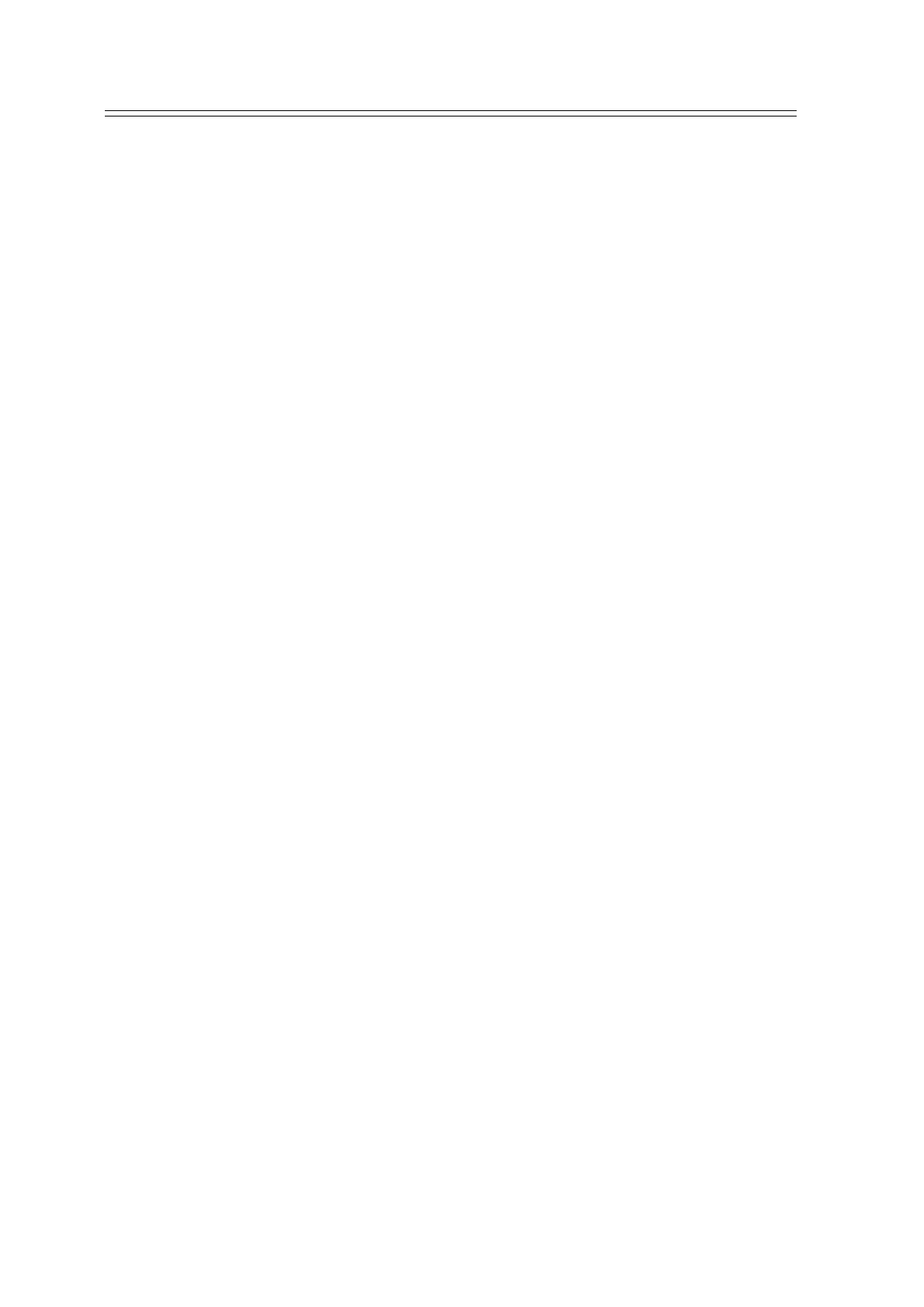
íÂıÌÓÎÓ„Ëfl ÔðÓËÁ‚Ó‰ÒÚ‚‡ Ë ðÂÏÓÌÚ‡
#
114
#
требует небольших (по сравнению с воздействием
на течение в целом) энергетических затрат. Этим и
обусловлена высокая эффективность тех способов
управления интенсивностью обменных процессов
турбулентного потока с охлаждаемой поверхнос-
тью, которые основаны на воздействии на пристен-
ную турбулентность.
Выполненный ранее анализ возможностей ин-
тенсификации теплоотдачи за счет наложения на
поток жидкости периодических воздействий [7]
показал,
что рациональное применение ультразву-
ка позволяет до 1,25 раза увеличить теплоотдачу.
