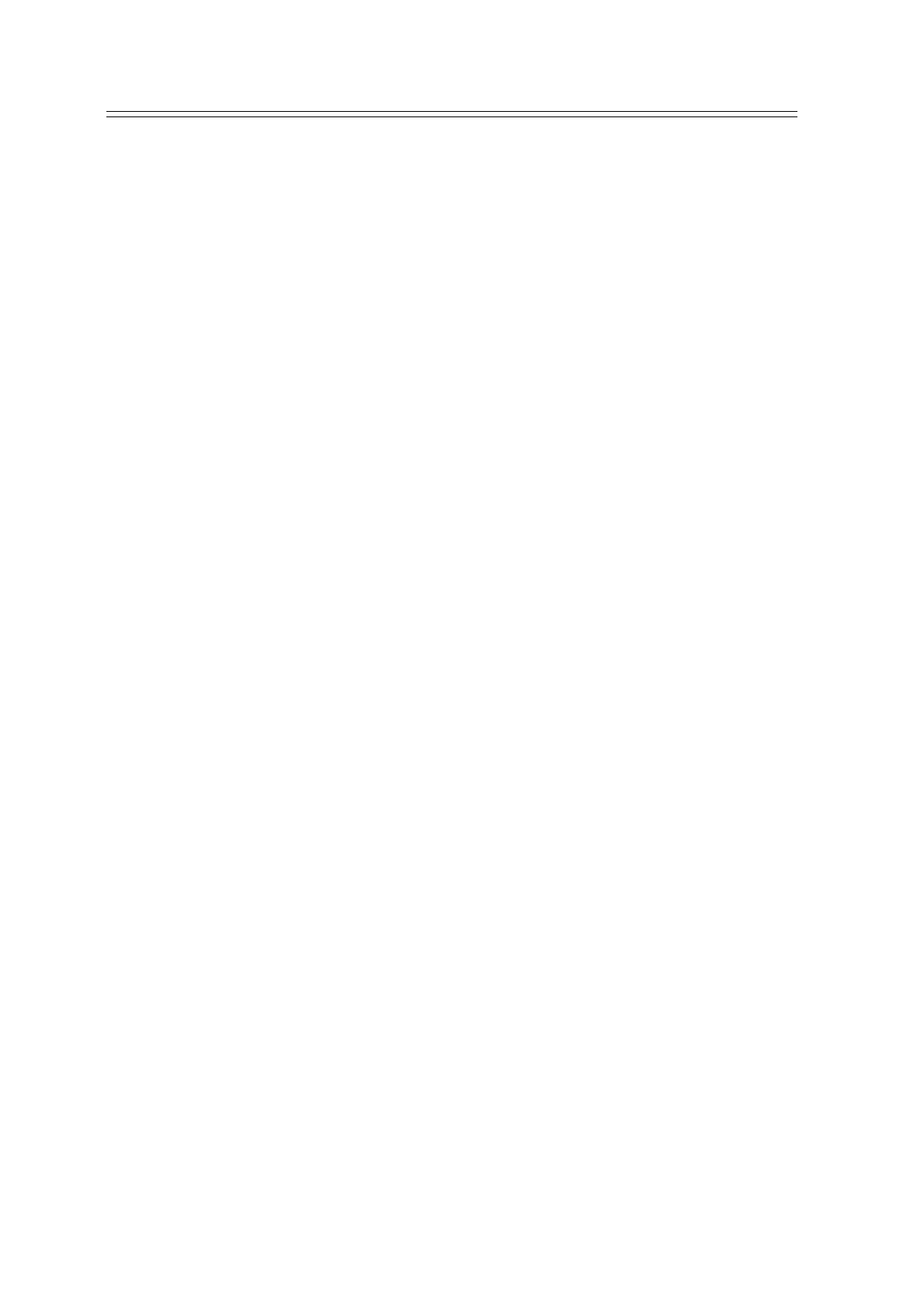
#
154
#
ëڇ̉‡ðÚËÁ‡ˆËfl Ë ÏÂÚðÓÎÓ„Ëfl
УДК 621.941
Я. В. Барабаш
ДОСЛІДЖЕННЯ ШОРСТКОСТІ ПОВЕРХНІ ДЕТАЛІ ПРИ
ТОЧІННІ ТИТАНОВИХ СПЛАВІВ ІЗ ЗАСТОСУВАННЯМ
ВІБРОАКУСТИЧНОГО СИГНАЛУ
©
Я. В. Барабаш, 2007
При точінні титанового сплаву віброакустична емісія може бути використана для
діагностики процесу точіння і оцінки шорсткості обробленої поверхні. Встановлено за-
лежність між середньою енергією RMS акустичного сигналу та шорсткістю обробленої
поверхні. За даними ВАЕ можна оцінювати шорсткість обробленої поверхні безпосеред-
ньо в процесі різання, що дозволить надалі створити методику моніторингу стану шор-
сткості
обробленої поверхні
Вступ
Віброакустична емісія (ВАЕ) є одним з найбільш
інформативних явищ для відображення фізичних
процесів, що відбуваються при різанні металів.
