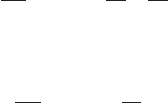
13 PUMP TESTING 13.35
this type of gage is used and the connecting lines are completely filled with water, the cor-
rect equation is
In addition to the differential gage, a separate suction gage can be used, as shown in
Figures 22 and 25. The equation in this case is
MEASURING HEAD WITH BOURDON GAGES An example of a centrifugal pump arrangement that
uses calibrated bourdon gages for head measurement is shown in Example 3 of Figure 27,
with the gage pressure above atmospheric pressure. The distances Z
s
and Z
d
are measured
to the center of the gage and are negative if the center of the gage lies below the datum line.
MEASURING HEAD ON VERTICAL SUCTION PUMPS IN SUMPS AND CHANNELS
In vertical-shaft
pumps drawing water from large open sumps and having inlet passages whose length
does not exceed about three inlet opening diameters, such inlet pieces having been fur-
nished as part of the pump, the total head should be the reading of the discharge con-
nection in feet (meters) plus the vertical distance from the gage centerline to the free
water level in the sump in feet (meters) (Example 2 of Figure 27).
Power Measurement The pump input power may be determined with a calibrated
motor, a transmission dynamometer, or a torsion dynamometer. The Hydraulic Institute
ANSI/HI 2000 Edition Pump Standards (Reference 13) are generally used as the basis for
most power measurement procedures.
CALIBRATED MOTORS
When pump input power is to be determined with a calibrated motor,
the power input should be measured at the terminals of the motor to exclude any line
losses that may occur between the switchboard and the driver. Certified calibration curves
of the motor must be obtained. The calibration should be conducted on the motor in ques-
tion and not on a similar machine. Such calibrations must indicate the true input-output
value of motor efficiency and not some conventional method of determining an arbitrary
efficiency. Calibrated laboratory-type electric meters and transformers should be used to
measure power input to all motors.
TRANSMISSION DYNAMOMETERS The transmission, or torque-reaction, dynamometer con-
sists of a cradled electric motor with its frame and field windings on one set of bearings
and the rotating element on another set, so the frame is free to rotate but is restrained
by means of some weighting or measuring device.
When pump input power is to be determined with a transmission dynamometer, the
unloaded and unlocked dynamometer must be properly balanced prior to the test at the
same speed at which the test is to be run.The balance should be checked against standard
weights. After the test the balance must be rechecked to assure that no change has taken
place. In the event of an appreciable change, the test should be rerun. An accurate mea-
surement of speed is essential and should not vary from the pump rated speed by more
than 1%. Power input is calculated as shown later in this section under “Computations.”
TORSION DYNAMOMETERS The torsion dynamometer consists of a length of shafting whose
torsional strain when rotating at a given speed and delivering a given torque is measured
by some standard method. When pump input power is to be determined with a torsion
dynamometer, the unloaded dynamometer should be statically calibrated prior to the test.
This is done by measuring the angular deflection for a given torque.
Immediately before and after the test, the torsion dynamometer must be calibrated
dynamically at the rated speed. The best and simplest method to accomplish this is to use
the actual job driver to supply power and use a suitable method of loading the driver over
the entire range of the pump to obtain the necessary calibrations. The calibration of the
h
s
W
m
W
h
gs
Z
V
s
2
2g
H a
W
m
W
1bh
g
V
d
2
2g
V
s
2
2g