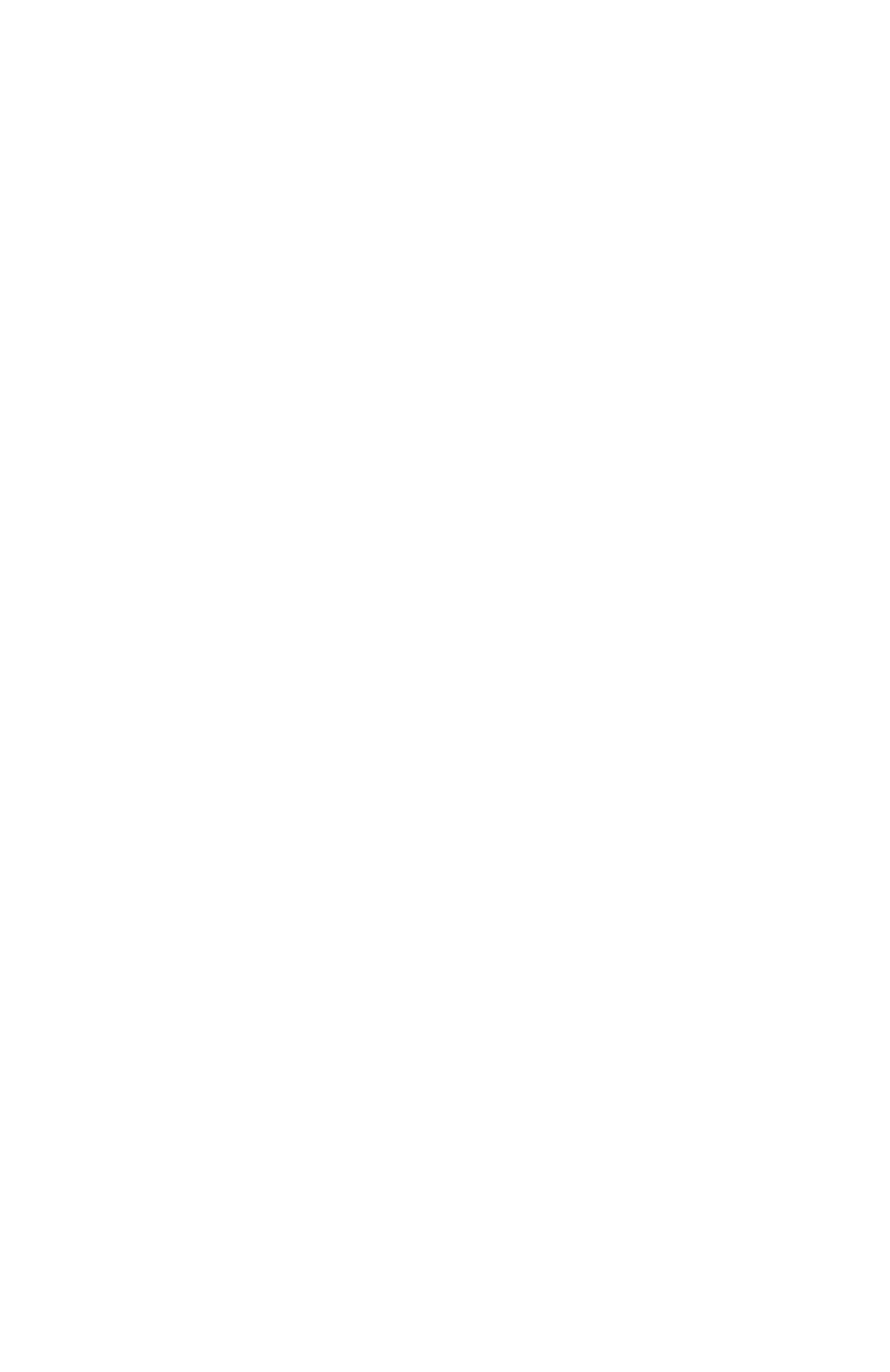
30
14. ТЕХНОЛОГИЧЕСКИЕ ОСОБЕННОСТИ ПРОЕКТИРОВАНИЯ
И ИЗГОТОВЛЕНИЯ ДЕТАЛЕЙ ИЗ КОМПОЗИЦИОННЫХ
МАТЕРИАЛОВ
Конструктивные особенности деталей из композиционных материалов обу-
словлены физико-механическим и технологическими свойствами, способами их
получения. Прочностные и точностные характеристики деталей во многом зави-
сят от их конструктивного оформления. Следует всегда стремиться к упрощению
конструкции детали как по технологическим и эксплуатационным, так и по эко-
номическим соображениям. Чем проще конструкция детали, тем дешевле техно-
логическая оснастка, ниже себестоимость, выше производительность труда и ка-
чество получаемых деталей. Габаритные размеры деталей определяют мощность
оборудования (пресса, литьевой машины и т. д.). При проектировании деталей с
высокими требованиями к точности размеров необходимо предусмотреть при-
пуск на их дальнейшую механическую обработку.
В конструкциях деталей следует избегать выступов, пазов и отверстий, распо-
ложенных перпендикулярно к оси прессования (рис. 14.1, а) [1]. Их следует за-
менять соответствующими элементами, расположенными в направлении прессо-
вания. Процесс формообразования деталей из композиционных материалов со-
провождается значительной усадкой, поэтому в их конструкциях нельзя допус-
кать значительной разностенности, которая вызывает коробление и образова-
ние трещин (рис. 14.1, б-г). Разностенность не должна превышать 1:3. В зависи-
мости от габаритных размеров детали, используемого материала и других факто-
ров оптимальной толщиной стенок считается 0,5...5 мм, а минимальными ра-
диусами сопряжений – 0,5...2 мм.
Отверстия в деталях получают при формообразовании (литьем, прессованием
и т.д.) соответствующими стержнями, устанавливаемыми в технологической ос-
настке (пресс-формах). Наличие стержней вызывает появление напряжений в де-
талях, так как они затрудняют свободную усадку материала. Отверстия лучше
располагать не в сплошных массивах, а в специальных бобышках с тонкими
стенками (рис. 14.1, г, е), что снижает усадку и силу обхвата стержней.
В деталях из композиций на основе пластмасс литьем под давлением и прес-
сованием получают наружные и внутренние резьбы, не требующие дальнейшей
обработки. Минимальный допустимый диаметр резьбы для деталей из термопла-
стов и пресс-порош ков равен 2,5 мм, для волокнистых материалов – 4 мм. Резь-
бу на деталях из спеченных порошковых материалов получают обработкой реза-
нием.
В конструкциях деталей необходимо предусматривать ребра жесткости, кото-
рые позволяют уменьшить сечения отдельных элементов детали, снизить на-
пряжения в местах сопряжения стенок различного сечения, повысить устойчи-
вость и прочность конструкций (рис. 14.1, б). Толщина ребер жесткости у их ос-
нования должна быть равной толщине основной стенки детали. Для малогаба-
ритных деталей роль ребер жесткости могут выполнять выступы или впадины