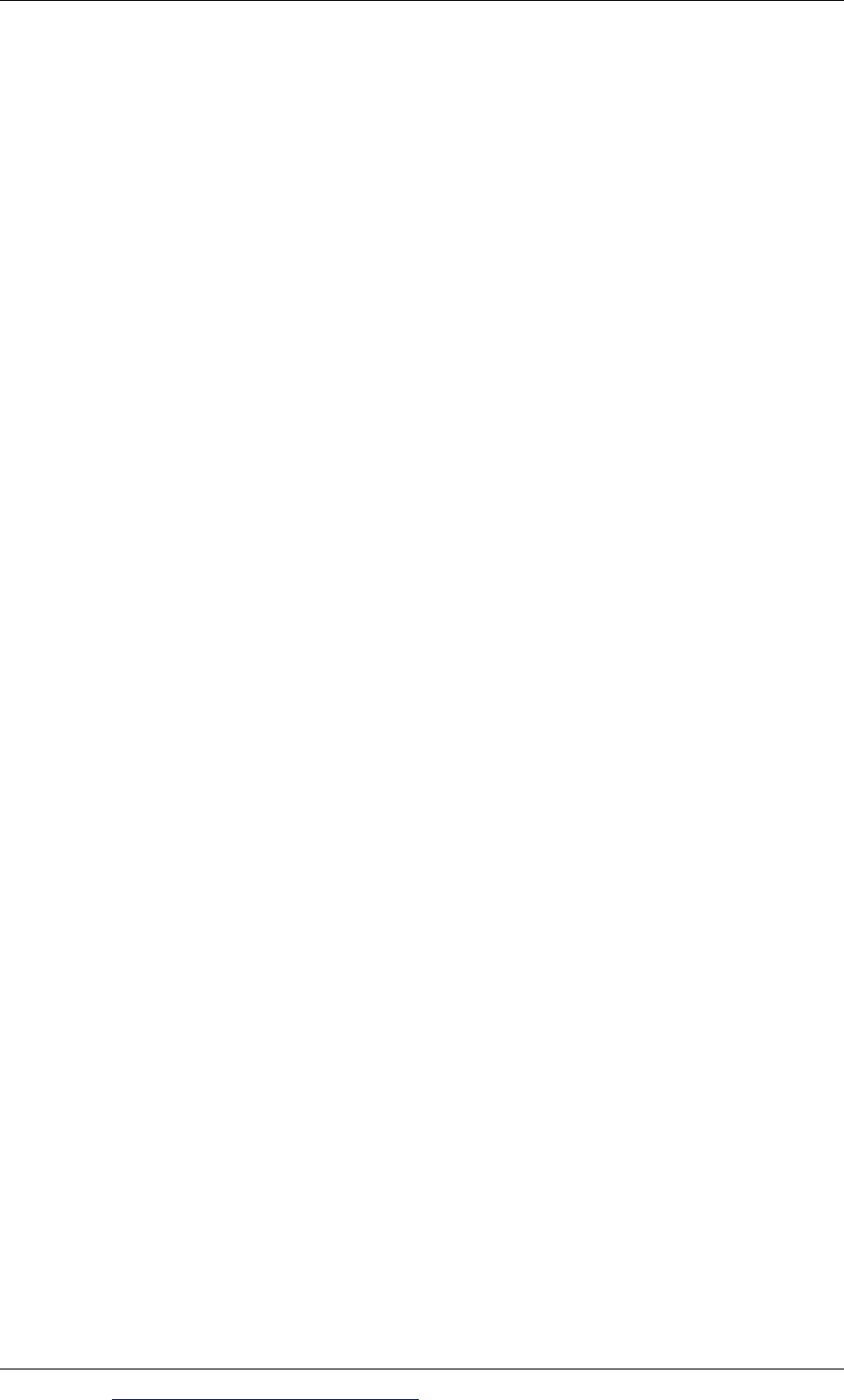
F5: Performance management
46 Go to www.emilewoolfpublishing.com for Q/As, Notes & Study Guides © EWP
Transfers between processes are often made at standard cost, and any variances are
taken directly as a total variance to the income statement as a gain or a loss.
3.3 Traditional costing systems and back-flush accounting compared
Traditional costing systems
Traditional cost accounting systems for manufacturing costs are ‘sequential
tracking’ systems. They track the costs of items as they progress through the
manufacturing process, from raw materials, through work in progress to finished
goods. At each stage of the manufacturing process, more costs are added and
recorded within the cost accounting system.
Raw material costs are recorded in a raw materials inventory account when the
materials are purchased. When the raw materials are issued to production, a
record is made in the cost accounts of the cost of materials issued to production,
often using FIFO or weighted average costs to measure the cost of the materials.
Direct labour costs are recorded in a direct labour cost account, and then
transferred to the work in progress account.
Production overhead costs are calculated by absorbing overheads into
production costs at a pre-determined overhead absorption rate. At the end of the
period there will be some over- or under-absorbed overheads. Under-absorption
is reduced or over-absorption is increased by maximising production volume.
The main benefit of sequential tracking costing systems is that they can be used to
put a cost to items of inventory. When inventory is large, there is a need to measure
inventory costs with reasonable ‘accuracy’.
Features of back-flush accounting
As the term ‘back-flush’ might suggest, and as explained earlier, costs are calculated
after production has been completed. They are allocated between the cost of goods
sold and inventories in retrospect. They are not built up as work progresses through
the production process.
Back-flush accounting is a method of cost accounting that is consistent with JIT.
With a system of JIT purchasing and production, the benefit of ‘accurate’ costing of
inventory does not exist, or is insignificant. Inventory should be small, or even non-
existent. The cost of inventory is therefore fairly insignificant. A costing system that
measures the cost of inventory is therefore of little or no value, and is certainly not
worth the time, effort and expenditure involved.
With back-flush accounting, there is no work-in-progress account in the costing
system. The only inventory accounts in the costing system are an account for
finished goods and (possibly) an account for raw materials.
However there is no need to value raw materials inventory using FIFO or
weighted average cost.
Back-flush accounting also keeps no records of direct labour times and direct
labour costs. Labour costs are included with other expenses in a single account
for ‘conversion costs’. Consequently, the system does not record any direct