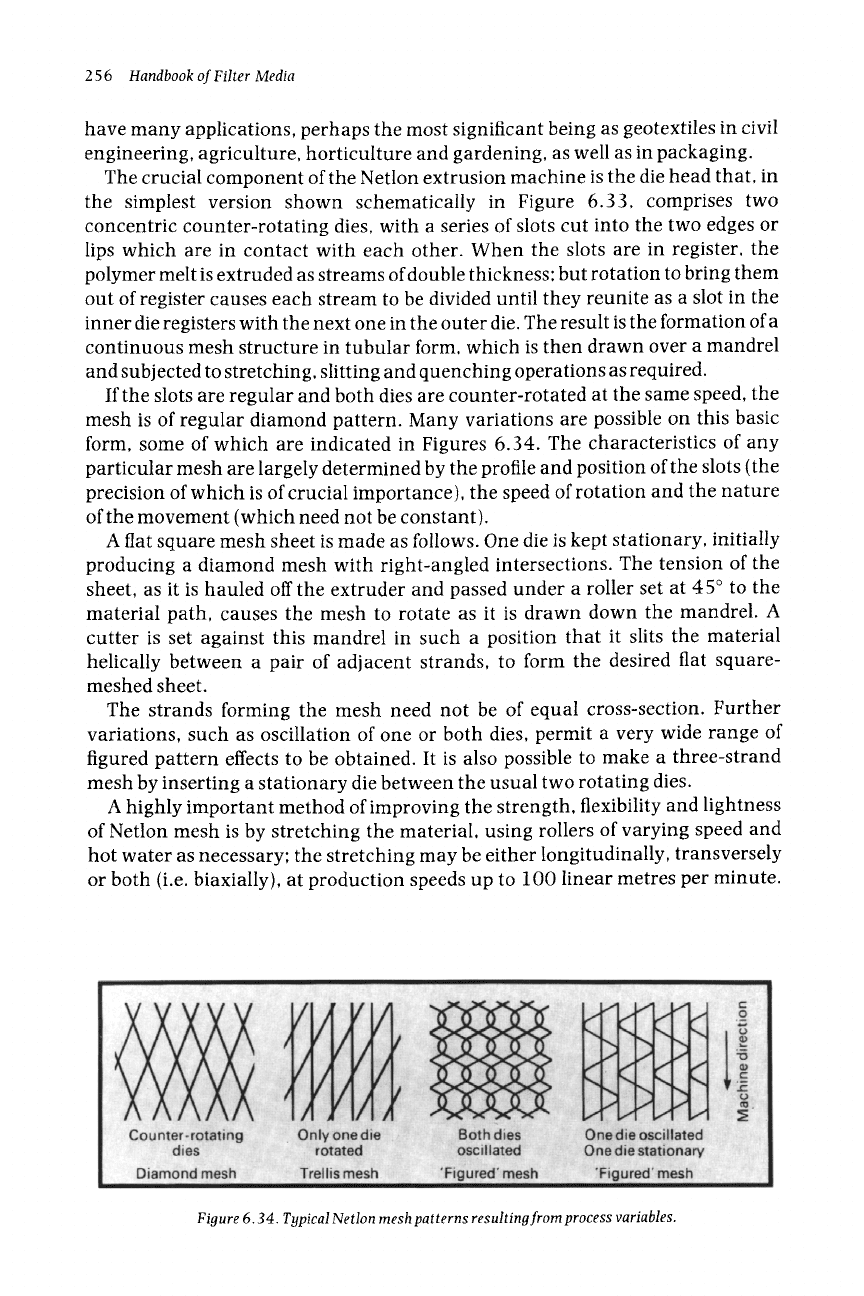
256 Handbook of Filter Media
have many applications, perhaps the most significant being as geotextiles in civil
engineering, agriculture, horticulture and gardening, as well as in packaging.
The crucial component of the Netlon extrusion machine is the die head that, in
the simplest version shown schematically in Figure 6.33, comprises two
concentric counter-rotating dies, with a series of slots cut into the two edges or
lips which are in contact with each other. When the slots are in register, the
polymer melt is extruded as streams of double thickness: but rotation to bring them
out of register causes each stream to be divided until they reunite as a slot in the
inner die registers with the next one in the outer die. The result is the formation of a
continuous mesh structure in tubular form, which is then drawn over a mandrel
and subjected to stretching, slitting and quenching operations as required.
If the slots are regular and both dies are counter-rotated at the same speed, the
mesh is of regular diamond pattern. Many variations are possible on this basic
form, some of which are indicated in Figures 6.34. The characteristics of any
particular mesh are largely determined by the profile and position of the slots (the
precision of which is of crucial importance), the speed of rotation and the nature
of the movement (which need not be constant).
A flat square mesh sheet is made as follows. One die is kept stationary, initially
producing a diamond mesh with right-angled intersections. The tension of the
sheet, as it is hauled off the extruder and passed under a roller set at 45 ~ to the
material path, causes the mesh to rotate as it is drawn down the mandrel. A
cutter is set against this mandrel in such a position that it slits the material
helically between a pair of adjacent strands, to form the desired flat square-
meshed sheet.
The strands forming the mesh need not be of equal cross-section. Further
variations, such as oscillation of one or both dies, permit a very wide range of
figured pattern effects to be obtained. It is also possible to make a three-strand
mesh by inserting a stationary die between the usual two rotating dies.
A highly important method of improving the strength, flexibility and lightness
of Netlon mesh is by stretching the material, using rollers of varying speed and
hot water as necessary; the stretching may be either longitudinally, transversely
or both (i.e. biaxially), at production speeds up to 100 linear metres per minute.
Figure O. 34. Typical Netlon mesh patterns resulting from process variables.