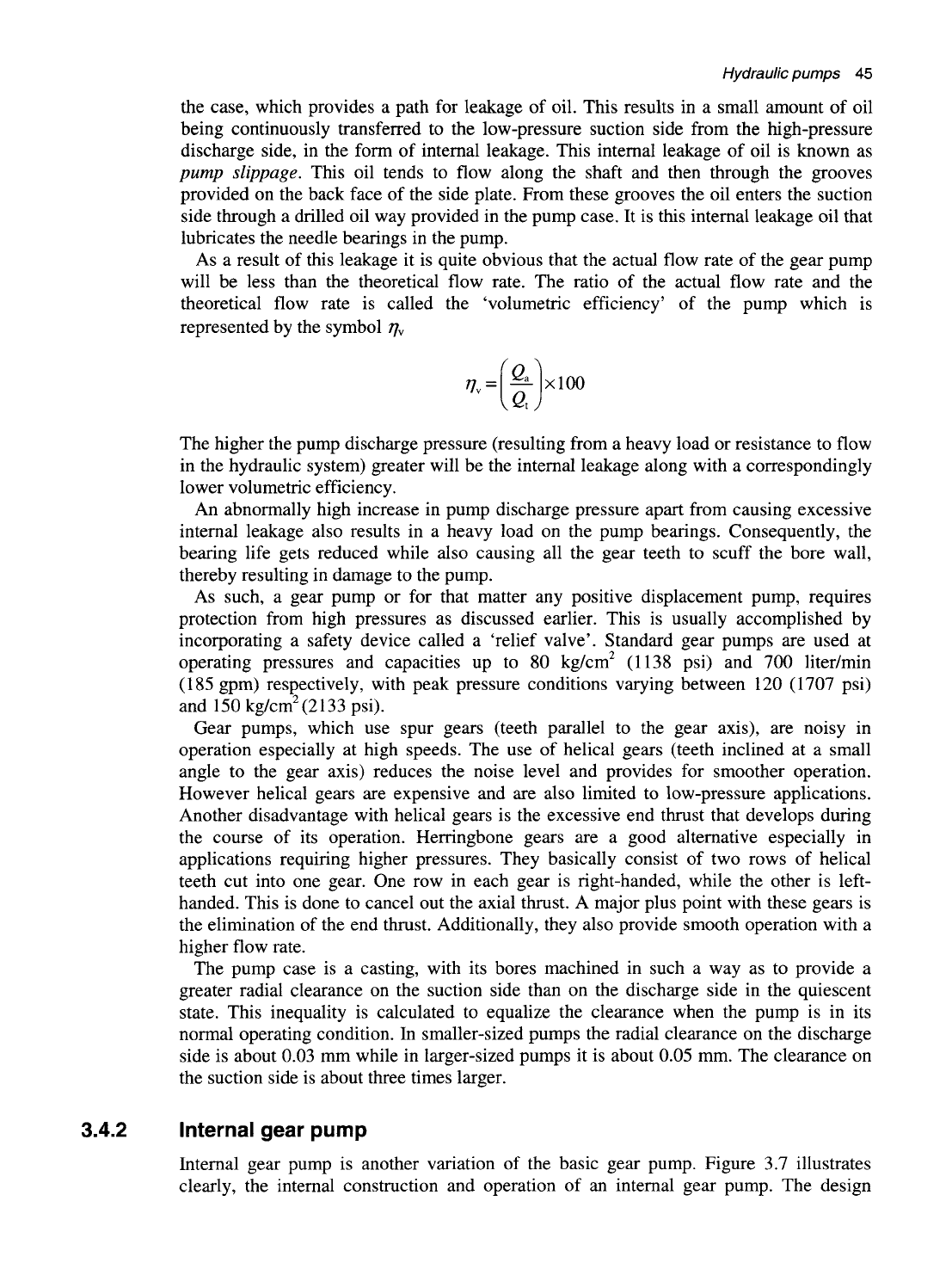
Hydraulic pumps
45
the case, which provides a path for leakage of oil. This results in a small amount of oil
being continuously transferred to the low-pressure suction side from the high-pressure
discharge side, in the form of internal leakage. This internal leakage of oil is known as
pump slippage. This oil tends to flow along the shaft and then through the grooves
provided on the back face of the side plate. From these grooves the oil enters the suction
side through a drilled oil way provided in the pump case. It is this internal leakage oil that
lubricates the needle bearings in the pump.
As a result of this leakage it is quite obvious that the actual flow rate of the gear pump
will be less than the theoretical flow rate. The ratio of the actual flow rate and the
theoretical flow rate is called the 'volumetric efficiency' of the pump which is
represented by the symbol //v
^v =
^a^
a
xlOO
The higher the pump discharge pressure (resulting from a heavy load or resistance to flow
in the hydraulic system) greater will be the internal leakage along with a correspondingly
lower volumetric efficiency.
An abnormally high increase in pump discharge pressure apart from causing excessive
internal leakage also results in a heavy load on the pump bearings. Consequently, the
bearing life gets reduced while also causing all the gear teeth to scuff the bore wall,
thereby resulting in damage to the pump.
As such, a gear pump or for that matter any positive displacement pump, requires
protection from high pressures as discussed earlier. This is usually accomplished by
incorporating a safety device called a 'relief valve'. Standard gear pumps are used at
operating pressures and capacities up to 80 kg/cm^ (1138 psi) and 700 liter/min
(185 gpm) respectively, with peak pressure conditions varying between 120 (1707 psi)
andl50kg/cm^2133psi).
Gear pumps, which use spur gears (teeth parallel to the gear axis), are noisy in
operation especially at high speeds. The use of helical gears (teeth inclined at a small
angle to the gear axis) reduces the noise level and provides for smoother operation.
However helical gears are expensive and are also limited to low-pressure applications.
Another disadvantage with helical gears is the excessive end thrust that develops during
the course of its operation. Herringbone gears are a good alternative especially in
applications requiring higher pressures. They basically consist of two rows of helical
teeth cut into one gear. One row in each gear is right-handed, while the other is left-
handed. This is done to cancel out the axial thrust. A major plus point with these gears is
the elimination of the end thrust. Additionally, they also provide smooth operation with a
higher flow rate.
The pump case is a casting, with its bores machined in such a way as to provide a
greater radial clearance on the suction side than on the discharge side in the quiescent
state.
This inequality is calculated to equalize the clearance when the pump is in its
normal operating condition. In smaller-sized pumps the radial clearance on the discharge
side is about 0.03 mm while in larger-sized pumps it is about 0.05 mm. The clearance on
the suction side is about three times larger.
3.4.2 Internal gear pump
Internal gear pump is another variation of the basic gear pump. Figure 3.7 illustrates
clearly, the internal construction and operation of an internal gear pump. The design