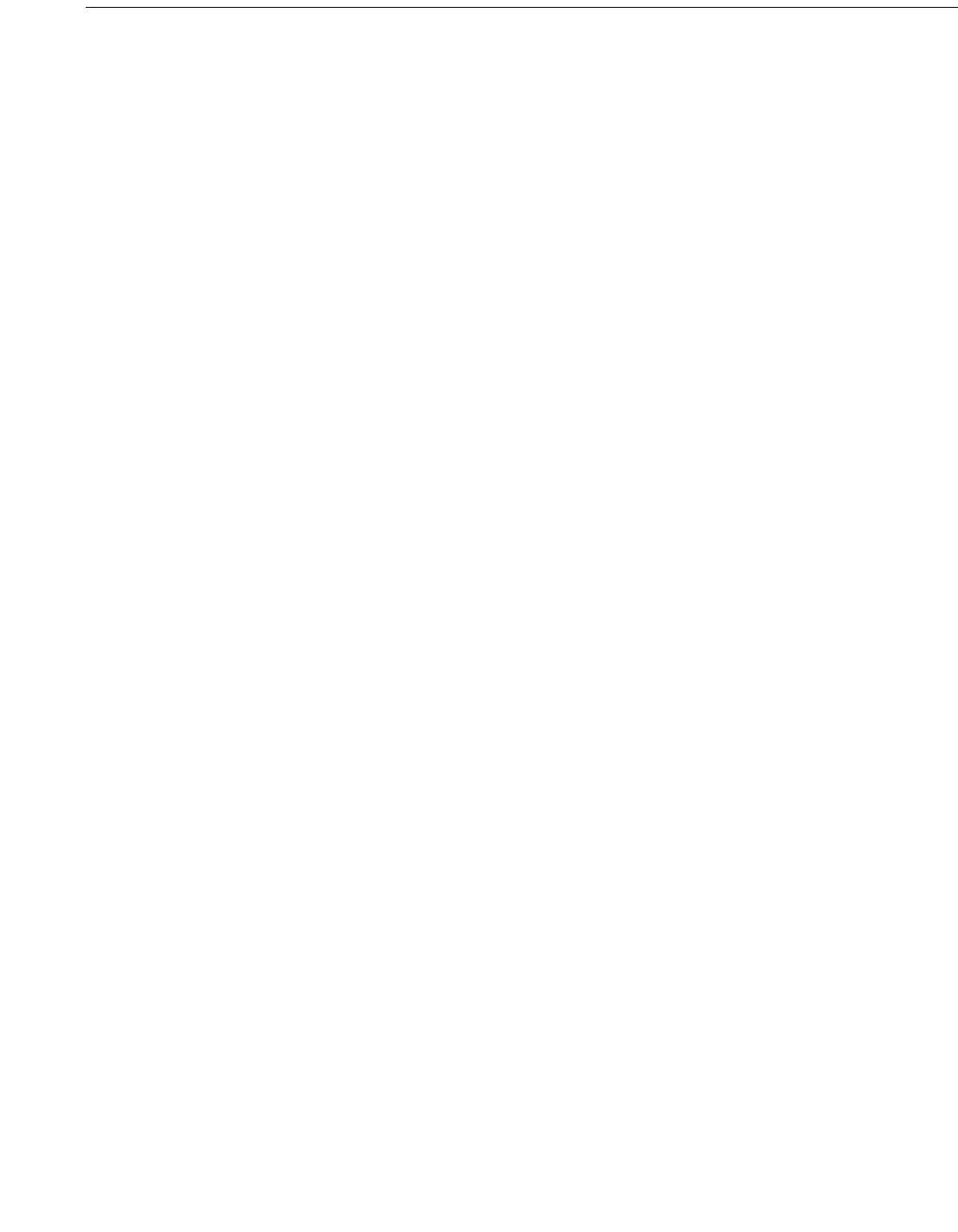
RECIPROCATING COMPRESSORS FOR PETROLEUM, CHEMICAL, AND GAS INDUSTRY SERVICES 35
Unless otherwise specified, weld procedures for major repairs shall be subject to review by the purchaser prior to any repair.
