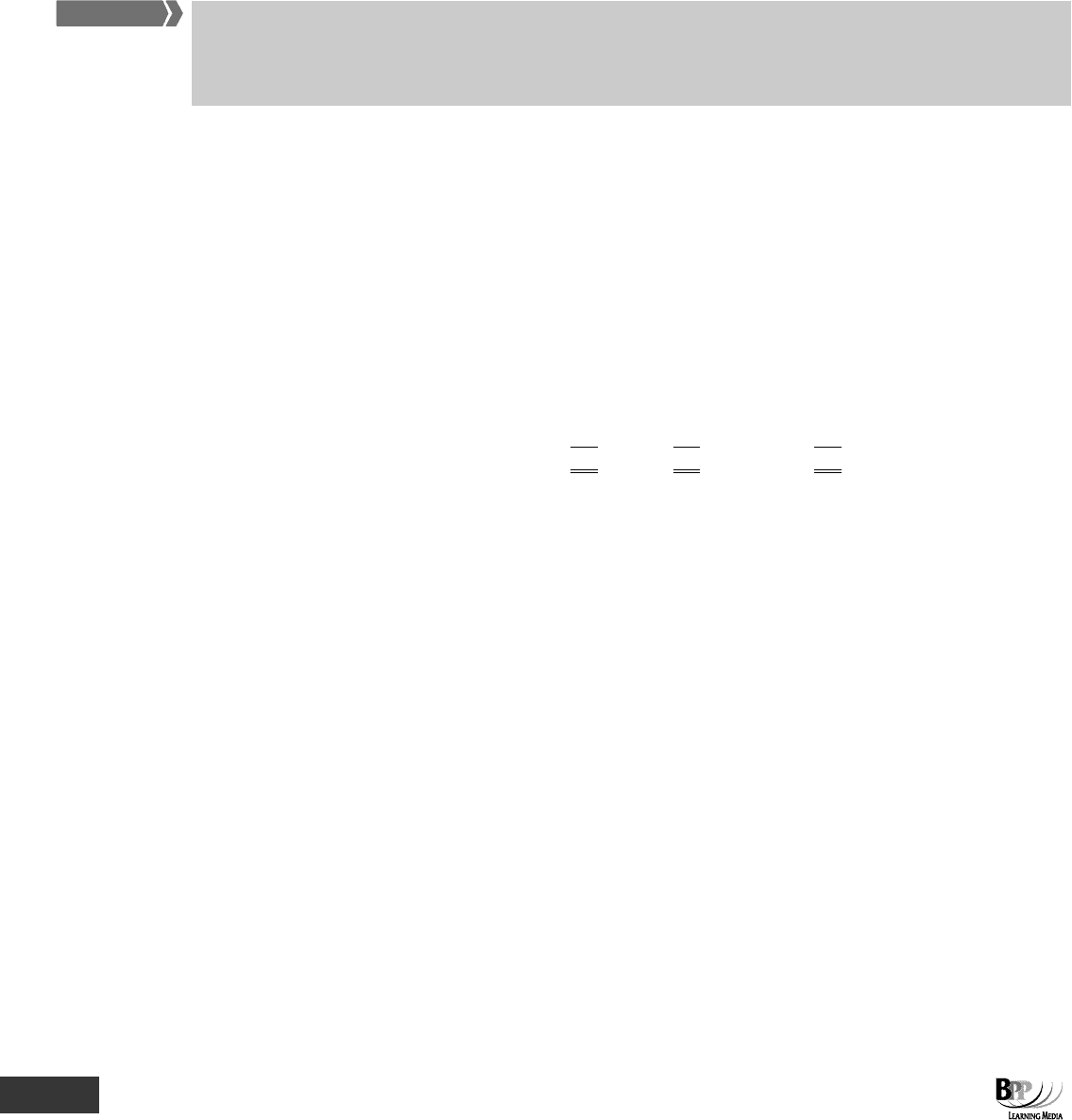
176 11: Cost of goods sold and inventories ⏐ Part B Accounting systems and accounts preparation
In more complicated cases, an alternative approach to establishing inventory quantities is to maintain continuous
inventory records. This means that a card is kept for every item of inventory, showing receipts and issues from the
stores, and a running total. A few inventory items are counted each day to make sure the record cards are correct. This is
called a
'continuous' inventory count because it is spread out over the year.
4 Valuing inventories
Inventory is valued in accordance with the prudence concept at the lower of cost and net realisable value (NRV). Cost
comprises purchase costs and costs of conversion.
Net realisable value is the selling price less all costs to completion and less selling costs.
4.1 Applying the basic valuation rule
If a business has many inventory items on hand, the comparison of cost and NRV should be carried out for each item
separately. It is not sufficient to compare the total cost of all inventory items with their total NRV.
4.2 Example: closing inventory
A company has four items of inventory and their cost and NRVs are as follows.
Inventory item
Cost
NRV
Lower of cost/NRV
$
$
$
1
27
32
27
2
14
8
8
3
43
55
43
4
29
40
29
113
135
107
What is the value of closing inventory?
Solution
It would be incorrect to compare total costs ($113) with total NRV ($135) and to state inventories at $113 in the
statement of financial position. The company can foresee a loss of $6 on item 2 and this should be recognised. By
performing the cost/NRV comparison for each item separately the prudent valuation of $107 can be derived. This is the
value which should appear in the statement of financial position.
However, for a company with large amounts of inventory this procedure may be impracticable. In this case it is
acceptable to group similar items into categories and perform the comparison of cost and NRV category by category,
rather than item by item.
4.3 Determining the purchase cost
Inventory may be raw materials or components bought from suppliers, finished goods which have been made by the
business but not yet sold, or work in the process of production, but only part-completed (this is called work in progress
or WIP). It will simplify matters, however, if we think about the cost of purchased raw materials and components.
A business may be continually purchasing a particular component. As each consignment is received from suppliers they
are stored in the appropriate 'bin', where they will be mingled with previous consignments. When the storekeeper issues
components to production, he will simply pull out the nearest components to hand, which may have arrived in the latest
consignment or in an earlier consignment or in several different consignments.
There are several techniques to attribute cost to the components.
FA
T F
RWAR
197465 www.ebooks2000.blogspot.com