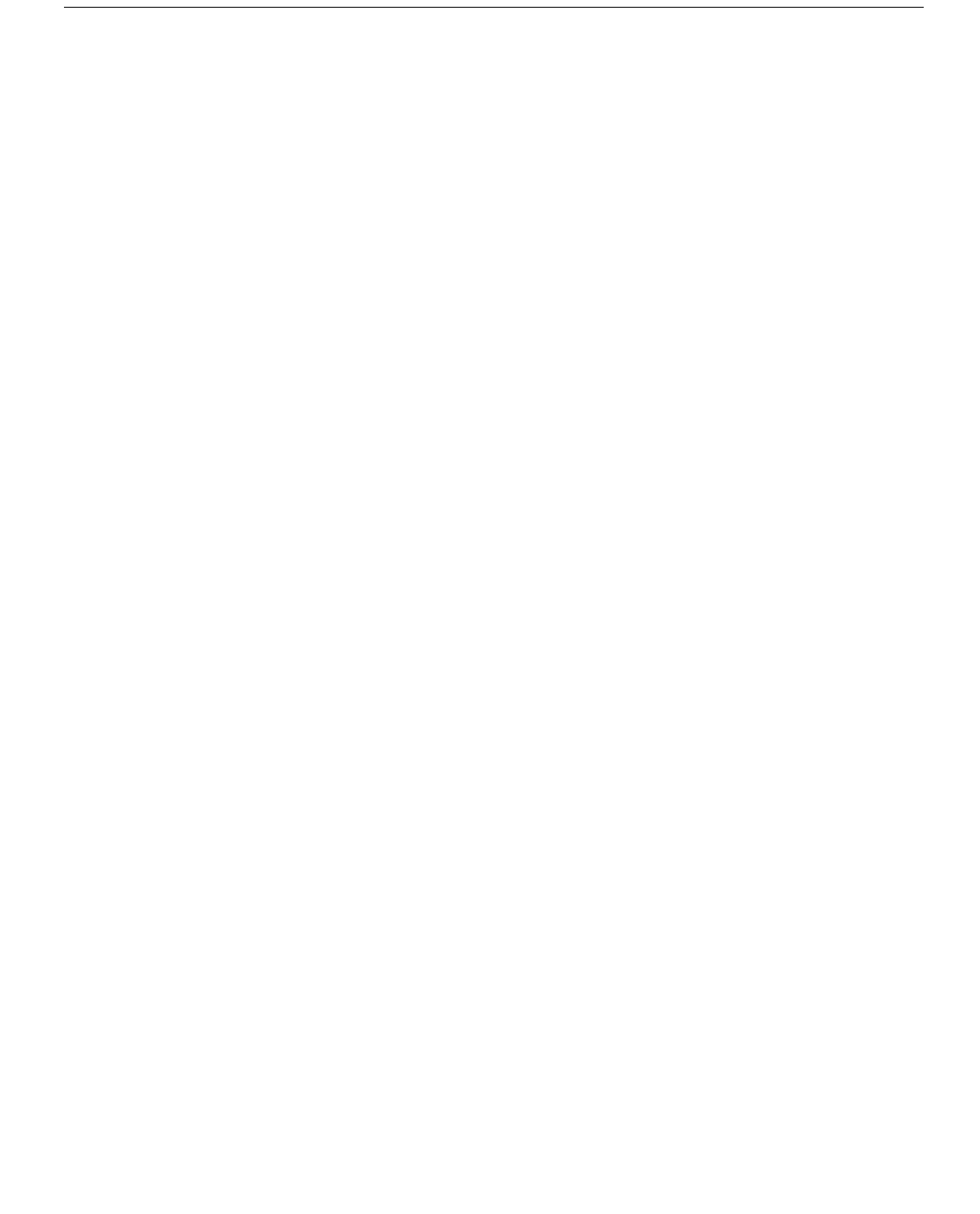
56 API STANDARD 618
7.9.4.2.4.2 Step 3a—Mechanical Natural Frequency Analysis of the Compressor and Piping System to Avoid
Coincidence with Significant Shaking Forces
a. The starting point of the mechanical model is either the crankcase-to-foundation interface or the crosshead guide-to-crankcase
interface. For modeling accuracy, this location shall be relatively rigid when compared to the rest of the compressor mechanical
model and/or it shall be accurately described by a six degree of freedom spring. The compressor mechanical model end point is
the second pipe clamp on the suction and discharge piping moving away from the line side nozzles of the pulsation suppression
devices. The factors that can influence the accuracy of the model are discussed in more detail in API 688. If specified, this
modeling will also include an analysis of the stresses found in the pulsation suppression device internals in accordance with
7.9.5.1.22 and 7.9.5.1.23.
