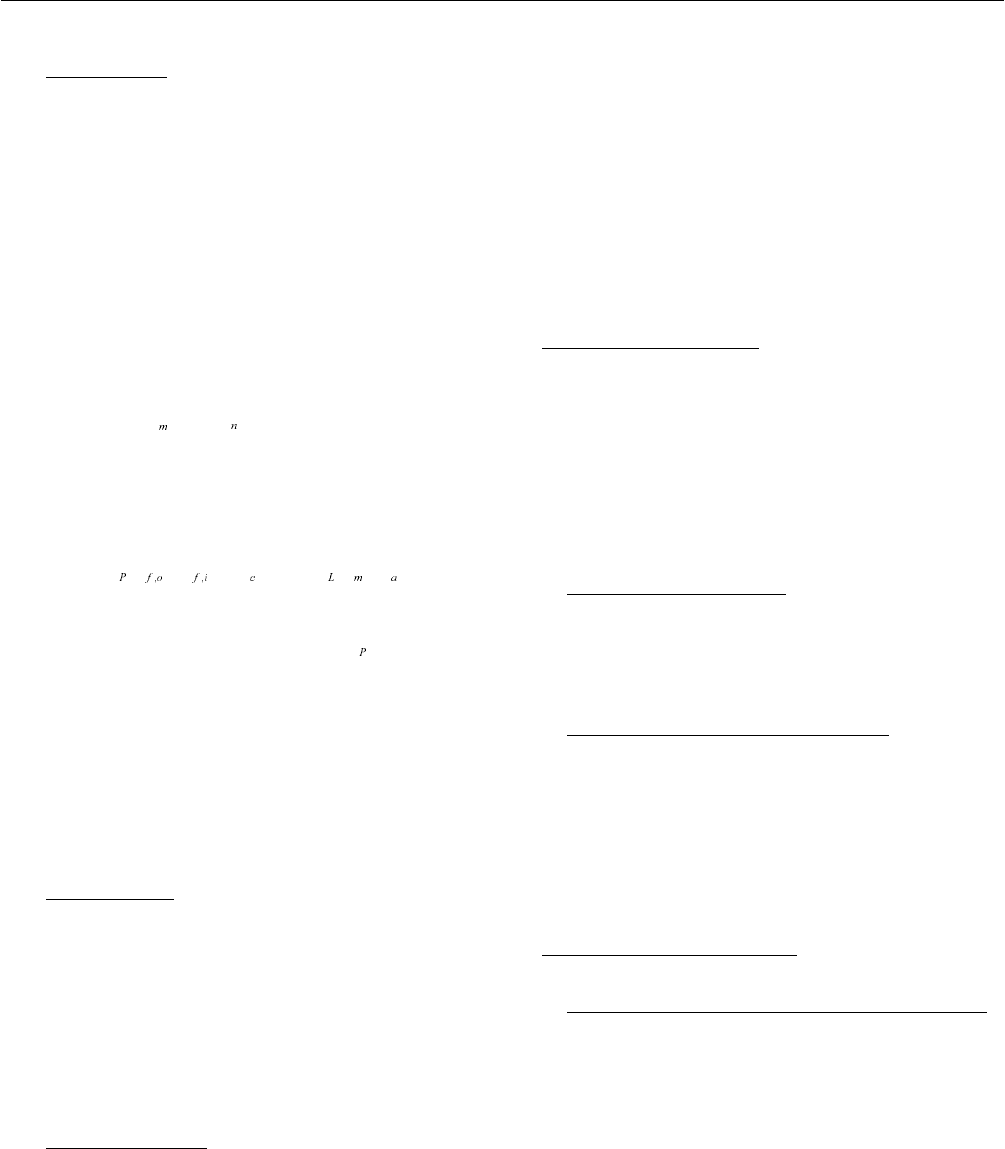
Proceedings of ISES Solar World Congress 2007: Solar Energy and Human Settlement
958
2.2 Solar Collector
There are two solar collectors used in the system. They
were
fabricated at the tilt angel of 45
o
and faced to the south
direction. One solar collector was made up of 18 vacuum
tubes with 58mm in diameter and 1.9m in length. The
distance between two vacuum tubes is 21mm. The overall
area of one collector is 2.5m
3
. At the meantime, there is an
auxiliary electrical heater system with the power of 1500W
in the water tank. The volume of the water tank is 163L.
It can be assumed that the temperature distribution of the
collector and the water tank is linear, and their average
temperature are
T and T , respectively. The thermal
capacity of the collector can be neglected since it is very
small
[6]
. The obtained energy from the solar collectors can
be presented by the following equation,
()'[()]mC T T A F S U T T−= − −
(3)
m
is the flow rate of the water˄kggs
-1
˅, C specific heat
of water, (Jgkg
-1
K
-1
), T
f,o
water outlet temperature from
the solar collector, ( )ć ˈT
f,i
water inlet temperature to the
solar collector, ( ),ć A
c
the solar collector area (m
2
), 'F the
collector efficiency factor,
S absorbed radiation(W/m
2
)ˈ
U
L
overall heat loss coefficient from the solar collector to
environment, (Wm
-2
K
-1
)ˈT
m
average temperature of the
water in the solar collector, T
a
ambient temperature( )ć .
2.3 Heat Exchanger
The heat exchanger is coiled by copper pipe with the
diameter of 16mm. This design is simple and the cost is
very low. The heat provided by the heat exchanger can
compensate for the heat loss from the bioreactor. The
logarithmic mean temperature difference for the heat
exchangeris calculated from the heat exchanger[7].
2.4 The Control System
The purpose of the control system is to keep the bioreactor
temperature constant. When the temperature of the
bioreactor was below the given temperature, the water
pump started to run and the heat can be input into the
bioreactor by the hot water from the solar collectors. The
pump stopped working when the temperature achieved the
given value. If the temperature of the water in the tank can
not reach the needed value, the auxiliary electrical heat
system started to work until the temperature of the tank
reached up to the needed value. The designed temperature
of the sensor can be adjusted ranging from 0 to 80 ,ćć
which can satisfy different digestion temperature for the
bioreactor.
3. EXPERIMENT METHOD
Because the original investment needs to be reduced and
the biogas produced can be enough for daily use for
farmers, an optimum temperature of bioreactor must be
found in the experiments. For this purpose, the experiments
at the temperatures of 15ć, 20ć and 25 ć were carried
out on the abovementioned proposed system.
3.1 The Digestion Temperature
The experiments were carried out at the digestion
temperatures of 15ć, 20ć and 25ć, respectively.
3.2 The Material of Digestion and Inoculant
The material of the digestion was the cattle manure that
came from the cattle farm near the laboratory. By the test,
the TS is16.98%, the VS is78.02% .The inoculant is gained
from swine manure. TS is 10.43% ,VS is 72.22 %.
4. RESULTS AND DISCUSSION
4.1 Measurement of Material Before and after Digestion
Test unit˖250ml, inoculantǃ60g cattle manureˈadd liquid
manure to1000ml˗
Comparision unit˖250ml, inoculant, add liquid manure
to1000ml˗
Digestion temperature:
(20+1)ć, pH is kept at 7.
Table 1 shows the value of TSǃVS before and after the
digestion. It can be seen from Fig. 1 that the concentrations
of TS and VS in anaerobic manure were very low. Based on