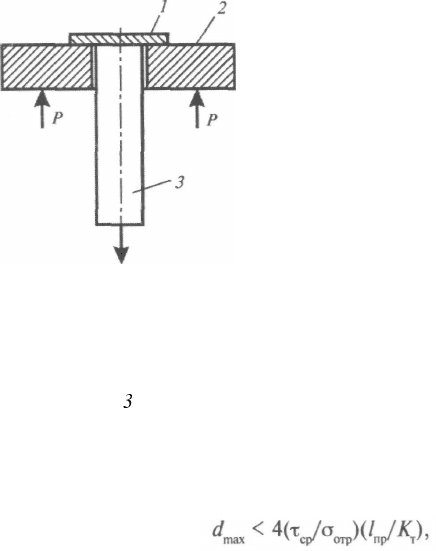
68
И. М. Ковенский, В. В. Поветкин Металловедение покрытий
возникают нормальные, касательные или эквивалентные (когда
усилие отрыва направлено под некоторым углом к переходной зоне)
напряжения. Поэтому количественные методы определения проч¬
ности сцепления покрытий с основой подразделяются на методы
отрыва, сдвига и отслаивания.
Метод отрыва
Один из наиболее простых методов заключается в осаждении
металла на торцевую часть цилиндрического образца. Испытания
проводят путем отрыва металлического цилиндра от покрытия на
разрывной машине (рис. 2.13). Однако данный метод находит огра¬
ниченное применение, главным образом из-за необходимости осаж¬
дения покрытий большой толщины, а также некоторых методи¬
ческих трудностей подготовки образца к испытаниям.
Значительно более прогрессивным
при проведении испытаний методом
отрыва является использование кони¬
ческих штифтов. Конические штифты
применяются достаточно давно, одна¬
ко в последние годы методика прове¬
дения испытаний значительно усовер¬
шенствована. Основные рекомендации,
позволяющие значительно повысить
точность определения прочности сцеп¬
ления покрытия с основой, сводятся к
следующему.
Для определения прочности сцеп¬
ления гальванических покрытий с ос¬
новой из чугуна или стали необходимо
применять штифты с углом конуса не
менее 16—18°, а для материалов, склон¬
ных к схватыванию, 22—26°. При этом
угол конуса штифта должен быть на 0,5
—1,0° меньше угла конуса отверстия.
Диаметр торца штифта выбирается из условия, исключающего срез
покрытия и обеспечивающего отрыв, по формуле:
Рис. 2.13. Схема определения
прочности сцепления мето¬
дом отрыва металлическо¬
го цилиндра:
1 — покрытие; 2 — сталь¬
ная пластина;
— стальной
цилиндр
Глава 2. Методы изучения строения и свойств покрытий
69
где τ
ср
— тангенциальные напряжения при срезе покрытия; о —
нормальные напряжения при отрыве; l
пр
— предельная толщина
покрытия, зависящая от свойств осаждаемого материала и усло¬
вий электролиза; К
т
— коэффициент, учитывающий уменьшение
максимально допускаемого диаметра торца штифта в зависимости
от характеристик покрытий (для хрупких K
т
= 1,05 — 1,10, для пла¬
стичных - K
т
= 1,10 - 1,15).
Если адгезионные связи превышают когезионные, то разру¬
шение происходит по основному материалу или по материалу по¬
крытия или имеет смешанный характер. Для получения «чистого»
отрыва необходимо принять минимально допустимый диаметр торца
штифта, который, однако, ограничен как свойствами материала
основы, так и погрешностями измерения. Практически диаметр
торца штифтов выбирают равным 1,6—3,0 мм, а точность измере¬
ния прочности сцепления покрытий с основой повышают за счет
применения многоштифтовых приспособлений.
Одно из таких приспособлений конструкции И. Ф. Плеханова
приведено на рис. 2.14. Применение многоштифтового приспособ¬
ления по сравнению с цилиндрическими стержневыми образцами
исключает влияние на адгезионную прочность краевого эффекта и
неравномерности распределения плотности тока по поверхности
электрода.
При подготовке образцов к сборке приспособления необхо¬
димо соблюдать некоторые требования:
штифты и диск изготавливаются из того же материала
и с такой же структурой, что и деталь, прочность сцепления по¬
крытия с которой нужно определить;
с учетом точности размеров и шероховатости поверх¬
ностей (R
z
40—R
a
2,5) соединения допускается изготовление конус¬
ных штифтов на станках токарной группы и выполнение конусных
отверстий с последующей обработкой конусной разверткой;
перед сборкой сопряжений на конусные поверхности
отверстий и штифтов наносится слой мелкодисперсных (0,2—
2,0 мкм) частиц оксида алюминия или графита;
после сборки поверхность диска со штифтами, на ко¬
торую наносится покрытие, шлифуется; поскольку при шлифова¬
нии диаметр торца штифтов и внутренний диаметр отверстий в
диске увеличиваются, при их изготовлении необходимо преду¬
смотреть припуски на шлифование;