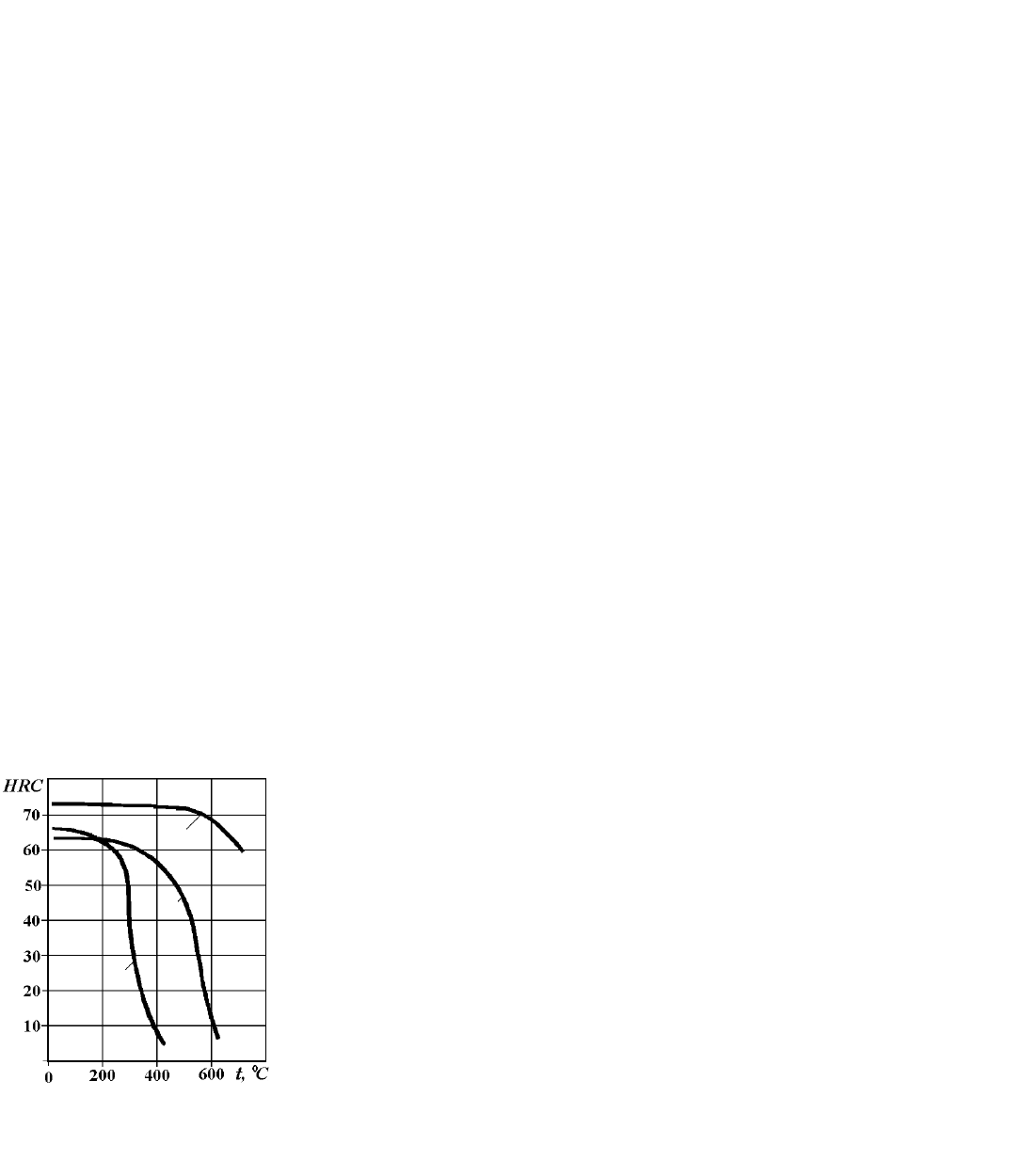
Лабораторная работа 12
ТЕПЛОСТОЙКОСТЬ ИНСТРУМЕНТАЛЬНЫХ СТАЛЕЙ
Цель работы
: ознакомиться с понятием теплостойкости (красностойкости), структурными изменениями,
происходящими при нагревании инструментальных сталей.
Приборы и оборудование
: электропечи, твердомер Роквелла.
