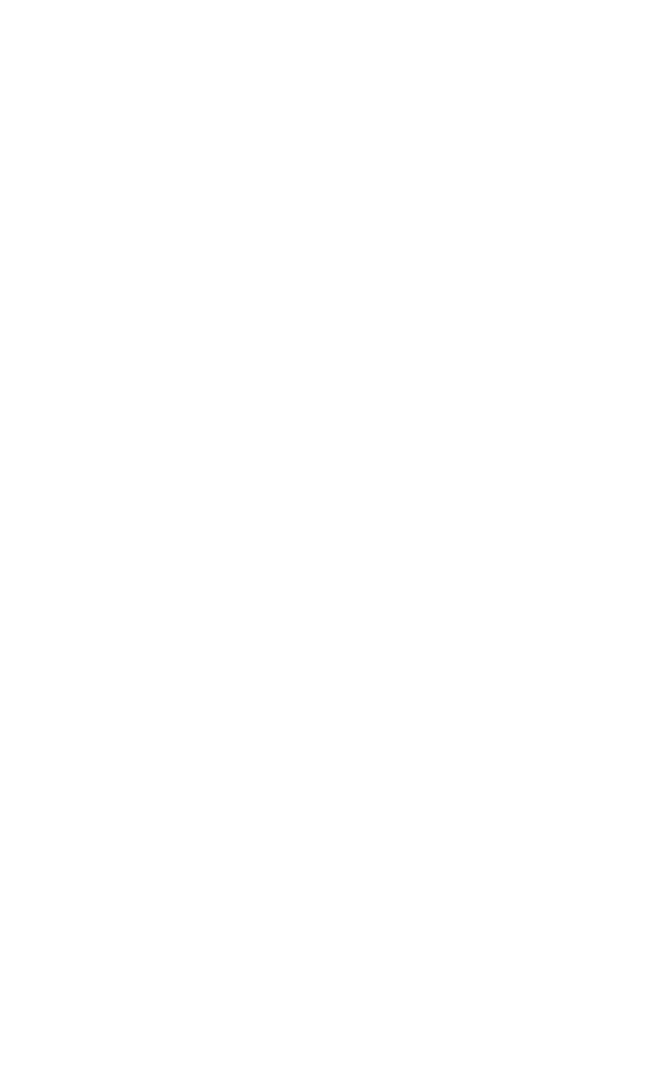
The same situation can be produced by a thrust bearing where angular deflection
is combined with lateral deflection.
18
If contact occurs on the same side of the disc as
the virtual pivot point of the deflected disc, then backward whirl will result. Con-
versely, if contact occurs on the side of the disc opposite to the side where the virtual
pivot point of the disc is located, then forward whirl will result.
It has been suggested (but not concluded)
19
that the whirling frequency is gener-
ally less than the critical speed.
The vibration is subject to various types of control. If contact between rotor and
stator can be avoided or the contact area can be kept well lubricated, no whipping
will occur. Where contact must be accommodated, and lubrication is not feasible,
whipping may be avoided by providing abradability of the rotor or stator element to
allow disengagement before whirl. When dry friction is considered in the context of
the dynamics of the stator system in combination with that of the rotor system,
20
it is
found that whirl can be inhibited if the independent natural frequencies of the rotor
and stator are kept dissimilar, that is, a very stiff rotor should be designed with a very
soft mounted stator element that may be subject to rubs. No first-order interde-
pendence of whirl speed with rotational speed has been established.
FLUID BEARING WHIP
As described in experimental and analytic literature,
21
and in standard texts (e.g.,
Ref. 22), fluid bearing whip can be understood by referring to Fig. 5.7. Consider
some nominal radial deflection of a shaft rotating in a fluid (gas- or liquid-) filled
clearance. The entrained, viscous fluid will circulate with an average velocity of
about half the shaft’s surface speed.The bearing pressures developed in the fluid will
not be symmetric about the radial deflection line. Because of viscous losses of the
bearing fluid circulating through the close clearance, the pressure on the upstream
side of the close clearance will be higher than that on the downstream side. Thus, the
resultant bearing force will include a tangential force component in the direction of
rotation which tends to induce forward whirl in the rotor. The tendency to instabil-
ity is evident when this tangential force exceeds inherent stabilizing damping forces.
When this happens, any induced whirl results in increased centrifugal forces; this, in
turn, closes the clearance further and results in ever-increasing destabilizing tangen-
tial force. Detailed reviews of the phenomenon are available in Refs. 23 and 24.
These and other investigators have shown that to be unstable, shafting must
rotate at an rpm equal to or greater than approximately twice the critical speed, so
that one would expect the ratio of frequency to rpm to be equal to less than approx-
imately 0.5.
The most obvious measure for avoiding fluid bearing whip is to restrict rotor
maximum rpm to less than twice its lowest critical speed. Detailed geometric varia-
tions in the bearing runner design, such as grooving and tilt-pad configurations, have
also been found effective in inhibiting instability. In extreme cases, use of rolling
contact bearings instead of fluid film bearings may be advisable.
Various investigators (e.g., Ref. 25) have noted that fluid seals as well as fluid
bearings are subject to this type of instability.
SEAL AND BLADE-TIP-CLEARANCE EFFECT IN TURBOMACHINERY
Axial-flow turbomachinery may be subject to an additional whirl-inducing effect
by virtue of the influence of tip clearance on turbopump or compressor or turbine
5.12 CHAPTER FIVE
8434_Harris_05_b.qxd 09/20/2001 11:28 AM Page 5.12