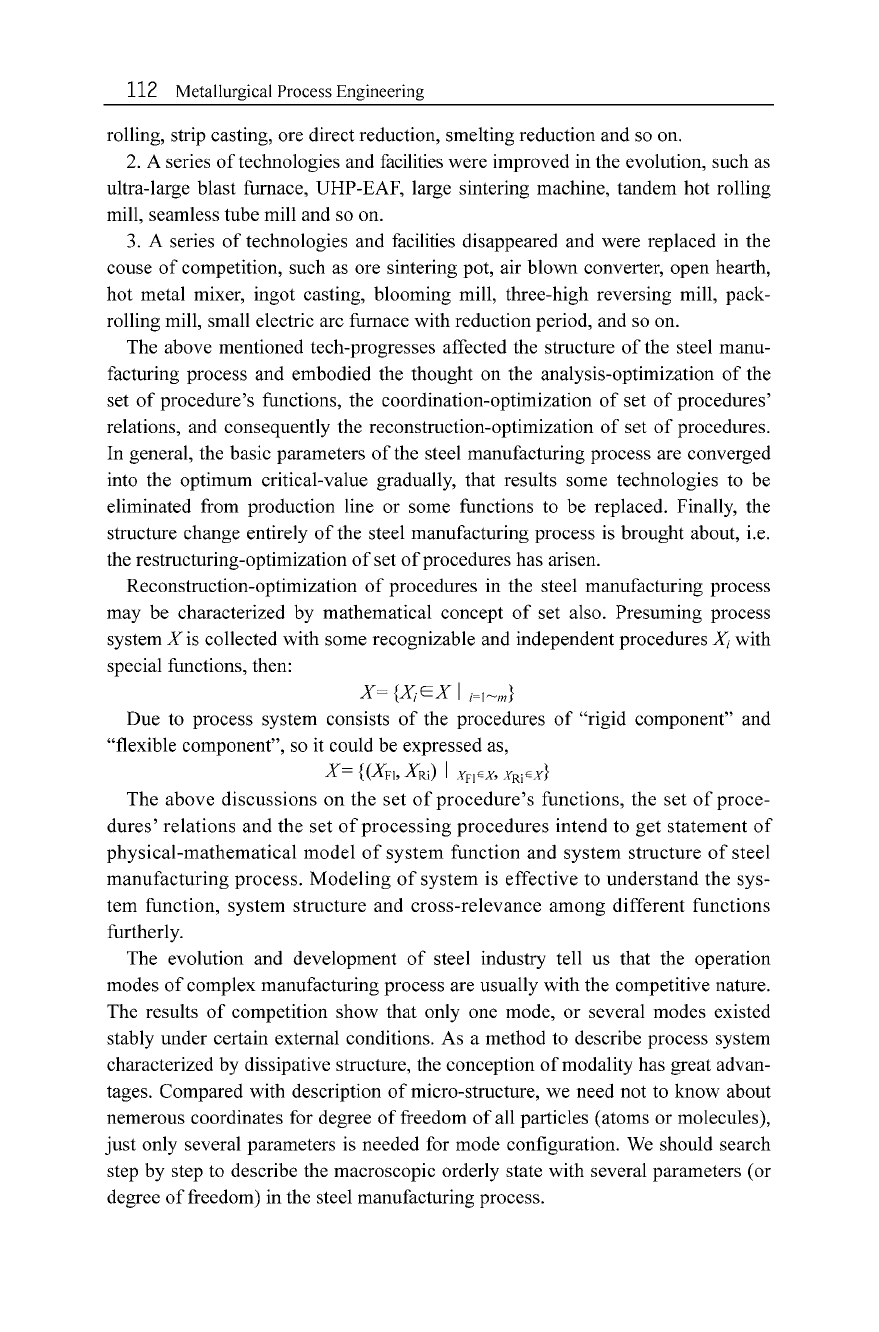
112
Metallurgical Process Engineering
rolIing, strip casting, ore direct reduction, smelting reduction and so on.
2. A series
of
technologies and facilities were improved in the evolution, such as
ultra-large blast furnace, UHP-EAF, large sintering machine, tandem hot rolling
mill, seamless tube mill and so on.
3. A series
of
technologies and facilities disappeared and were replaced in the
couse
of
competition, such as ore sintering pot, air blown converter, open hearth,
hot metal mixer, ingot casting, blooming mill, three-high reversing mill, pack-
rolling mill, small electric arc furnace with reduction period, and so on.
The above mentioned tech-progresses affected the structure
of
the steel manu-
facturing process and embodied the thought on the analysis-optimization
of
the
set
of
procedure's functions, the coordination-optimization
of
set
of
procedures'
relations, and consequently the reconstruction-optimization
of
set
of
procedures.
Ingeneral, the basic parameters
of
the steel manufacturing process are converged
into the optimum critical-value gradualIy, that results some technologies to be
eliminated from production line or some functions to be replaced. FinalIy, the
structure change entirely
of
the steel manufacturing process is brought about, i.e.
the restructuring-optimization
of
set
of
procedures has arisen.
Reconstruction-optimization
of
procedures in the steel manufacturing process
may be characterized by mathematical concept
of
set also. Presuming process
system X is colIected with some recognizable and independent procedures Xi with
special functions, then:
X =
{XjEX
I
i
~
hn
}
Due to process system consists
of
the procedures
of
"rigid component" and
"flexible component", so it could be expressed as,
X =
{(X
Fb
X
Ri
) [
XFlEX, XRiEX }
The above discussions on the set
of
procedure's functions, the set
of
proce-
dures' relations and the set
of
processing procedures intend to get statement
of
physical-mathematical model
of
system function and system structure
of
steel
manufacturing process. Modeling
of
system is effective to understand the sys-
tem function, system structure and cross-relevance among different functions
furtherly.
The evolution and development
of
steel industry telI us that the operation
modes
of
complex manufacturing process are usualIy with the competitive nature.
The results
of
competition show that only one mode, or several modes existed
stably under certain external conditions. As a method to describe process system
characterized by dissipative structure, the conception
of
modality has great advan-
tages. Compared with description
of
micro-structure, we need not to know about
nemerous coordinates for degree
of
freedom
of
alI particles (atoms or molecules),
just only several parameters is needed for mode configuration. We should search
step by step to describe the macroscopic orderly state with several parameters (or
degree
of
freedom) in the steel manufacturing process.