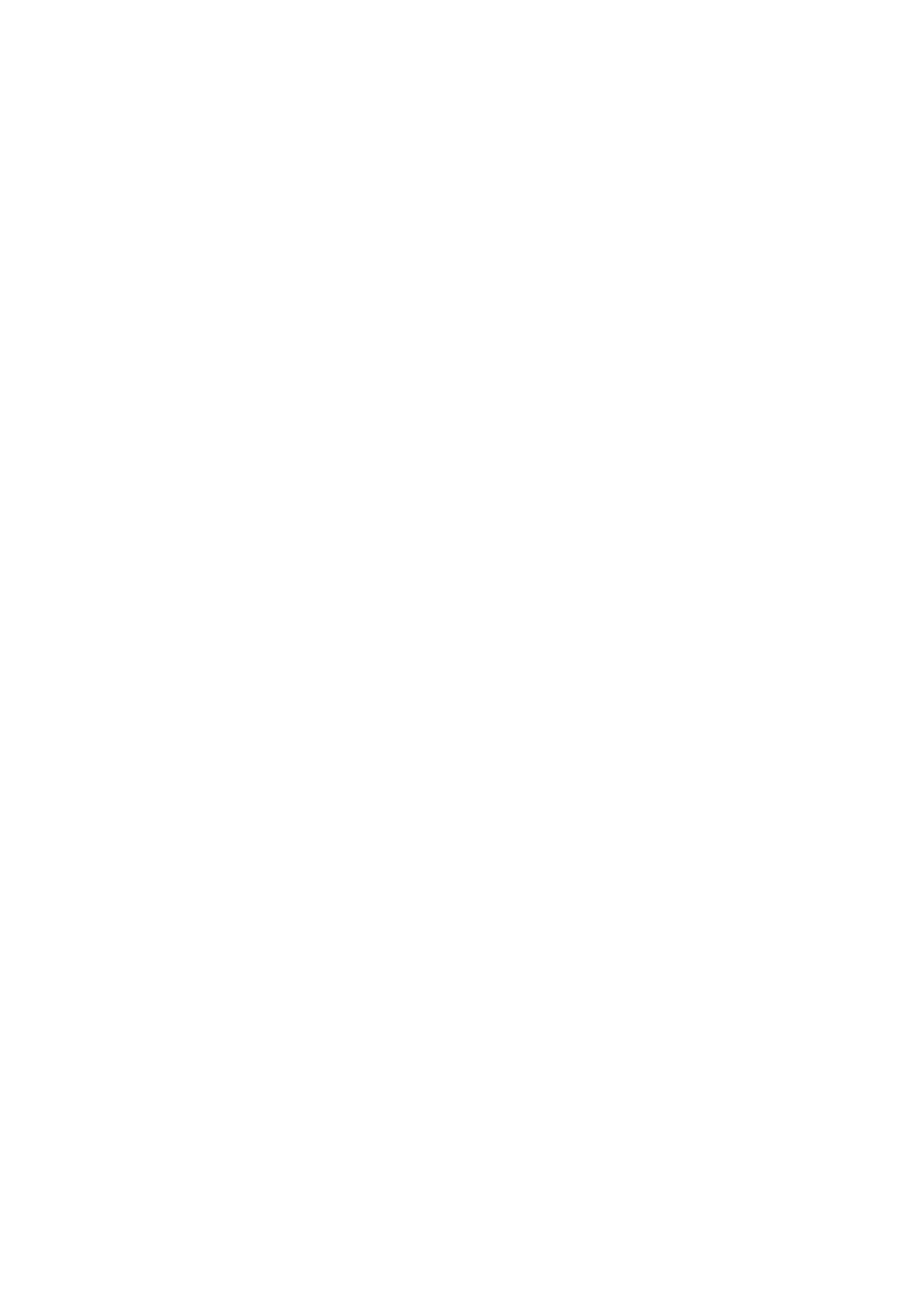
242
Для уравновешивания детали следует приложить на радиусе г
2
два равных
груза весом Q в осевой плоскости детали, где сосредоточены неуравновешен-
ные массы, на расстоянии 1
2
, чтобы они создали уравновешивающий момент.
Динамическая балансировка производится всегда при вращении детали,
установленной на гибких опорах. Центробежные силы, вызванные вращением
неуравновешенной детали, создают колебательные движения гибких опор. С
помощью специальных устройств колебания уравновешиваются и определяют-
ся значения и направление дисбаланса.
На рис. 5.6, б приведена схема установки для динамической балансировки.
Балансируемая деталь 3 устанавливается на опоры 1 через плоские пружины 2.
Колебания пружин, вызванные дисбалансом, посредством тяг 4 передаются на
индуктивные преобразователи 5 перемещения, возбуждая в цепи ток с напря-
жением, пропорциональным амплитуде колебаний. Ток вызывает отклонения
стрелки ваттметра 6, градуированного в единицах дисбаланса.
Другая обмотка ваттметра 6 получает ток от генератора 7, ротор которого
вращается синхронно с балансируемой деталью. Статор генератора можно по-
ворачивать с помощью рукоятки 8 во время вращения детали, при этом поло-
жение дисбаланса может быть определено на лимбе (на схеме не показан) по
углу поворота обмотки статора при максимальном отклонении стрелки ватт-
метра. Продолжительность балансировки на этой машине составляет 1. . .2 мин.
Современные устройства для динамической балансировки в значительной
степени автоматизированы; в частности, по шкалам приборов можно опреде-
лить глубину сверления определенного диаметра, массу неуравновешенного
груза, размеры противовесов и др., а также места крепления грузов или места
удаления лишнего металла.
Для взаимного уравновешивания сил инерции деталей машин, движущихся
прямолинейно-возвратно, и для создания равенства масс этих деталей в узлах
машины применяют подгонку масс. Наиболее характерными деталями, тре-
бующими подгонки, являются поршни, шатуны, штоки и др. Так, колебания в
массе поршней вызывают неуравновешенность двигателей; эти колебания чаще
всего создают необработанные внутренние поверхности поршней.
Подгонку по массе обычно производят растачиванием внутреннего пояска
юбки поршня, а у облегченных конструкций поршней – удалением металла с
нижней плоскости и приливов у бобышек под палец, а также растачиванием
специального прилива на внутренней стороне юбки поршня, ниже бобышек под
палец.
Подгонку по массе осуществляют на специальных станках. В современном
машиностроении применяют станки для подгонки по массе с автоматическим
передвижением ползуна (груза) по коромыслу весов посредством электронной
системы. Применение станка для подгонки по массе обеспечивает отклонения
деталей по массе в пределах ±2 г.