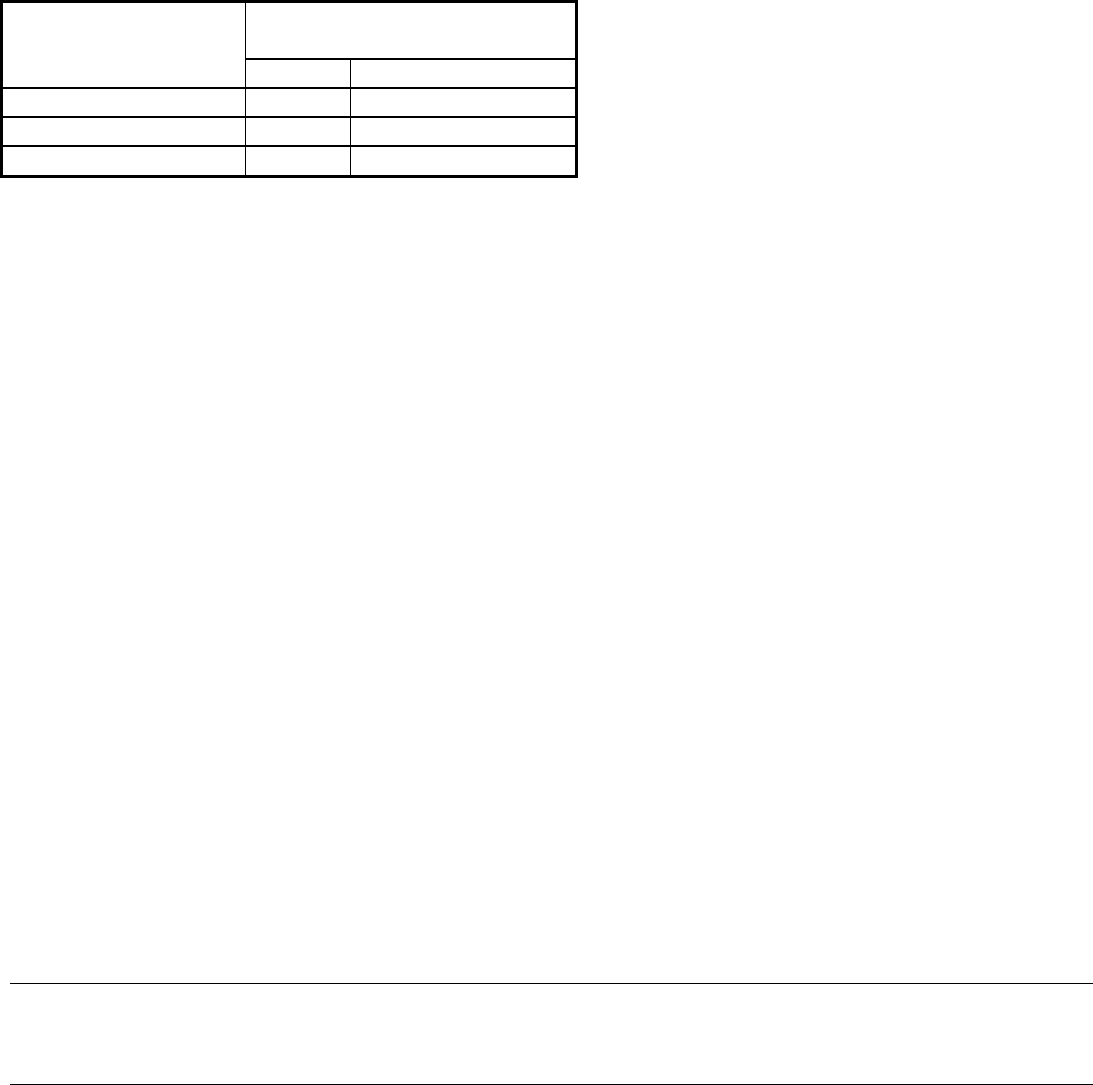
High degrees of multiaxiality can be found especially at notch roots or in front of a crack tip. Also, in the soft
zone of the heat-affected zone of a weld there is a strong element of tensile triaxiality, which will have an effect
on the life.
The multiaxial ductility for our model tube (R
i
= 0.6R
o
) gives the values shown in Table 1 when calculated
using the Eq 32 and 34. This result is extremely important because it explains the discrepancy between the two
observations:
• Creep stress analysis for a cylindrical body gives always the maximum effective stress values on the
inner surface of the tube.
• The service experience shows that the creep damage always appears on the outer surface of the tube—at
least for materials other than the most brittle ones.
Table 1 Ratio of multiaxial and uniaxial ductility calculated at various locations in the wall of a tube
Ratio of multiaxial ductility to
uniaxial ductility
Location on tube wall
1/TF
(a)
1.65 exp(-3h/2)
(b)
Inner surface 7.60 1.54
Mid wall 1.01 1.00
Outer surface 0.58 0.69
Tube has a ratio of inner radius to outer radius of 0.6.
(a) See Eq 34.
(b) See Eq 32.
In a creeping tube, the strains are proportional to 1/radius. Therefore, both the effective stress and the strain on
the inner surface of the tube are the highest, but the multiaxial ductility is clearly higher than the uniaxial
ductility, as shown in Table 1. This is why the damage does not initiate on the inside of the tube (except in
materials where the uniaxial creep ductility is very low—then the relaxation of the high initial elastic stresses
can cause failure on the inside). On the other hand, according to Eq 32 and 34, the ductility on the outer surface
is much less than the uniaxial ductility, which leads to the initiation of the damage on the outer surface first.
Fortunately, the nature of creep rupture itself seems to simplify the problem of multiaxiality in plant
components. In long-term service, creep rupture occurs with a constrained grain-boundary cavity nucleation
and growth mechanism, it seems to be more MPS controlled, and damage appears predominantly on the outer
surface (which is fortunate from an inspection point of view).
This finding could simplify the necessary engineering calculations of multiaxial stress systems to some extent.
However, the present-day design codes for plant equipment do not necessarily reflect this idea, although design
lives can be well above 100,000 h where MPS would become the controlling parameter. Further, it should be
remembered that for components in the creep regime, the MPS should not be calculated according to the initial
elastic distribution but according to the steady-state creep stress distribution.
References cited in this section
9. P. Segle, P. Andersson, and L.Å. Samuelson, A parametric study of creep crack growth in
heterogeneous CT specimens by use of finite element simulations, Mater. High Temp., Vol 15, 1998, p
101
10. B.W. Roberts, Influence of Multiaxial Stressing on Creep and Creep Rupture, Mechanical Testing, Vol
8, ASM Handbook, ASM International, 1985, p 343–345
Influence of Multiaxial Stresses on Creep and Creep Rupture of Tubular Components
R.C. Hurst and J.H. Rantala, European Commission, Joint Research Centre, Institute for Advanced Materials (The Netherlands)