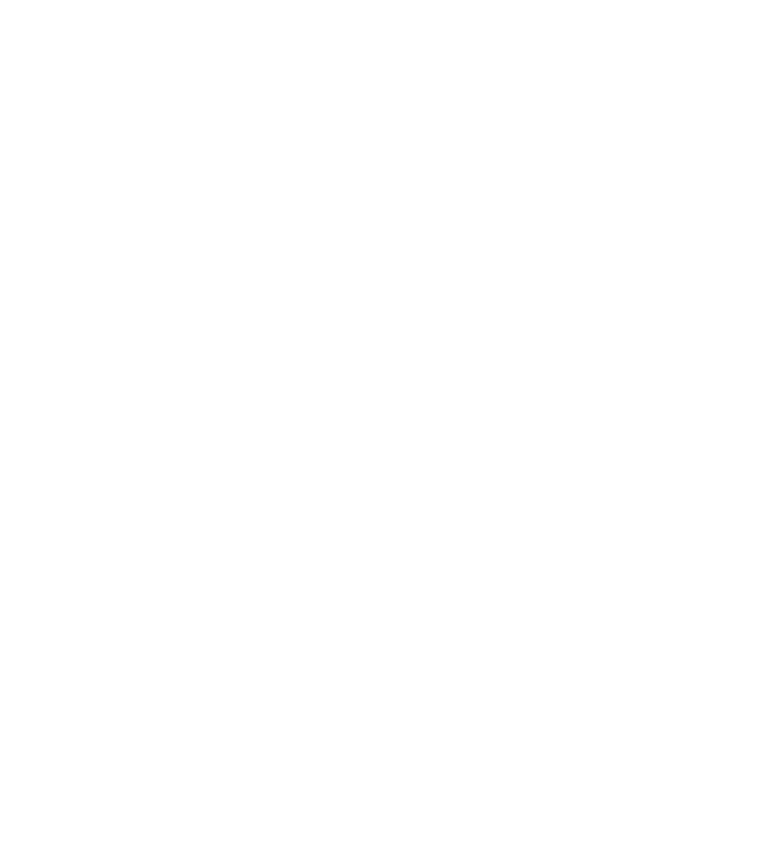
Both balanced-draught and induced-draught systems incorporate an ID fan, which can be sized to provide the
flow energy to achieve high stack effluent velocities. Alternatively, a longer stack can provide additional draught
and stack velocity while simultaneously providing a higher emissions point.
The four primary flue-gas pollutants of interest are discussed in F.10.3.2 through F.10.3.5.
F.10.3.2 Sulfur oxides
The sulfur oxide fraction of the flue gas depends solely on the composition of the gas or oil burned and is not
affected to any extent by the APH system. However, since fuel consumption is reduced when an APH system is
used, the mass of sulfur dioxide (SO
2
) emitted is reduced for any given process duty. This results in a net
reduction in SO
x
emissions (i.e. an environmental benefit).
F.10.3.3 Nitrogen oxides
The oxides of nitrogen produced depend on the time, temperature and the oxygen concentration of any specific
fuel’s combustion process. The reactions involved are many and complex. The following can be stated in general.
a) NO
x
produced increases with increasing firebox or combustion temperatures.
b) NO
x
produced decreases with decreasing excess air.
The above indicates that preheating combustion air increases NO
x
production. This has been shown to be true
when expressed as a concentration in the flue gas. However, as is the case with SO
x
, the total mass flow of NO
x
is usually reduced because of the lower flue-gas mass flow resulting from the higher heater efficiency. Thus, in
applications where APH systems yield substantial efficiency increases, the APH system actually reduces NO
x
emissions (i.e. an environmental benefit).
Excess air appears to be the most significant factor in the control of NO
x
formation. Since APH systems most
often utilize forced-draught burners, it is not only possible to operate at extremely low excess-air levels, but also to
more accurately control the fuel/air ratio. On natural-draught burners, the minimum excess-air levels previously
considered necessary to provide for operational variations have been 20 % on gas fuels and 25 % on oil fuels.
Most burner manufacturers represent that using their forced-draught designs and preheated air requires minimum
excess-air levels of only 5 % on gas and 10 % on oil fuels, and controls can be furnished to ensure that these
levels are maintained. This low excess-air operation reduces the NO
x
level.
F.10.3.4 Particulates
The formation of particulates during combustion is normally a function of burner application and the specific fuel
burned. The use of air preheat and forced-draught systems involved have enabled burner manufacturers to
reduce the formation of carbon when burning normal fuels. This can reduce the particulates formed to essentially
the ash content of the fuel. Therefore, the use of an APH system reduces the total solids emission from many
heater applications since the amount of fuel burned, and hence of ash emitted, is reduced.
F.10.3.5 Combustibles
The presence of combustibles, such as unburned hydrocarbons and carbon monoxide, in the flue gases from fired
heaters is related to the incomplete combustion of the fuel. This, in turn, can result from insufficient excess air.
The application of an APH system enhances the ability to burn fuels completely at the lowest possible excess air
level. As a result, unburned hydrocarbons and carbon monoxide pollution should be minimized with the
application of an APH system.
F.10.4 Noise
The main sources of noise from a fired heater are the burners and fan(s). The application of an APH system
requires that the burners be housed in an insulated enclosure. In addition, high-efficiency heater systems employ
ANSI/API Standard 560/ISO 13705
Copyright American Petroleum Institute
Provided by IHS under license with API
Licensee=TECNA/5935100001
Not for Resale, 09/06/2007 11:42:18 MDT
No reproduction or networking permitted without license from IHS
--```,``,`,`,```,``,,,,,,`,``-`-`,,`,,`,`,,`---