Фізичні принципи віброакустичної емісії пов’язані з
процесами тертя, руйнування і пластичної дефор-
мації і є високочастотними хвилями пружної дефор-
мації, що генерується в зоні різання.
Спроби використовувати ВАЕ для вивчення про
-
цесів різання, механізмів тертя і зносу робилися ще
раніше [1-3]. Але сучасний етап розробки та викори-
стання засобів діагностики характеризується інтен-
сивною комп’ютеризацією. Обчислювальна техніка
використовується на всіх етапах проектування діаг-
ностичних систем, але, безумовно, головна роль
припадає на процес обробки і аналізу діагностичної
інформації. Для діагностики методом ВАЕ розробка
ефективних алгоритмів запису
, обробки і аналізу
акустичних сигналів набуває в даний час особливої
актуальності [4].
Проблеми обробки віброакустичної інформації
обумовлені, перш за все, складністю і різноманіт-
тям процесів, які генерують сигнали ВАЕ. Крім того,
важливими чинниками, що визначають специфіку
пошуку інформативних діагностичних ознак, є по-
рівняно рисі зміни корисного сигналу при значних
рівнях перешкод, а також нестаціонарність
вимі-
рюваних сигналів.
Дослідження віброакустичних сигналів вико-
нується вже давно [4-6], але про створення загаль-
ного алгоритму аналізу виміряних сигналів говори-
ти ще зарано.
Як відомо, основними джерелами випроміню-
вання віброакустичних сигналів при точінні є на-
ступні три зони: площина зрушення; поверхня роз-
поділу різець-стружка; поверхня розподілу різець-
деталь.
У
даній статті описані результати дослідження
динаміки зміни спектру віброакустичного сигналу
при різних подачах S. Метою аналізу спектрограм
віброакустичного сигналу був пошук закономірно-
стей зміни спектру сигналу в залежності від подачі,
що змінювалась.
Методика та результати досліджень
Точіння титанової заготівки ВТ20 проводилося
різцями з вбудованим датчиком віброакустичної
емісії. Обробка проводилась на верстаті ТПК-
125ВМ
з ЧПУ. Вимірювання шорсткості здійснюва-
лися за допомогою приладу Surtface фірми «Taylor-
Hobson». Застосовували повздовжний різець, ос-
нащений круглою пластиною з BK-8 діаметром 7
мм з наступними геометричними параметрами:
α =
5°,
γ = 0°.
Схема експериментальної установки включала
наступні компоненти: широкосмуговий датчик ВАЕ,
попередній підсилювач і швидкодіючий АЦП, вбу-
дований в персональний комп’ютер. Сигнал ВАЕ
записували з частотою 44100 Гц. Після чого він
оброблявся спеціальним пакетом програм «Cool Edit
2000» для аналізу звукових сигналів: сигнал мас-
штабувався по амплітуді, проводилася фільтрація
для відсікання шумів роботи верстата, будувала-
ся спектрограма
та розраховувалася середня енер-
гія віброакустичного сигналу для кожного досвіду
(періоди врізання і виходу різця не враховували-
ся).
Спектрограму будували за допомогою швидко-
го перетворення Фур’є з використанням згладжу-
вання по методу Блекмана-Харріса при кількості
вибірок 4096 і частоті 48000 Гц, так як використову-
вали звукову карту оскільки .
Для фільтрації сигналу
в кожному експерименті
записувався нетривалий за часом сигнал (5-10 с)
при працюючому верстаті та включеній подачі, а
потім спектр цього сигналу програмно віднімався
із спектру сигналу, отриманого при різанні. Таким
чином, після фільтрації віброакустичний сигнал не
містив в собі частоти, що відповідають сигналам
від верстата і електродвигунів головного руху та
подачі, тертя в передачах, що
направляють.
Було проведено експерименти, при таких ре-
жимах: глибина різання t = 0,2 мм, швидкість V