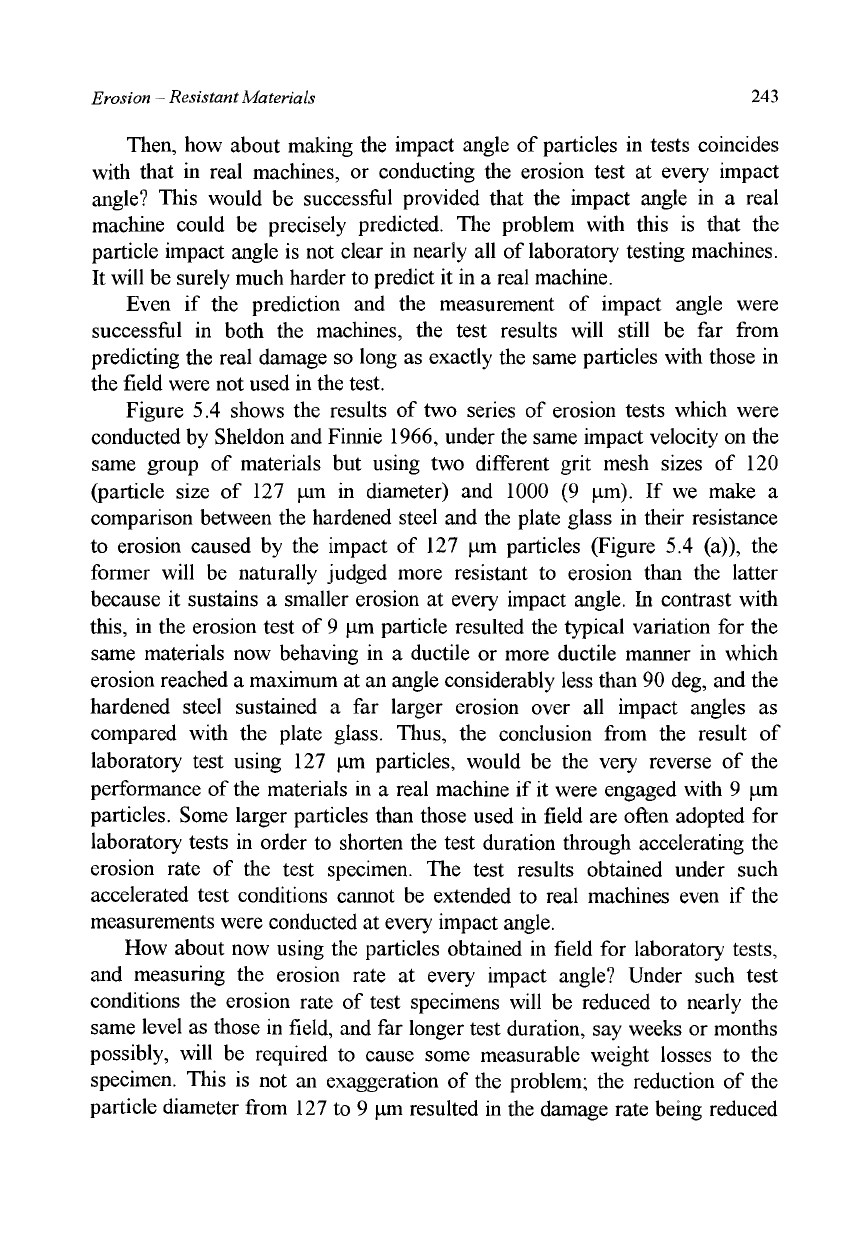
Erosion - Resistant Materials
243
Then, how about making the impact angle of particles in tests coincides
with that in real machines, or conducting the erosion test at every impact
angle? This would be successful provided that the impact angle in a real
machine could be precisely predicted. The problem with this is that the
particle impact angle is not clear in nearly all of laboratory testing machines.
It will be surely much harder to predict it in a real machine.
Even if the prediction and the measurement of impact angle were
successful in both the machines, the test results will still be far from
predicting the real damage so long as exactly the same particles with those in
the field were not used in the test.
Figure 5.4 shows the results of two series of erosion tests which were
conducted by Sheldon and Finnie 1966, under the same impact velocity on the
same group of materials but using two different grit mesh sizes of 120
(particle size of 127 urn in diameter) and 1000 (9 urn). If we make a
comparison between the hardened steel and the plate glass in their resistance
to erosion caused by the impact of 127 um particles (Figure 5.4 (a)), the
former will be naturally judged more resistant to erosion than the latter
because it sustains a smaller erosion at every impact angle. In contrast with
this,
in the erosion test of 9 um particle resulted the typical variation for the
same materials now behaving in a ductile or more ductile manner in which
erosion reached a maximum at an angle considerably less than 90 deg, and the
hardened steel sustained a far larger erosion over all impact angles as
compared with the plate glass. Thus, the conclusion from the result of
laboratory test using 127 urn particles, would be the very reverse of the
performance of the materials in a real machine if it were engaged with 9 um
particles. Some larger particles than those used in field are often adopted for
laboratory tests in order to shorten the test duration through accelerating the
erosion rate of the test specimen. The test results obtained under such
accelerated test conditions cannot be extended to real machines even if the
measurements were conducted at every impact angle.
How about now using the particles obtained in field for laboratory tests,
and measuring the erosion rate at every impact angle? Under such test
conditions the erosion rate of test specimens will be reduced to nearly the
same level as those in field, and far longer test duration, say weeks or months
possibly, will be required to cause some measurable weight losses to the
specimen. This is not an exaggeration of the problem; the reduction of the
particle diameter from 127 to 9 urn resulted in the damage rate being reduced