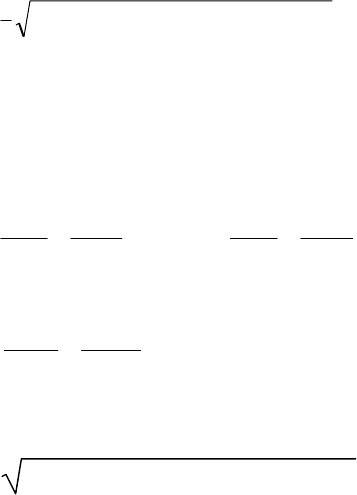
NOTE 1: Each set of design stress resultants for stored solid loading of a silo should be based on a
single set of stored solid properties.
NOTE 2: Where the design stress resultants are being evaluated to verify adequate resistance to the
plastic limit state, in general the stored solid properties should be chosen to maximise the internal
pressure and the condition of discharge with patch loads in EN 1991-4 should be chosen.
NOTE 3: Where the design stress resultants are being evaluated to verify adequate resistance to the
buckling limit state under stored solid loads, in general the stored material properties should be chosen
to maximise the axial compression and the condition of discharge with patch loads in EN 1991-4
should be chosen. However, where the internal pressure is beneficial in increasing the buckling
resistance, only the filling pressures (for a consistent set of material properties) should be adopted in
conjunction with the discharge axial forces, since the beneficial pressures may fall to the filling values
locally even though the axial compression derives from the discharge condition.
(2) Where membrane theory is used to evaluate design stresses in the shell wall, the resistance of
the shell should be adequate to withstand the highest pressure at every point.
(3) Because highly localised pressures are found to induce smaller design membrane stress
resultants than would be found using membrane theory, the provisions of EN 1993-1-6 for stress
design, direct design or computer design may be used to achieve a more economical design solution.
(4) Where a membrane theory analysis is used, the resulting two dimensional stress field of stress
resultants n
x,Ed
, n
θ,Ed
and n
xθ,Ed
may be evaluated using the equivalent design stress:
2
EdxθθEdθ,Edx,
2
Edθ,
2
Edx,Ede,
3
1
nnnnn
+−+=
σ
... (5.1)
(5) Where an elastic bending theory analysis (LA) is used, the resulting two dimensional stress
field of primary stress resultants n
x,Ed
, n
θ,Ed
, n
xθ,Ed
, m
x,Ed
, m
θ,Ed
, m
xθ,Ed
may be transformed into
the fictitious stress components:
, , , ,
, ,
2 2
x Ed x Ed Ed Ed
x Ed Ed
n m n m
θ θ
θ
σ σ
= ± = ± ... (5.2)
, ,
,
2
x Ed x Ed
x Ed
n m
θ θ
θ
τ
= ± ... (5.3)
and the von Mises equivalent design stress:
σ
e,Ed
=
σ
x
2
.Ed
+
σ
θ
2
.Ed
−
σ
x.Ed
σ
θ
.Ed
+ 3
τ
x
2
θ
.Ed
... (5.4)
NOTE: The above expressions (Ilyushin yield criterion) give a simplified conservative equivalent
stress for design purposes.
5.3.2.3 Plastic limit state
(1) The design resistance in plates in terms of membrane stress resultants should be assessed as the
equi
valent stress resistance for both welded and bolted construction f
e,Rd
given by:
f
e,Rd
= f
y
/ γ
M0
... (5.5)