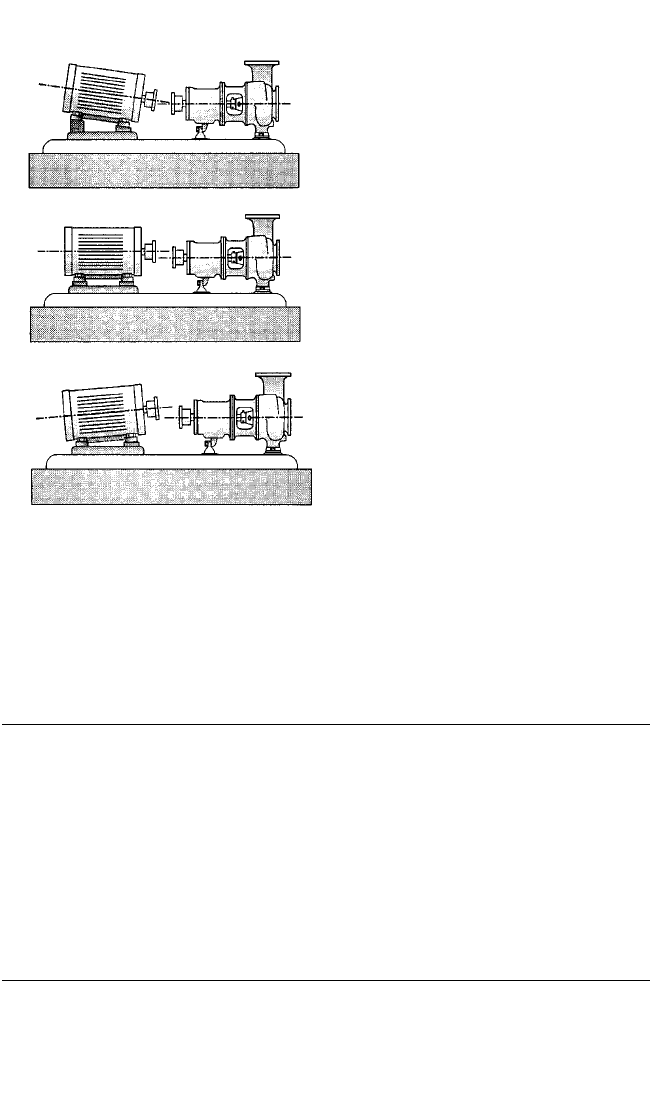
16, which includes discussions of the
parameter to be measured (displace-
ment, velocity, or acceleration), suitable
vibration pickups to be mounted on the
rotating machinery, suitable locations
for the transducers, the selection of an
appropriate spectrum analyzer, deter-
mination of appropriate analyzer band-
width for fault detection in rotating
machinery, and spectrum interpretation
and fault diagnosis. For example, the
Trouble-Shooting Chart of Table 16.1
indicates that the dominant frequency
in the spectrum of misaligned rotating
machinery is often 1 or 2 times the rpm,
and sometimes 3 or 4 times the rpm.
Chapter 16 also points out that in inter-
preting a vibration spectrum, it is often
difficult to separate faults caused by
misalignment, unbalance, bent shaft,
eccentricity, and cracks in a rotating
shaft; this is because these various
faults may be mechanically related. The
results of vibration spectrum analysis
of misaligned rotating machinery show,
for example, that the spectra are differ-
ent for (1) different types of couplings
and (2) different types of bearings
which support the machinery shafts.
TOLERANCE GUIDE FOR FLEXIBLY COUPLED
ROTATING MACHINERY
Whether a measured value of shaft misalignment in flexibly coupled machinery is
acceptable or not depends not only on the magnitude of the misalignment but on the
rotational speed of the shaft, among other factors. A rough guide as to how much
misalignment is acceptable is given in Fig. 39.23. This illustration may be used to
determine, approximately, whether or not shaft realignment is required under most
circumstances. The vertical axis represents the amount of misalignment relative to
the distance between points of power transmission (left scale); this value may also be
expressed as the angle φ (see Fig. 39.21C), which is shown on the right vertical axis.
BASIC STEPS IN SHAFT ALIGNMENT
Before starting the shaft alignment, obtain relevant information on the equipment
being aligned, ensure that all possible safety precautions have been taken, perform
preliminary checks such as inspecting the coupling (between the driver shaft and the
driven shaft) for damage or worn components, find and correct any problems with
the foundation or baseplate, perform bearing clearance or looseness checks, meas-
SHAFT MISALIGNMENT OF ROTATING MACHINERY 39.39
FIGURE 39.22 Types of shaft misalignment:
(A) angular misalignment, (B) parallel misalign-
ment, and (C) the most common combination of
parallel and angular misalignment.
(A)
(B)
(C)
8434_Harris_39_b.qxd 09/20/2001 12:24 PM Page 39.39