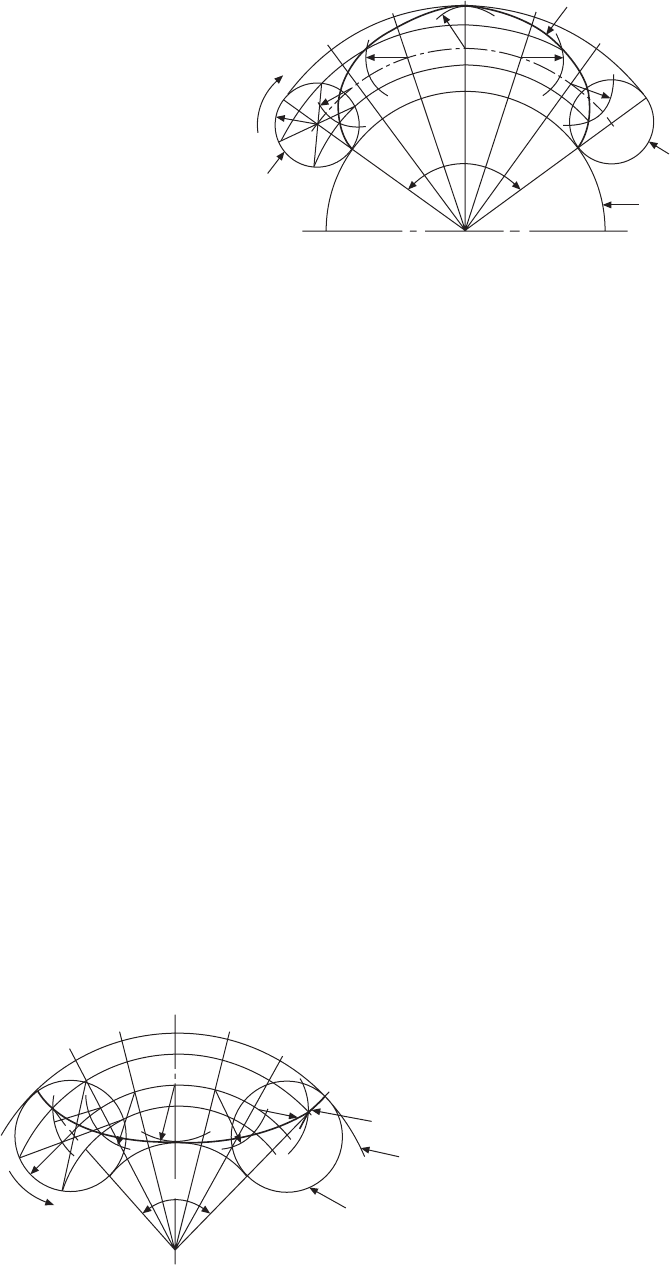
78 Manual of Engineering Drawing
2 Calculate the length of the circumference of the
smaller and the larger circle, and from this
information calculate the angle θ covered by the
rolling circle.
3 Divide the angle θ into the same number of parts
as the rolling circle.
4 Draw the arc which is the locus of the centre of the
rolling circle.
5 The lines forming the angles in step 3 will now
intersect with the arc in step 4 to give six further
positions of the centres of the rolling circle as it
rotates.
6 From the second centre, draw radius R to intersect
with the arc from point 2 on the rolling circle.
Repeat this process for points 3, 4, 5 and 6.
7 Draw a smooth curve through the points of
intersection, to give the required epicycloid.
The hypocycloid
A hypocycloid is defined as the locus of a point on the
circumference of a circle which rolls without slip around
the inside of another circle.
The construction for the hypocycloid (Fig. 10.16)
is very similar to that for the epicycloid, but note that
the rolling circle rotates in the opposite direction for
this construction.
It is often necessary to study the paths taken by
parts of oscillating, reciprocating, or rotating mech-
anisms; from a knowledge of displacement and time,
information regarding velocity and acceleration can
be obtained. It may also be required to study the extreme
movements of linkages, so that safety guards can be
designed to protect machine operators.
Figure 10.17 shows a crank OA, a connecting rod
AB, and a piston B which slides along the horizontal
axis BO. P is any point along the connecting rod. To
plot the locus of point P, a circle of radius OA has
been divided into twelve equal parts. From each position
of the crank, the connecting rod is drawn, distance AP
measured, and the path taken for one revolution lined
in as indicated.
The drawing also shows the piston-displacement
diagram. A convenient vertical scale is drawn for the
crank angle. and in this case clockwise rotation was
assumed to start from the 9 o’clock position. From
each position of the piston, a vertical line is drawn
down to the corresponding crank-angle line, and the
points of intersection are joined to give the piston-
displacement diagram.
The locus of the point P can also be plotted by the
trammel method indicated in Fig. 10.18. Point P
1
can
be marked for any position where B
1
lies on the
horizontal line, provided A
1
also lies on the cir-
cumference of the circle radius OA. This method of
solving some loci problems has the advantage that an
infinite number of points can easily be obtained, and
these are especially useful where a change in direction
in the loci curve takes place.
Figure 10.19 shows a crank OA rotating anti-
clockwise about centre O. A rod BC is connected to
the crank at point A, and this rod slides freely through
a block which is allowed to pivot at point S. The loci
of points B and C are indicated after reproducing the
mechanism in 12 different positions. A trammel method
could also be used here if required.
Part of a shaping-machine mechanism is given in
Fig. 10.20. Crank OB rotates about centre O. A is a
fixed pivot point, and CA slides through the pivoting
block at B. Point C moves in a circular arc of radius
AC, and is connected by link CD, where point D slides
horizontally. In the position shown, angle OBA is 90°,
and if OB now rotates anti-clockwise at constant speed
it will be seen that the forward motion of point D takes
more time than the return motion. A displacement
diagram for point D has been constructed as previously
described.
Fig. 10.15 Epicycloid
Direction of
rotation of
rolling
circle
Initial position
of rolling circle
2
3
1
4
R
R
5
6
R
R
R
R
θ
Epicycloid
Base circle
Final position
of rolling circle
Fig. 10.16 Hypocycloid
θ
Direction of
rotation of
rolling circle
Hypocycloid
Base
circle
Final position
of rolling circle
R
R
R
R
R
R
1
2
3
4
5
6