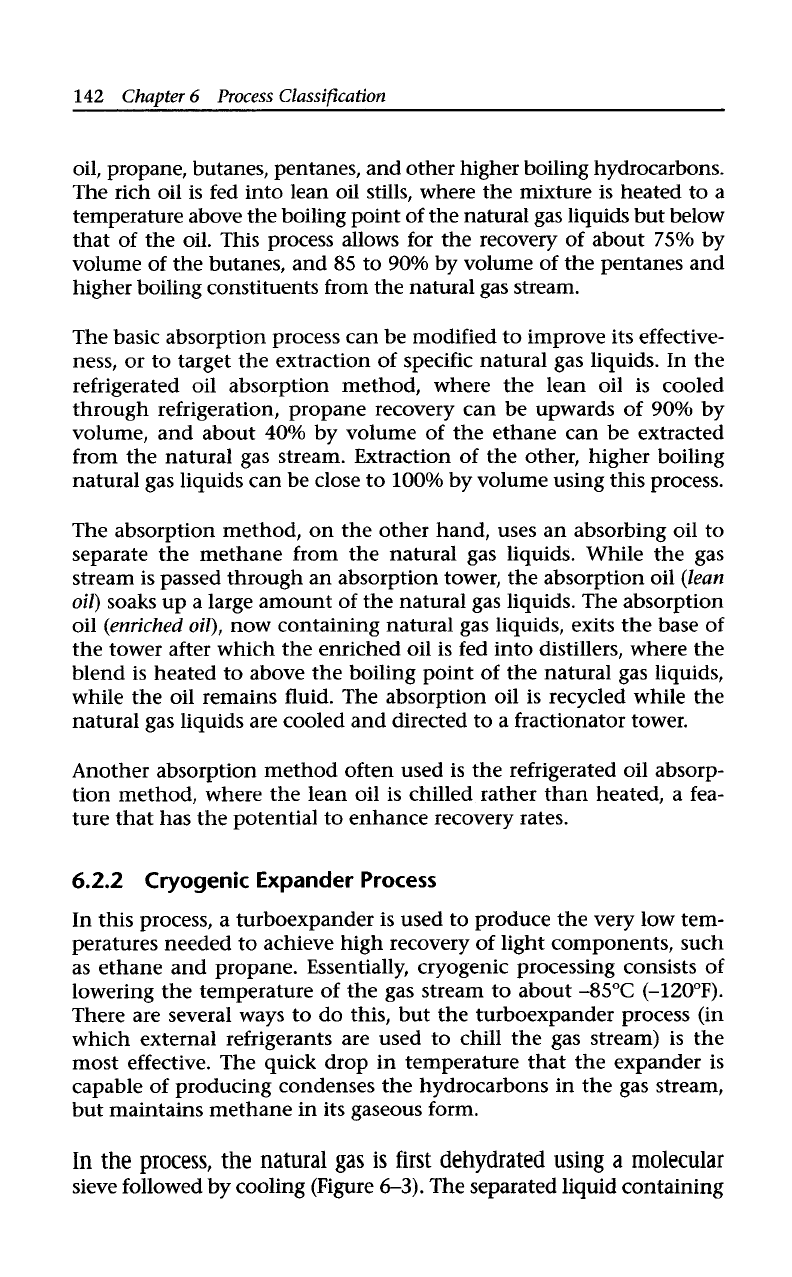
142
Chavter
6
Process Classification
oil, propane, butanes, pentanes, and other higher boiling hydrocarbons.
The rich oil is fed into lean oil stills, where the mixture is heated
to
a
temperature above the boiling point of the natural gas liquids but below
that
of
the oil. This process allows
for
the recovery
of
about 75% by
volume of the butanes, and 85 to
90%
by volume of the pentanes and
higher boiling constituents from the natural gas stream.
The basic absorption process can be modified to improve its effective-
ness, or to target the extraction
of
specific natural gas liquids.
In
the
refrigerated oil absorption method, where the lean
oil
is cooled
through refrigeration, propane recovery can be upwards
of
90%
by
volume, and about
40%
by volume
of
the ethane can be extracted
from the natural gas stream. Extraction
of
the other, higher boiling
natural gas liquids can be close to
100%
by volume using this process.
The absorption method,
on
the other hand, uses an absorbing oil to
separate the methane from the natural gas liquids. While the gas
stream is passed through an absorption tower, the absorption oil
(lean
oil)
soaks up a large amount
of
the natural gas liquids. The absorption
oil
(enriched oil),
now containing natural gas liquids, exits the base of
the tower after which the enriched oil is fed into distillers, where the
blend is heated
to
above the boiling point
of
the natural gas liquids,
while the oil remains fluid. The absorption oil is recycled while the
natural gas liquids are cooled and directed to a fractionator tower.
Another absorption method often used is the refrigerated oil absorp-
tion method, where the lean oil is chilled rather than heated, a fea-
ture that has the potential to enhance recovery rates.
6.2.2
Cryogenic Expander Process
In
this process, a turboexpander is used to produce the very low tem-
peratures needed to achieve high recovery
of
light components, such
as ethane and propane. Essentially, cryogenic processing consists
of
lowering the temperature
of
the gas stream
to
about -85°C
(-120°F).
There are several ways
to
do this, but the turboexpander process (in
which external refrigerants are used to chill the gas stream) is the
most effective. The quick drop in temperature that the expander is
capable
of
producing condenses the hydrocarbons in the gas stream,
but maintains methane in its gaseous form.
In
the process, the natural gas
is
first dehydrated using a molecular
sieve followed by cooling (Figure
6-3).
The separated liquid containing