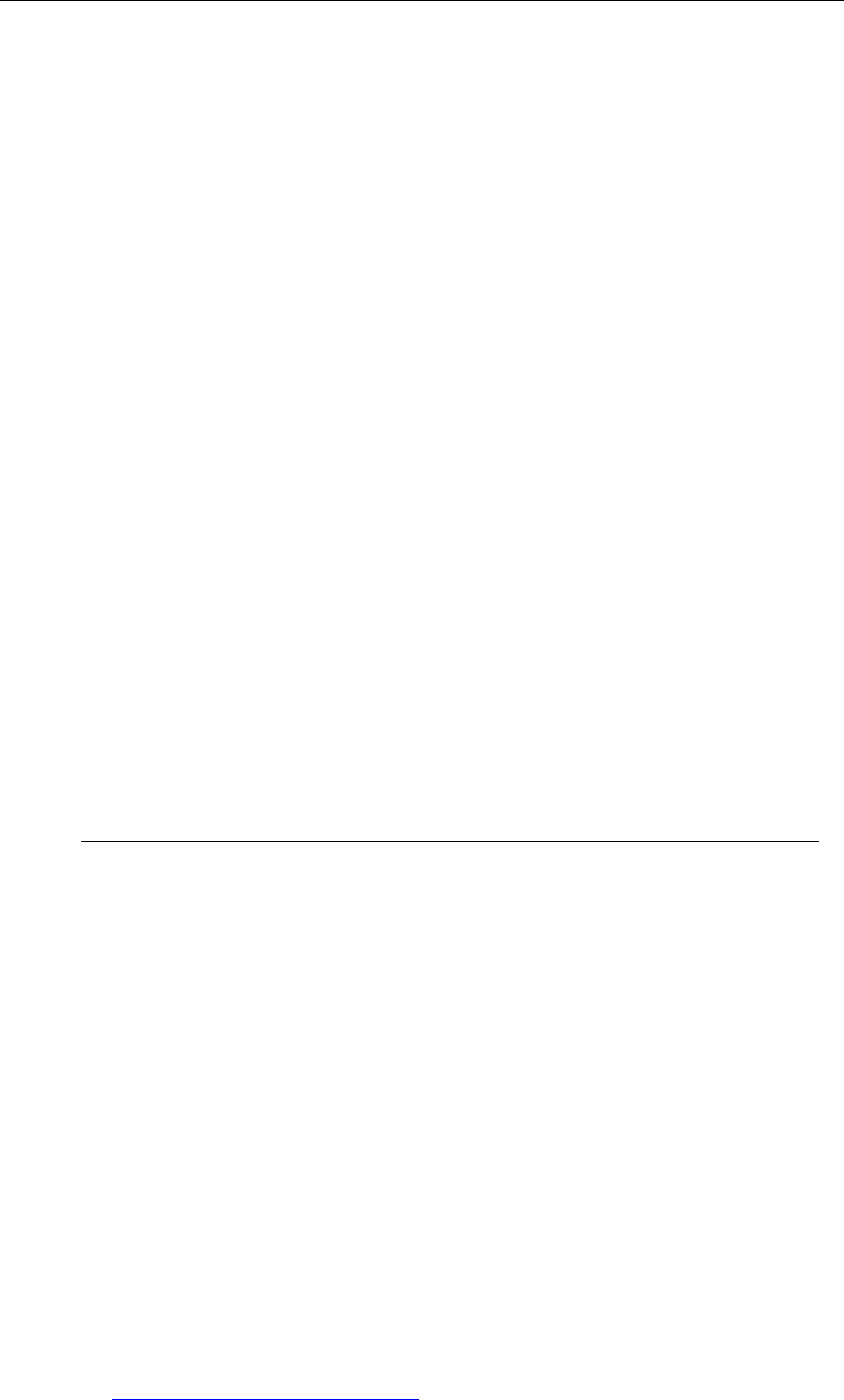
Paper F5: Performance management
436 Go to www.emilewoolfpublishing.com for Q/As, Notes & Study Guides © EWP
40 Planning and operational variances
CAD manufactures product X. In the annual budget for the current year, the
standard direct labour cost for Product X is:
3 hours per unit × $15 per hour = $45 per unit.
This cost was based on the expectation that new working procedures and new
equipment would be used to reduce the labour time per unit. The changes have not
yet been introduced, however, in retrospect, it is decided that a more appropriate
direct labour cost for product X should be:
4 hours per unit × $15 per hour = $60 per unit.
In the current period, 2,000 units of Product X were produced. These took 8,200
hours to make, and the direct labour cost was $120,800.
Required
(a) Reconcile the actual direct labour costs to the original standard costs, using
planning and operational variances.
(b) Show the planning and operational variances if 2,000 units were made in the
period in 8,200 hours at a direct labour cost of $101,600, and it was decided in
retrospect that the appropriate direct labour cost for product X should be:
4 hours per unit × $12 per hour = $48 per unit.
41 Size and share
The budgeted and actual annual sales of Pushing Company, and the budgeted and
actual variable cost of sale per unit, were as follows.
Budget Actual results
Sales volume Sales price Variable cost Sales volume Sales price Variable cost
units $ per unit $ per unit units $ per unit $ per unit
120,000 $10 $4 114,000 $10.50 $4
The budget was based on an estimate of 600,000 units for the total market size. At
the end of the year it was established that the actual total market size was 550,000
units.
Required:
Calculate the sales price variance, market size variance and market share variance,
and comment on the sales performance of the company.