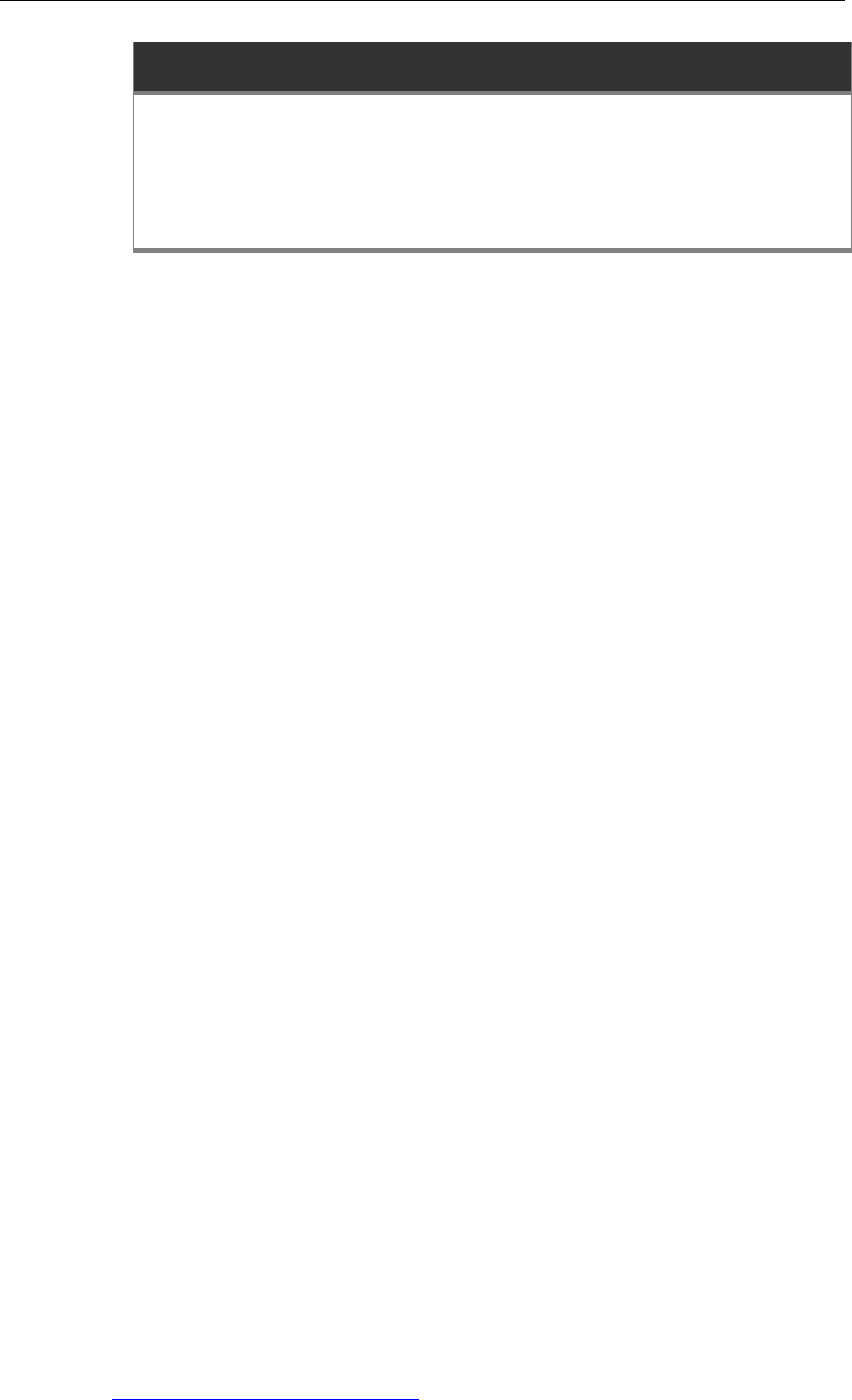
Paper F9: Financial management
86 Go to www.emilewoolfpublishing.com for Q/As, Notes & Study Guides © EWP
Reorder level and buffer stock
Minimising materials costs
Holding costs and ordering costs
Economic order quantity (EOQ)
EOQ: changes in the variables in the formula
2 Reorder level and buffer stock
2.1 Inventory reorder level and other warning levels
So far, it has been assumed that when an item of materials is purchased from a
supplier, the delivery from the supplier will happen immediately. In practice,
however, there is likely to be some uncertainty about when to make a new order for
materials in order to avoid the risk of running out of inventory before the new order
arrives from the supplier. There are two reasons for this.
There is a supply ‘lead time’. This is the period of time between placing a new
order with a supplier and receiving the delivery of the purchased items. The
length of this supply lead time might be uncertain and might be several days,
weeks or even months.
The daily or weekly usage of the material might not be a constant amount.
During the supply lead time, the actual usage of the material may be more than
or less than the average usage.
If demand for an inventory item exceeds the available quantity of inventory during
the reorder period, there will be a stock-out (inventory-out). When there is a stock-
out of a key item of materials, there might be a hold-up in production and a
disruption to the production schedules. This in turn may lead to a loss of sales and
profits. Stock-outs therefore have a cost.
Management responsible for inventory control might to know:
what the reorder level should be for each item of materials, in order to avoid any
stock-out: the reorder level is the level of inventory at which a new order for the
item should be placed with the supplier
whether the inventory level for each item of material appears to be too high or
too low
what the reorder level should be for each item of materials, if stock-outs can be
allowed to happen.
In an inventory control system, if there is uncertainty about the length of the supply
lead time and demand during the lead time there might be three warning levels for
inventory, to warn management that:
the materials item should now be reordered (the reorder level)
the inventory level is too high (a maximum inventory level) or
the inventory level is getting dangerously low (a minimum inventory level).