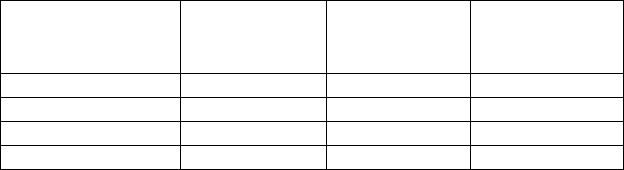
Characterization of Asphalt Materials for Moisture Damage 241
was selected through trials in the range of 25 to 45 for asphalt imaging. When the
drive amplitude was too large, the cantilever made an intermittent contact with the
surface.
2.1 Tip Functionalization and Calibration
Silicon nitride tips are purchased from VEECO Instruments, Inc (Veeco Instru-
ment Inc., 2007). This tip is a beam bounce cantilever (called RFESPA-CP
MPP211) with a length of 125 μm, natural frequency of 90 kHz, and spring con-
stant of 3 N/m. AFM tips were functionalized using carboxyl (-COOH), methyl
(-CH3), ammin (-NH3) and hydroxyl (-OH) groups from the help of Novascan
Technologies, Ames, IA. These functionals are known to be the major part of as-
phalt chemistry (Testa, 1995). The functionalized AFM test requires calibration of
tips. As discussed previously the force in AFM is calculated for a specific tip, the
tip constant is determined through calibration. Special module to calibrate the
AFM tips supplied by Veeco was used in this study. In calibration procedure, the
tip distances are measured on a sample on a sample of known force between the
tip and the sample molecules. Tip constant is calculated from known force and
displacement (k =F/δ). This constant is used for converting displacement data of
other samples to force; thereby producing force distance (F-D) curve.
2.2 Asphalt Sample Surface Imaging
This paper describes the results of AFM testing on two types of PG grade asphalt
binders under wet and dry conditions. Noncontact mode AFM with Proscan soft-
ware was used to conduct the AFM testing and to analyze the images. In AFM
testing, sample image is produced as a first step. Figure 2 shows the 3D images of
dry and wet PG 70-22 binder samples. It can be seen that wet sample has more
spikes than the dry samples. These images were analyzed using WSXM software
(Horacos et al. 2007). In image analysis, asphalt film roughness is measured using
quantities such as average, maximum and root mean square (RMS) values of sur-
face roughness. These quantities are listed in Table 2. It can be seen that PG 76-28
(Dry) sample shows the lowest RMS value (0.56 nm) and the all other RMS val-
ues are fairly close. In general, the RMS roughness values of the wet samples are
higher than those of dry samples.
Table 2 Height and Roughness values of all samples
Sample
Maximum
height (nm)
Average
height (nm)
RMS
Roughness
(nm)
PG 70-22 (dry) 27.96 9.40 2.97
PG 70-22 (wet) 4.59 2.51 0.56
PG 76-28 (dry) 17.73 13.47 0.94
PG 76-28 (wet) 23.21 8.51 2.43