Note 1: The intent is to avoid mechanical resonance of the compressor cylinders, pulsation suppression devices, and piping system at
frequencies where high shaking forces also exist.
Note 2: In some cases the compressor frame, crosshead guides and cylinders, mounted on a concrete foundation, can be considered to be
relatively rigid, and can be modeled using rigid elements.
Note 3: The compressor and pulsation suppression device mechanical model was formerly known as the compressor manifold model.
b. An analysis of the compressor and piping system shall be done to predict the mechanical natural frequencies. The mechanical
and acoustic system shall be designed to meet the separation margin criteria of 7.9.4.2.5.3.2 and the shaking forces shall not
exceed the limits found in 7.9.4.2.5.2.3.
Note: Geometrically-complex areas of the system such as cylinders, distance pieces, crosshead guides, frames, pulsation suppression device
nozzles, and piping, where span calculations cannot be applied accurately, are analyzed to determine mechanical natural frequencies, usually
with vendor proprietary methods, shop measured data, or finite element methods; with the intent of avoiding mechanical resonances at
frequencies where significant shaking forces also exist
7.9.4.2.4.3 Step 3b1—Forced Mechanical Response Analysis of the Compressor Mechanical Model
When the excitation frequency separation margins or the shaking force amplitude guidelines for pulsation suppression devices
cannot be met, a forced-mechanical-response analysis of the compressor mechanical model to the pulsation-induced forces and
cylinder-gas forces shall be performed. The allowable cyclic stress criteria in 7.9.4.2.5.2.5 shall apply. The compressor vendor
shall supply the allowable vibration limits for compressor components such as cylinders, distance pieces and crankcases.
Note: The allowable compressor vibration levels are generally the limiting design criteria. This analysis predicts the cyclic stress in the pulsation
suppression devices and associated piping. It is not intended that analysis of the cyclic stresses in the compressor components be included in this
design approach. The compressor components are included in the model only for the purpose of enabling the analysis of the effects of their
flexibility and dynamic movement on the pulsation suppression devices. The compressor manufacturer is expected to provide vibration criteria
to ensure that no fatigue failures or premature wear of compressor components occur, in accordance with 6.1.1.
7.9.4.2.4.4 Step 3b2—Forced Mechanical Response of the Piping System
When the excitation frequency separation margins or the shaking force amplitude guidelines for the piping system cannot be met,
a forced-mechanical response analysis of the piping system to acoustic shaking forces shall be performed. The allowable
vibration and cyclic stress limits in 7.9.4.2.5.2.4 and 7.9.4.2.5.2.5 respectively shall apply. The model end points shall be defined
by the analyst in agreement with the purchaser; in general, the piping system model should include all of the piping that was
included in the acoustic model. Factors that can influence the accuracy of the model are discussed in more detail in API 688.
When forced mechanical response analysis of the piping system is performed without doing a forced mechanical response
analysis of the compressor mechanical model, the starting point of the piping system is at the compressor cylinder flanges, which
are assumed to be rigid.
Note: As with Step 3b1, the vibration is generally the limiting design consideration, because when the vibration levels are within the
recommended allowable limits, the allowable stress levels are usually not approached. The exception is where high stress concentrations occur
at large diameter reductions such as nozzle connections and weldolets for small piping on significantly larger piping.
7.9.4.2.5 Design Criteria
7.9.4.2.5.1 General
Pulsation suppression devices and techniques applied in accordance with Design Approaches 1, 2, and 3 shall satisfy the basic
criteria in 7.9.4.2.5.2, and the other criteria in 7.9.4.2.5.3.
Copyright American Petroleum Institute
Provided by IHS under license with API
Licensee=IHS Employees/1111111001, User=Japan, IHS
Not for Resale, 01/01/2008 21:15:45 MST
No reproduction or networking permitted without license from IHS
--```,`,,,,`,``,,```,`,,`,,,,`-`-`,,`,,`,`,,`---