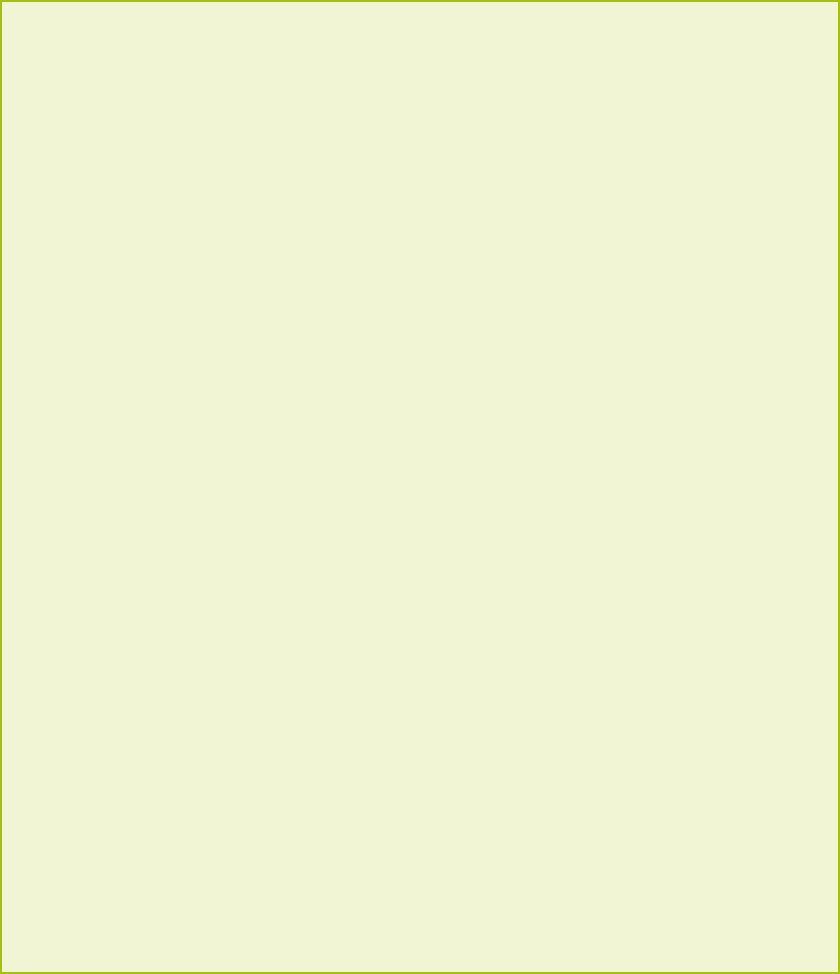
STUDY MATERIAL E1
106
OPERATIONS MANAGEMENT
of planning and control pulling work through the system in response to customer demand.
The obvious advantage of JIT is the elimination of large stocks of materials and parts. JIT
purchasing involves a system whereby ‘material purchases are contracted so that the receipt
and usage of material, to the maximum extent possible, coincide’ (CIMA, 2005). Put simply
the stock of raw materials is reduced to near-zero levels. Financial savings are easily apparent
as is the requirement to foster an effective working relationship with suppliers.
JIT approaches are often undertaken in parallel with TQM. TQM facilitates the intro-
duction of JIT because JIT is not feasible with, for example, high reject rates and high
wastage in manufacturing, and TQM reduces these. A form of risk assessment in the pro-
duction department often takes place. The impact of production delays and stock-outs if
the JIT system fails has implications. A decision on whether to accept the risk or, perhaps,
to carry buffer stocks must be made.
The extract from the following article explains how crucial just-in-time (JIT) deliveries
are to optimising space in retail outlets.
For all the attention focused on supply chain processes, from global sourcing to the
end consumer, very little discussion is dedicated to how shipments are received into
stores. The reason is perhaps quite pragmatic: Few retailers are willing to talk about
what happens in their back rooms. When approached for this story, most declined to
comment. However, there is a clear consensus among retailer expectations: Inventory
should fl ow from the back room to the store fl oor as quickly as possibly. Back rooms,
kept to a minimum footprint, are for processing shipments, not for storage.
. . . . . . . . .
Reliance on transportation carriers and third-party logistics providers for store-
level logistics has become a dominant trend. The ultimate goal is to manage store
deliveries so that store resources, specifi cally back-room space and labour, are utilised
most effi ciently and in-stock positioning is optimised.
. . . . . . . . .
Pharmacies in traditional drug stores as well as in grocery and super-store formats
have some of the most stringent requirements for JIT deliveries. Every inch of every
footprint is at a premium, and neither the pharmacist nor technicians has time to
receive shipments.
‘A pharmacy retailer may need to receive deliveries before 6 a.m. to replenish stock
or at a defi ned time slot when they have scheduled clerks specifi cally for receiving
deliveries.’ noted Drew Kronick, executive VP of business development and supply
chain solutions for Velocity Express.
A national home-accessories and lifestyle retailer began using Velocity Express
for furniture replenishment about 18 months ago. In a targeted Northeastern mar-
ket where the retailer operates approximately 30 stores, Velocity Express makes daily
deliveries to the stores, and in some cases may deliver multiple times to a single store.
Valuable square footage that was once dedicated to back-room storage has been con-
verted to selling space, and replenishment inventory of large furnishings is held in a
centralised location. When furniture sells from the store fl oor, Velocity Express picks
up at the central warehouse and delivers to the store that same day.
The JIT service is designed to deliver to whatever parameters the retailers set. In
markets where there is a critical mass of stores, a fl eet of trucks and drivers may be
dedicated to a specifi c retailer.
Source: Robbins Gentry, C. (2007) Back-room secrets. Chain Store Age, March.