6.15.7.4 Connections welded to pressure-containing parts shall be installed as specified in 6.15.7.5 through 6.15.7.9.
6.15.7.5
•
If specified, in addition to the requirements of 6.15.7.1, specific welds shall be subjected to 100% radiography or
magnetic particle inspection or liquid penetrant inspection of welds.
6.15.7.6
•
If specified, proposed connection designs shall be submitted to the purchaser for acceptance before the start of
fabrication. The drawings shall show weld designs, size, materials, and pre- and postweld heat treatments.
6.15.7.7 All welds shall be heat treated in accordance with the specified pressure vessel code or an internationally recognized
standard such as the ASME Section VIII, Division 1, Sections UW-10 and UW-40. For steels in H
2
S service, heat treatment shall
also be in accordance with NACE MR0175 (see 6.15.1.11).
6.15.7.8 If postweld heat treatment is required it shall be carried out after all welds, including piping welds, have been
completed.
6.15.7.9 Auxiliary piping welded to alloy steel casings and cylinders shall be of a material with the same nominal properties as
the casing or cylinder material or shall be of low carbon austenitic stainless steel. Other materials compatible with the casing or
cylinder material and intended service may be used with the purchaser's approval.
6.15.7.10 Flux-core welding may be used for equipment in hydrogen service, upon written agreement of the purchaser after
submission of weld procedures.
6.15.8 Low-temperature Service
6.15.8.1
•
The minimum design metal temperature and concurrent pressure used to establish impact test and other material
requirements shall be as specified.
Note: Minimum temperature can be caused by operating and/or environmental conditions including auto-refrigeration, and low ambient
temperatures during shipping, installation, operation or shutdown.
6.15.8.2 To avoid brittle failures, materials and construction for low temperature service shall be suitable for the minimum
design metal temperature in accordance with the codes and other requirements specified. The purchaser and the vendor shall
agree on any special precautions necessary with regard to conditions that can occur during operation, maintenance, transportation,
erection, commissioning and testing.
Note: Good design practice should be followed in the selection of fabrication methods, welding procedures, and materials for vendor furnished
steel pressure-retaining parts that can be subject to temperatures below the ductile-to-brittle transition temperature. The published design-
allowable stresses for many materials in internationally recognized standards such as the ASME Code and ANSI standards are based on
minimum tensile properties. Some standards do not differentiate between rimmed, semi-killed, fully-killed hot-rolled, and normalized material,
nor do they take into account whether materials were produced under fine- or course-grain practices. The vendor should exercise caution in the
selection of materials intended for services between –30°C (–20°F) and 40°C (100°F).
6.15.8.3 All carbon and low alloy steel pressure-containing components, including nozzles, flanges, and weldments, shall be
impact tested in accordance with the requirements of ASME Section VIII, Division 1, Sections UCS-65 through 68, or the
specified pressure design code. High-alloy steels shall be tested in accordance with ASME Section VIII, Division l, Section
UHA-51, or the specified pressure design code. For materials and thickness’ not covered by ASME Section VIII, Division l or the
specified pressure design code, testing requirements shall be as specified by the purchaser.
Note: Impact testing of a material may be omitted depending on the minimum design metal temperature, thermal, mechanical and cyclic loading
and the governing thickness. Refer to requirements of ASME Section VIII, Division l, Section UG-20F, for example.
6.15.8.4 The governing thickness used to determine impact testing requirements shall be the greater of the following.
a. The nominal thickness of the largest butt-welded joint.
b. The largest nominal section for pressure containment, excluding
1. structural support sections such as feet or lugs,
2. sections with increased thickness required for rigidity to mitigate shaft deflection,
3. structural sections required for attachment or inclusion of mechanical features such as jackets or seal chambers;
c. One fourth of the nominal flange thickness (recognizing that the predominant flange stress is not a membrane stress).
Copyright American Petroleum Institute
Provided by IHS under license with API
Licensee=IHS Employees/1111111001, User=Japan, IHS
Not for Resale, 01/01/2008 21:15:45 MST
No reproduction or networking permitted without license from IHS
--```,`,,,,`,``,,```,`,,`,,,,`-`-`,,`,,`,`,,`---