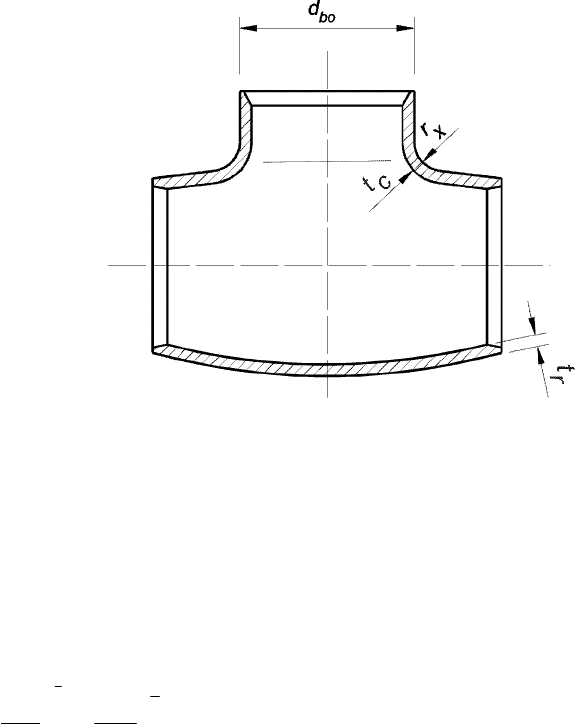
EN 13941:2009 (E)
NOTE 1 Weld-in tees are usually made in dimensions d
h
≤ 600 mm. The formulas for weld-in tees are applicable for
dimensions according to ISO 3419 and EN 10253-2. The stress concentrations i
a1
and i
a2
indicated for resulting stresses,
σ
res
,
make up an upper limit value for i
a1
and i
a2
for membrane stresses
σ
m
.
Figure C.10 — Extruded or forged tee
NOTE 2 The formulas for extruded tees are also applicable for tees made by welding two identically formed halves together.
The stress concentration factors i
a1
and i
a2
indicated for resulting stresses
σ
res
stated for welded tees give an upper limit value for
i
a1
and i
a2
in respect of membrane stresses,
σ
m
, for extruded tees.
NOTE 3 Although FEM analyses show higher values for stress intensification factors for the branch pipe the values proposed
are according to present experience. The lower values here are proposed under consideration, among other things, of the
methodology that all stresses are referred to point B. In special cases (e.g. when the tee only is subject to actions from the branch
giving maximum stresses in point A) the factors might be on the unsafe side. In this case k
a
can be valued at:
8
1
3
2
75,0
⋅
⋅=
rm
bm
r
rm
d
d
t
d
k
For fatigue analyses all stresses are referred to point B, Figure C.8.
σ
and
τ
are calculated separately for run pipe and branch pipe with sectional forces chosen as follows:
For the calculation of stresses in point B, normally the forces and moments determined in the intersection between
the centrelines of the pipes are used. When d
bo
< 0,5 d
ro
, the forces and moments from the branch pipe can be used,
determined at the distance 0,5 d
ro
from the centreline of the run pipe.
Reduced forces and moments are used for calculating the stresses from the forces and moments in the run pipe. If
M
y1
and M
y2
have the same sign as in accordance with Figure C.8, M
y
is equal to the smallest values of M
y1
and M
y2
.
If M
y1
and M
y2
have different signs, M
y
= 0. Reduced values of the other forces and moments in the run pipe are
determined accordingly.
The stresses at point B are calculated as the sum of the stress contribution from internal forces in main pipe and
branch pipe.