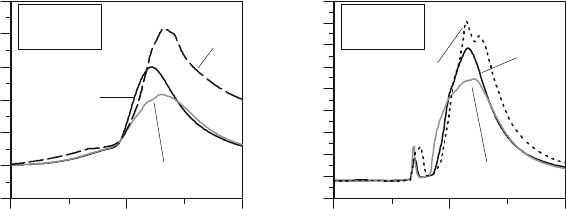
162 10 3D-CFD-Modeling of the Wall Heat-Transfer
Figure 10.16: Average heat-transfer flux
through the cylinder-liner walls.
Figure 10.17: Average heat-transfer flux
through the spark plug walls.
Concluding the analysis of the heat-transfer flux using the wall-function approach (see Figures
10.11-10.12) reports the extreme high sensitivity of the heat-transfer flux with the mesh. The
results of the different simulations show variations of about 500% in the prediction of the local
heat-flux (in certain cases even more) and up to 100% in the prediction of the overall heat-
transfer energy
W
Q
(J/cycle). The resulting predictability in the calculation of the heat-transfer
and the energy balance is obviously not acceptable for a reliable engine analysis.
10.2.5 QuickSim’s Approach: A new Phenomenological Heat-
Transfer Model in the 3D-CFD-Simulation
In this work a three-dimensional phenomenological heat-transfer coefficient
MD ,x
&
, which is
based on the before described Re-Nu-correlations (see Chapters 10.2.3.3 and 10.2.3.4), is
proposed for both the working cycle
MD ,
1
x
&
and the charge changing period
MD ,
2
x
&
. This
model is implemented locally, like the wall function, in only a single wall-cells layer, so that
computing overheads are not caused. The classic wall function is still used for assuring the no-
slip velocity condition and the temperature condition at the wall.
The modeling of the heat-transfer coefficients chosen for the 3D-CFD-simulation, similarly to
the real working-process analysis, is based on the following correlations [21,22]:
x
Bargende’s correlation during the compression and expansion stroke (working cycle).
x
Hohenberg’s correlation during the intake and exhaust stroke (gas exchange period).
2000 rpm -
WOT
Thin
layer
Fine
Standard &
Bad SP
Cy
.
ne
HT f
ux, M
/m
-0.2
0.0
0.2
0.4
0.6
0.8
1.0
Crank an
le
, de
630 FTDC 810
2000 rpm -
WOT
Standard &
Thin layer
Fine
Bad SP
Cy
. spa
k p
ug HT f
ux, M
/m
-0.2
0.0
0.2
0.4
0.6
0.8
1.0
1.2
1.4
1.6
Crank an
le
, de
630 FTDC 810