Это, в свою очередь, как следует из рис. 1, откры-
вает возможность до 7 раз сократить расход пода-
ваемой СОЖ через зоны контакта инструмента и
заготовки при фиксированном значении отводимо-
го из нее теплового потока. Вместе с тем, на прак-
тике часто экономически
более целесообразна ре-
ализация преимущества от интенсификации тепло-
отдачи и уменьшения тепловой напряженности в
зоне обработки не путем сокращения расхода по-
даваемой СОЖ, а путем форсирования произво-
дительности обработки. В последнем случае, по-
мимо всего прочего, пропорционально снижению
машинного времени уменьшается норма расхода
СОЖ на одну заготовку [1].
Экспериментальные исследования проводили
на установке, созданной
на базе плоскошлифоваль-
ного станка мод. 3Г71, оснащенной динамометри-
ческой аппаратурой и аппаратурой для измерения
контактной температуры методом полуискусствен-
ной термопары, одним электродом которой служи-
ла обрабатываемая заготовка, а другим – хроме-
левая проволока диаметром 0,1 мм. СОЖ подава-
ли поливом, а также с использованием ультразву-
ковой техники к торцам круга через клиновые
на-
садки [8]. При этом максимальное расхождение
между расчетными и экспериментальными значе-
ниями температур не превышало ± 8 %.
Обсуждение результатов
На рис. 2 в качестве примера представлены
результаты экспериментального исследования и
численного моделирования на основе теплофизи-
ческого анализа по методике [3] производительно-
сти процесса плоского маятникового шлифования
заготовок с применением различной техники пода-
чи СОЖ в зону обработки
.
Поскольку, как показали предварительные ис-
следования, увеличение производительности на
этой операции лимитируется образованием прижо-
гов на шлифованных поверхностях, выполняли
детальный теплофизический анализ зоны шлифо-
вания с использованием предложенной модели. По
результатам этого анализа определяли области
режимов бездефектного шлифования, при которых
контактная температура не превышала критичес-
кой температуры вторичных структурно-фазовых
превращений в поверхностном
слое шлифованных
деталей. Области режимов бездефектного шлифо-
вания строили в логарифмической координатной
плоскости, по оси абсцисс которой откладывали
величину врезной подачи шлифовального круга, а
по оси ординат– скорость подачи стола. В такой
плоскости изолинии удельной производительнос-
ти представляют собой семейство параллельных
прямых (штриховые линии на рис. 2). Удельную про-
изводительность Q, мм
2
/с, подсчитывали по сле-
дующей зависимости:
*67,16 tVQ
c
,(3)
где V
c
– скорость продольной подачи стола, м/мин; t*
– критическая глубина шлифования, при которой
для заданной скорости V
c
контактная температура
в зоне шлифования равна минимальной темпера-
туре отпуска, мм/дв.х.
Критическую глубину t* определяли как по ре-
зультатам серии расчетов теплового состояния, так
и по результатам измерения контактной температу-
ры, полагая по рекомендациям [9] минимальную
температуру отпуска равной 500 °С.
Как видно из рис. 2, применение ультразвуко-
вой техники подачи СОЖ (кривые
3-5) по сравне-
нию с поливом (кривая 1) при одинаковом расходе
подаваемой СОЖ позволило увеличить производи-
тельность шлифования до 2 раз при обработке за-
готовок из стали 40Х и до 3 раз при обработке заго-
товок из стали 95Х18. При этом, очевидно, в те же
разы сократилась и норма расхода СОЖ на одну
обработанную
заготовку – до 2 раз при обработке
заготовок из стали 40Х и до 3 раз при обработке
заготовок из стали 95Х18. Наиболее эффективной
оказалась ультразвуковая техника на основе час-
тотно-модулированного сигнала [8].
Учитывая комплексное влияние техники пода-
чи СОЖ на реализацию и смазочного, и охлажда-
ющего действий, на втором этапе исследований
оценивали вклад каждого из
этих действий в ито-
говый температурный режим обработки. Ввиду не-
возможности изолировать функциональные дей-
ствия в эксперименте, этот этап исследований про-
водили путем выполнения серии из двух числен-
ных расчетов теплового состояния инструмента и
заготовки по методике [2], в одном из которых пола-
гали q
ж
= 0, тем самым искусственно исключая ох-
лаждающее действие СОЖ. Некоторые результаты
этого этапа исследований представлены на диаг-
раммах рис. 3.