Краткая теория
Основные материалы для режущего инструмента делятся на углеродистые, малолегированные, быстрорежущие стали и
металлокерамические твердые сплавы. В рабочем состоянии стали должны иметь твёрдость не ниже 60…64
HRC
. Такую
твёрдость обеспечивает закалка с последующим низким отпуском для снятия остаточных напряжений на структуру
мартенсита отпуска. Если в результате закалки кроме мартенсита получается остаточный аустенит (твёрдость которого
невелика), это компенсируют наличием в нем мелкодисперсных карбидов железа (Ц
II
) и легирующих элементов.
В процессе резания выделяется большое количество тепла, которое приводит к разогреву режущей кромки
инструмента. Чем выше скорость резания, тем больше температура инструмента.
Красностойкость
(
теплостойкость
)
инструментальной стали
определяется максимальной температурой, до которой она
сохраняет свою высокую твёрдость.
Снижение твёрдости инструмента при нагревании определяется процессами, протекающими при IV превращении в
сталях: распадом мартенсита и коагуляцией (укрупнением карбидных частиц). Легирование мартенсита стали тугоплавкими
элементами (вольфрамом, молибденом, ванадием, хромом) уменьшает скорость диффузии и тем замедляет эти процессы,
сдвигая их к более высокой температуре и увеличивая теплостойкость. Эти элементы при нагревании мартенсита до
550…600 ºС связывают выделяющийся из него углерод в карбидные фазы, причем карбиды мелкодисперсные. Процесс
называют дисперсионным твердением. Имея более высокую твёрдость, чем мартенсит, карбиды увеличивают твердость
быстрорежущих сталей при нагревании.
По теплостойкости применяемые материалы подразделяют на:
• нетеплостойкие, сохраняющие твёрдость до 200 °С (углеродистые У7, У8, У13 и низколегированные стали 9ХФ,
9ХС, 13Х, В2Ф);
• полутеплостойкие – до 400…500 °С (среднелегированные стали Х6ВФ, Х6Ф4М, Х12М);
• теплостойкие – до 600…650 °С (высоколегированные быстрорежущие стали Р18, Р6М5, Р6М5Ф3, Р6М5К5);
• с повышенной теплостойкостью – до 800…1000 °С (металлокерамические твёрдые сплавы ВК8, Т5К10, ТТ7К12).
Углеродистые и малолегированные инструментальные стали применяют при изготовлении инструмента для резания с
малыми скоростями, когда не происходит сильный разогрев режущей кромки.
Высокие режущие свойства быстрорежущей стали нормальной производительности обеспечиваются за счёт
легирования сильными карбидообразующими элементами: вольфрамом, молибденом, ванадием (Р18, Р6М5, Р9).
Стали повышенной производительности (теплостойкость 625…640 °С) дополнительно легированы кобальтом и
ванадием. К ним относятся вольфрамокобальтовые стали (Р9К10), вольфрамованадиевые (Р9Ф5, Р12Ф3),
вольфрамованадиевые с кобальтом (Р10Ф5К5, Р12Ф4К5), вольфрамованадиевые с кобальтом и молибденом (Р12Ф3К10М3,
Р12Ф2К5М3).
К группе быстрорежущих сталей повышенной производительности относят также дисперсионно-твердеющие сплавы с
интерметаллидным упрочнением. Их высокая теплостойкость обеспечивается высокой температурой перехода α → γ и
выделением при отпуске интерметаллидов, имеющих более высокую устойчивость к
коагуляции при нагреве, чем карбиды (Р10М5К25), а значит более высокую твёрдость.
Металлокерамические твердые сплавы, составленные из карбидов вольфрама,
титана, в связке из кобальта, сохраняют режущие свойства до 1000 °С. Их применяют для
резания с повышенной скоростью труднообрабатываемых материалов.
Характеристики теплостойкости различных инструментальных материалов
приведены на рис. 1.
Порядок выполнения работы
1. Получить образцы инструментальных материалов, подвергнутых закалке и
низкому отпуску.
2. Измерить твёрдость каждого образца по Роквеллу.
3. Поместить образцы в печь, разогретую до температур, указанных ниже.
Выдержать 40 мин и затем охладить их на воздухе:
а) углеродистые стали до 250, 300, 350, 400 °С;
б) быстрорежущие стали до 500, 600, 650, 700 °С;
в) металлокерамические сплавы до 800, 900, 1000, 1100 °С.
4. Измерить твёрдость образцов после нагревания, и результаты для каждой стали
занести в табл. 1.
Рис. 1. Красностойкость
инструментальных сталей:
1
– углеродистые;
2
– быстрорежущие;
3
– твёрдые сплавы (пересчет на
HRC
)