is mounted on the top
of a hollow supporting structure that rests on the test
panel. The recording system contains a 3-mW CW
helium-neon laser and, through the use of suitable
optical components, encompasses a 460 mm (18 in.)
diam circular field of view of the portion of the panel
surface beneath the supporting structure.
During an inspection, the vacuum chamber, which is
made of fiberglass, is lowered over the recording
system until contact is made with the surface of the
panel. A first exposure is made of the panel in its
unstressed state. A second exposure is made when the
internal pressure has been reduced by approximately 7
kPa (1 psi). The pressure of the ambient air in the core voids pushes the face sheets out at unbonded regions. The double-
exposure hologram is recorded as a circular field 8 mm (0.3 in.) in diameter on a 16 mm ( in.) film strip. The film is
then advanced, the vacuum is released, the system is moved to the next location on the panel, and the sequence is
repeated. The total time required for constructing a double-exposure hologram is usually about 1 min or less. By using a
film strip 2030 mm (80 in.) long, it is possible to record a total of more than 200 double-exposure holograms.
A typical commercial holographic analyzer for the inspection of sandwich structures is illustrated in Fig. 13. It
consists of a 3.7 × 2.4 m (12 × 8 ft) table supported on air bearings. On this table is a part-holding mounting plate, which
is supported by two 1220 mm (48 in.) diam trunnion plates. The mounting plate can be rotated and translated to view
either flat panels or curved shapes. The holographic system usually uses a 50-mW helium-neon laser, but can also use
higher-powered argon lasers. The part to be inspected is held in place on the mounting plate by a series of vacuum cups or
clamps. Thermal, vibrational, pressure or vacuum stressing can be applied. A part measuring up to 1.5 × 1.8 m (5 × 6 ft)
can be inspected with this analyzer. Other analyzers are available that are designed to handle either smaller parts or larger
parts (up to 1.8 × 6.1 m, or 6 × 20 ft).
Fig. 12 Double-exposure time-lapse inter
thermally stressed honeycomb-
showing a fringe pattern (arrow) contouring a region of the
front face sheet over a debond. The panel had metal face
sheets 500 μ
m (0.02 in.) thick and was heated about 2.8
°C (5 °F) between exposures, which were made with a
pulsed ruby laser. The fringes indicate a maximum
displacement over the debond of 3 μm (120 μ
background fringes were caused by general movement of
the face sheet due to heating.