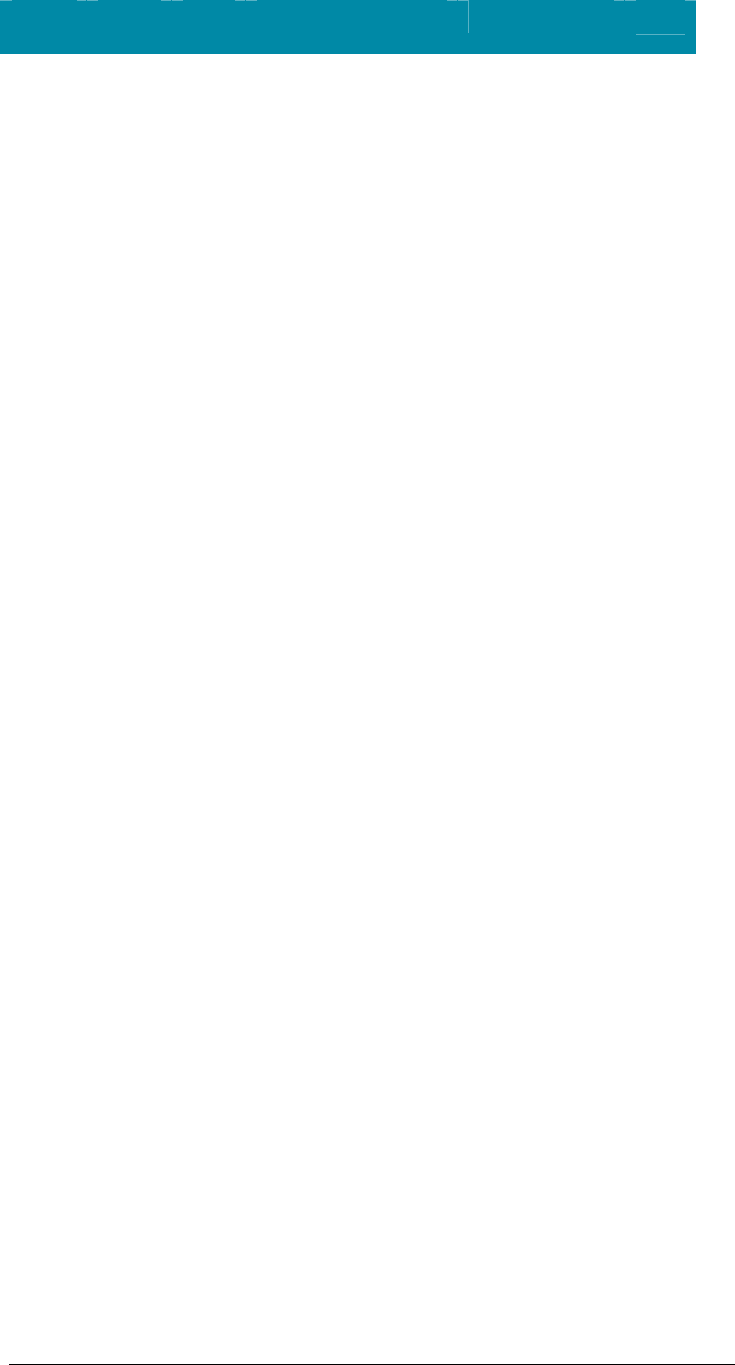
Group Grade Type Process of
Manufacture
Heat Treatment
°F
tempered (Q&T) at the manufacturer's option or if so specified on the purchase
order.
Grades of steel with letter designations other than those designated in Table 3-1
for instance, HC-95 and C-110, are not recognized by API and are not controlled
by API manufacturing and inspection requirements. The manufacturing and
quality requirements are those agreed to by the end user and the manufacturer.
3.4 Manufacturing Process
The manufacturing process is either seamless (SMLS) or electric resistance-
welded (ERW). The SMLS process takes a solid billet, usually round, that is
heated and rotary pierced. After piercing, the billet is elongated and the walls
thinned to produce a seamless tube. Several different types of equipment are
used to produce seamless pipe. The plug mill, pilger mill, mandrel mill, and
retained mandrel mill are examples.
The ERW process takes a continuous coil of flat steel with the desired final wall
thickness, called “skelp,” forms it into a round tube and welds the longitudinal
seam. The high-frequency welder heats the edges of the rounded coil to around
1400
o
C (2600°F). The edges are squeezed together to produce a forge weld. No
filler or welding rod is used. The resulting internal and external weld flash is
removed. Individual joints are then cut from this continuous tube.
As indicated in Table 3-1, a specified method of full-length heat treatment is
given for each grade. The heat treatment of SMLS and ERW pipe takes place
after rolling and ranges from “as rolled” (none) for some Group 1 grades to
“quenched and tempered” (Q&T) for grades in Groups 2, 3, and 4. Grades J-55,
K-55, and N-80 may also be heat-treated using the normalized (N) or normalized
and tempered (N&T) methods. Heat treatment is required to obtain the higher
yield strengths and develop desired ductility and toughness.
• The Q&T process involves heating individual tubes to approximately 870-
930°C (1600 to 1700°F) in an austenizing furnace, and then the tubes soak
at this temperature for a specified amount of time depending on the
chemistry of the steel, the thickness pipe, and the specific mill. The evenly
heated tube is then rapidly quenched, or cooled, to below 93°C (200°F) using
water or oil as the cooling medium. After quenching, the pipe is reheated, or
tempered, to approximately 560 to 650°C (1050 to 1200°F) in a tempering
furnace and then allowed to air cool to room temperature.
• The N&T process involves heating individual tubes in an austenizing furnace,
allowing the tubes to air cool, reheating them in the tempering furnace, and
then allowing them to air cool to room temperature again.
• “Normalizing” involves heating individual tubes in an austenizing furnace and
allowing the tubes to air cool to room temperature.
ERW pipe must also have the weld seam heat-treated, or seam annealed to
above 540°C (1000°F) to relieve the stresses of welding and produce a
Casing/Tubing Design Manual 3-3
October 2005